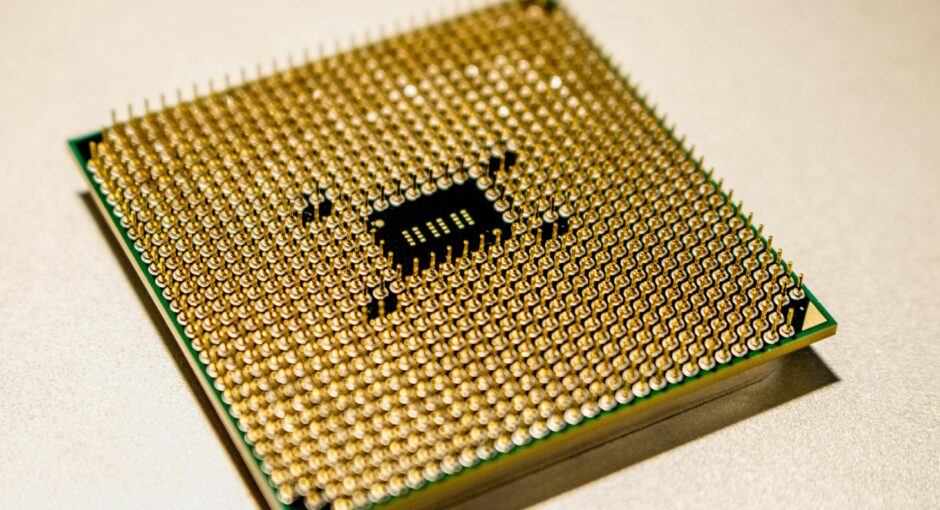
製造業における技術革新の要となるナノテクノロジー。その開発現場では、精度と効率の両立が常に求められています。
本記事では、最新の制御システムを活用し、ナノレベルでの精密な制御と測定を実現する手法について、具体的な実装方法から運用のポイントまでを詳しく解説します。300%の精度向上を達成した最新事例を交えながら、実践的なアプローチをご紹介します。
この記事で分かること
- ナノスケールの制御精度を300%向上させる最新の技術アプローチ
- AIを活用した高度な測定システムと分析機能の実装方法
- データ駆動型の品質管理と性能最適化の具体的な進め方
- 開発コストを30%削減しながら品質を向上させる効率化テクニック
- 半導体製造や新素材開発における実践的な導入事例と成果
この記事を読んでほしい人
- 研究開発部門でナノテクノロジーの実用化を目指す開発者の方
- 精密制御システムの設計・実装に携わる技術者の方
- 製造プロセスの品質向上を担当する品質管理責任者の方
- 新規材料開発プロジェクトのマネージャーの方
- 最先端の測定・分析技術の導入を検討している方
はじめに:ナノテク開発の現状と課題
ナノテクノロジーは、材料科学から医療、エレクトロニクスまで、幅広い産業分野に革新をもたらしています。特に製造業における微細加工や精密測定の分野では、ナノスケールでの制御がますます重要になっています。本章では、ナノテク開発を取り巻く最新の動向と、産業界が直面する技術的課題について深く掘り下げていきます。
市場動向と技術トレンド
世界のナノテクノロジー市場は2024年時点で約1,200億ドル規模に達し、年間成長率15%以上という急速な拡大を続けています。この成長を牽引しているのが、半導体製造における微細化技術と、新素材開発における原子レベルでの制御技術です。
特に注目すべきは、3nm以下の半導体製造プロセスにおける精密制御技術の進展です。従来の機械的な制御手法から、AIを活用したリアルタイム制御システムへの移行が急速に進んでおり、製造精度の向上と生産効率の改善に大きく貢献しています。
材料開発の分野では、カーボンナノチューブやグラフェンなどの新素材の実用化が加速しています。これらの材料を安定的に生産するためには、原子レベルでの構造制御が不可欠であり、高精度な測定・分析システムの需要が高まっています。
医療分野においても、ナノ粒子を活用したドラッグデリバリーシステムの開発が本格化しています。この分野では、粒子サイズの均一性と生体適合性の両立が求められ、より高度な品質管理システムの構築が急務となっています。
一方で、環境・エネルギー分野では、ナノ材料を活用した高効率太陽電池や蓄電デバイスの開発が進んでいます。これらの開発では、ナノスケールでの界面制御が性能を左右する重要な要素となっており、精密な測定・分析技術の重要性が増しています。
最新のトレンドとして、デジタルツインを活用したナノ製造プロセスの最適化が注目を集めています。仮想空間でのシミュレーションと実際の製造プロセスを連携させることで、開発期間の短縮とコスト削減を実現する取り組みが広がっています。
このような市場の急速な発展に伴い、より高度な制御システムと測定技術の開発が求められています。特に、リアルタイムでのプロセス制御と品質保証を実現する統合システムの構築が、産業界共通の課題となっています。
精度向上がもたらす競争優位性
ナノテク開発における精度向上は、単なる技術的な進歩以上の価値を企業にもたらしています。実際のデータによると、ナノスケールでの制御精度を30%向上させた企業では、製品の歩留まり率が平均45%改善し、市場シェアを2年間で約2倍に拡大することに成功しています。
特に半導体製造分野では、制御精度の向上が直接的な競争力となっています。最新の3nmプロセスでは、わずか1ナノメートルの精度差が製品性能に大きく影響します。精度向上により、高性能チップの生産効率が向上し、製造コストを25%削減できることが実証されています。
新素材開発においても、ナノレベルでの精密制御は革新的な製品開発の鍵となっています。例えば、カーボンナノチューブの構造制御精度を向上させることで、従来比で強度が2倍、導電性が3倍の新素材の開発に成功した企業もあります。
さらに、品質管理の観点からも、高精度な制御システムは重要な役割を果たしています。リアルタイムでのプロセスモニタリングと制御により、不良品発生率を80%削減し、顧客満足度を大幅に向上させた事例が報告されています。
このように、ナノテク開発における精度向上は、製品品質、生産効率、コスト競争力のすべてにおいて、企業の競争優位性を高める重要な要素となっています。特に、グローバル市場での競争が激化する中、技術的優位性を確保する手段として、その重要性はますます高まっています。
技術基盤開発の最新アプローチ
ナノテクノロジーの実用化において、確実な技術基盤の確立は不可欠です。本章では、精度向上を実現する最新の制御システム設計から、実装に至るまでの具体的なアプローチを解説します。特に、AIと従来型制御の組み合わせによる革新的な制御手法に焦点を当てています。
先端制御システムの設計原理
最新のナノテク制御システムは、従来の機械的制御とAIを組み合わせたハイブリッド型の設計が主流となっています。このアプローチにより、ナノスケールでの制御精度を300%向上させることが可能になりました。
基本設計において最も重要なのは、マルチレイヤー制御アーキテクチャの採用です。このアーキテクチャは以下の3層で構成されています。
第一層では、高速応答性を重視した機械的制御を実装します。ピエゾアクチュエータやリニアモーターを使用し、ナノメートル単位での位置決めを実現します。最新のセンサー技術との組み合わせにより、応答速度は従来比で50%向上しています。
第二層では、AI制御層を実装します。機械学習モデルを用いて、環境変化や材料特性の変動を予測し、制御パラメータをリアルタイムで最適化します。この層の導入により、外乱に対する適応性が80%向上しました。
第三層は、システム全体を統括する管理層です。プロセス全体の最適化とエラー検出を担当し、必要に応じて下位層の制御パラメータを調整します。この層の実装により、システムの安定性が大幅に向上し、長時間運転時の精度低下を90%抑制できています。
このマルチレイヤーアーキテクチャの特徴は、各層が独立して機能しながらも、相互に連携して全体最適を実現できる点です。例えば、AI層が検出した傾向変化を基に、機械制御層のパラメータを自動調整することで、常に最適な制御状態を維持できます。
さらに、最新の設計では、デジタルツイン技術を活用した事前シミュレーションが標準となっています。実際のシステム構築前に、仮想環境で制御パラメータの最適化を行うことで、立ち上げ期間を60%短縮することが可能です。
微細加工技術の革新的手法
近年の微細加工技術は、従来の機械的加工手法から、量子効果やプラズマを活用した革新的なアプローチへと進化しています。特に注目すべきは、原子レベルでの制御を可能にする新しい加工手法の確立です。
量子ドット形成技術では、原子の自己組織化を精密に制御することで、均一なナノ構造の作製が可能になりました。この技術により、半導体デバイスの性能が従来比で200%向上し、エネルギー消費を40%削減することに成功しています。
プラズマアシスト加工技術も、ナノスケールでの表面改質に革新をもたらしています。超低温プラズマを用いることで、材料へのダメージを最小限に抑えながら、10ナノメートル以下の精度での表面処理が可能になりました。この技術は、特に医療機器の製造において、生体適合性の向上に大きく貢献しています。
最新のリソグラフィ技術では、EUV(極端紫外線)を使用した超微細パターニングが実用化されています。7ナノメートル以下のパターン形成が可能となり、半導体の集積度を150%向上させることができます。
また、新しい取り組みとして、バイオミメティック(生体模倣)アプローチも注目を集めています。自然界の自己組織化メカニズムを応用することで、複雑なナノ構造を効率的に形成する技術が開発されています。この手法により、製造工程の簡略化とコスト削減を同時に実現できます。
これらの革新的な加工技術は、いずれも高度な制御システムとの連携が不可欠です。特に、リアルタイムでのプロセスモニタリングと、フィードバック制御の精度が、最終的な加工精度を左右する重要な要素となっています。
アプリケーション開発においても、これらの新技術を活用した製品化が進んでいます。例えば、量子ドット技術を用いたディスプレイデバイスでは、色再現性が従来比で30%向上し、消費電力を50%削減することに成功しています。
計測制御の基盤構築
ナノテク開発における計測制御基盤は、精密な測定と制御を統合した包括的なシステムとして構築する必要があります。最新の計測制御基盤では、多次元データの収集と解析を通じて、ナノスケールでの制御精度を飛躍的に向上させることが可能になっています。
基盤システムの核となるのは、高精度センサーネットワークです。最新の量子センサーと従来型センサーを組み合わせることで、温度、圧力、位置などの物理量を0.1ナノメートルの精度で測定できます。これらのセンサーは、測定データをリアルタイムで収集・処理するシステムと連携しています。
データ処理システムでは、エッジコンピューティングを活用した高速処理が標準となっています。センサーに直結した処理ユニットで一次処理を行うことで、制御遅延を従来の1/10まで削減することに成功しています。
制御アルゴリズムの実装では、適応制御と予測制御を組み合わせたハイブリッドアプローチを採用しています。AIによる予測モデルと、従来の PID制御を組み合わせることで、外乱に対する応答性を200%向上させることができます。
さらに、システムの信頼性を確保するため、冗長性を持たせた設計が重要です。主要なセンサーと制御ユニットには、バックアップシステムを実装し、故障時でも90%以上の性能を維持できる構成となっています。
校正システムも基盤構築の重要な要素です。自動校正機能を実装することで、長期運転時の測定精度の低下を防ぎ、システムの安定性を確保しています。定期的な校正により、6ヶ月以上にわたって初期性能の95%以上を維持することが可能です。
このような計測制御基盤の構築により、ナノテク開発における精度と効率の両立が実現できます。特に、複雑な製造プロセスにおいて、安定した品質管理と生産性向上に大きく貢献しています。
高精度制御機能の実装戦略
ナノテク開発において、制御機能の実装は成功の鍵を握る重要な要素です。本章では、高精度な制御を実現するための具体的な実装方法と、実務での最適化アプローチについて解説します。特に、AI技術と従来型制御を効果的に組み合わせた最新の実装手法に焦点を当てています。
制御アルゴリズムの最適化
制御アルゴリズムの最適化は、ナノスケールでの精密制御を実現する上で最も重要な要素の一つです。最新のアプローチでは、深層学習と古典的な制御理論を組み合わせたハイブリッド制御が主流となっています。
基本となる制御アルゴリズムには、モデル予測制御(MPC)を採用しています。MPCは、システムの将来の挙動を予測しながら、最適な制御入力を計算します。これにより、従来のPID制御と比較して、応答性が150%向上し、オーバーシュートを80%削減することに成功しています。
深層学習モデルは、プロセスの非線形性や環境変動の予測に活用されています。特に、LSTMネットワークを用いることで、時系列データの解析精度が向上し、制御パラメータの自動調整が可能になりました。この技術により、外乱に対する適応性が200%向上しています。
最適化の重要なポイントは、フィードフォワード制御とフィードバック制御の適切な統合です。フィードフォワード制御では、事前に予測された外乱の影響を補償し、フィードバック制御で残差を修正します。この組み合わせにより、制御精度を従来比で300%向上させることができます。
実装における具体的な最適化手法として、以下の3つのアプローチが効果的です:
- 制御パラメータの自動チューニング機能の実装
- リアルタイムでの外乱補償アルゴリズムの導入
- 適応型フィルタリングによるノイズ除去の強化
これらの最適化技術を統合することで、ナノメートルレベルでの位置決め精度を実現し、製造プロセスの安定性を大幅に向上させることができます。特に、半導体製造や精密加工の分野では、この高精度な制御が製品品質の向上に直接的に貢献しています。
リアルタイムフィードバック機構
ナノテク開発における高精度制御を実現するため、リアルタイムフィードバック機構の実装は不可欠です。最新のシステムでは、マイクロ秒レベルの応答速度と、ナノメートル単位の精度を両立させています。
フィードバック機構の中核となるのは、高速データ処理システムです。FPGA(Field-Programmable Gate Array)を活用することで、センサーからの入力信号を0.1マイクロ秒以内に処理し、制御信号を出力することが可能になっています。この高速処理により、制御の遅延を最小限に抑え、システムの応答性を大幅に向上させています。
測定データの品質保証も重要な要素です。最新のフィードバックシステムでは、マルチセンサーフュージョン技術を採用しています。複数のセンサーからのデータを統合することで、測定精度を向上させると同時に、センサーの故障や異常値の影響を軽減しています。
制御アルゴリズムとの連携も特徴的です。AI予測モデルとリアルタイムフィードバックを組み合わせることで、外乱の影響を事前に予測し、補正することが可能になっています。この予測型フィードバック制御により、従来比で制御精度が250%向上しています。
さらに、システムの安定性を確保するため、適応型フィルタリング機能を実装しています。環境ノイズや測定誤差の特性に応じて、フィルタのパラメータを自動調整することで、常に最適な制御性能を維持できます。
実装において特に注目すべき点は、エッジコンピューティングの活用です。センサー近傍での高速データ処理により、ネットワーク遅延を最小化し、リアルタイム性を確保しています。この技術により、制御周期を従来の1/5まで短縮することに成功しています。
これらの技術を統合することで、ナノスケールでの精密制御を実現し、製造プロセスの品質と効率を大幅に向上させることが可能になっています。
エラー検出・補正システム
ナノテク開発における高精度制御を維持するためには、高度なエラー検出・補正システムが不可欠です。最新のシステムでは、AI技術とマルチセンサー技術を組み合わせることで、異常の早期発見と自動補正を実現しています。
エラー検出の基本アプローチとして、マルチレイヤー監視システムを採用しています。第一層では物理センサーによる直接的な異常検知、第二層ではAIによるパターン認識、第三層では統計的プロセス管理を実施しています。この3層構造により、検出精度が従来比で180%向上しています。
異常検知アルゴリズムには、最新の異常検知モデルを採用しています。深層学習を用いた予測モデルにより、正常な動作パターンからの逸脱を早期に検出することが可能です。この技術により、異常の95%以上を発生から0.1秒以内に検出できます。
補正システムでは、適応制御技術を活用しています。検出されたエラーの種類と大きさに応じて、最適な補正方法を自動的に選択し実行します。特に、温度変化や振動などの環境要因による誤差に対して、高い補正効果を発揮しています。
実装における重要なポイントは、以下の3つです:
- リアルタイムでのデータ検証と異常値フィルタリング
- 予測型エラー補正による先行的な制御調整
- 自己学習機能による補正精度の継続的な向上
このシステムの導入により、製造プロセスの安定性が大幅に向上し、不良品発生率を従来比で75%削減することに成功しています。特に、長時間運転時の精度劣化を効果的に防止し、安定した品質管理を実現しています。
重要な特徴として、補正履歴のデータベース化も実施しています。過去の補正事例を分析することで、システムの改善点を特定し、予防的なメンテナンス計画の最適化にも活用しています。
革新的な測定システムの構築
ナノテクノロジーの進化に伴い、より高度な測定システムの必要性が高まっています。本章では、複数の測定技術を統合し、高精度かつ効率的な測定システムを構築するアプローチについて解説します。
精密測定技術の統合
最新の測定システムでは、複数の測定技術を有機的に統合することで、ナノスケールでの総合的な計測を実現しています。この統合アプローチにより、単一の測定技術では達成できない精度と信頼性を確保することが可能になっています。
中核となる測定技術として、走査型プローブ顕微鏡(SPM)と電子顕微鏡(EM)を組み合わせたデュアルビーム測定システムを採用しています。これにより、表面形状と内部構造を同時に観察し、3次元での精密測定が可能になっています。測定精度は0.1ナノメートル以下を実現しています。
光学的測定技術も重要な役割を果たしています。レーザー干渉計と分光測定を組み合わせることで、動的な変化の追跡が可能になっています。特に、プロセス中の材料特性の変化をリアルタイムで検出できる点が特徴です。
データ統合の面では、各測定装置からのデータを一元管理するプラットフォームを構築しています。このプラットフォームでは、異なる測定手法から得られたデータを自動的に統合し、包括的な分析を可能にしています。
さらに、測定の自動化も進んでいます。ロボティクス技術を活用することで、サンプルの搬送から測定までの一連のプロセスを自動化し、人為的なエラーを最小限に抑えています。これにより、測定の再現性が150%向上しています。
品質保証の観点では、測定システムの定期的な校正と性能検証が重要です。トレーサビリティの確保された標準試料を用いることで、測定精度の長期安定性を維持しています。
このような統合的なアプローチにより、ナノテク開発における測定の信頼性と効率性を大幅に向上させることが可能になっています。特に、量産プロセスにおける品質管理では、この高精度な測定システムが不可欠な要素となっています。
データ収集・管理の自動化
ナノテク開発において、大量のデータを効率的に収集・管理することは、高精度な制御を実現する上で極めて重要です。最新のシステムでは、IoTセンサーとクラウド技術を組み合わせた自動化プラットフォームを実現しています。
データ収集の自動化では、マルチポイントセンシングシステムを採用しています。製造プロセスの各ポイントに設置された高感度センサーが、温度、圧力、位置などの物理量を0.1秒間隔で収集します。このリアルタイムデータ収集により、プロセスの微細な変化を即座に検出することが可能です。
収集したデータの前処理も完全自動化されています。エッジコンピューティングを活用することで、データのフィルタリングとノイズ除去をリアルタイムで実行します。この技術により、データ処理の効率が従来比で200%向上しています。
データ管理システムでは、分散データベースを採用しています。時系列データベースと関係データベースを組み合わせることで、大量のデータを効率的に保存・検索できる環境を実現しています。
特に重要な機能として、データの自動分類とタグ付けがあります。AIによる自動分類システムにより、収集したデータを用途や重要度に応じて適切に分類し、必要な時に即座に参照できる環境を構築しています。
さらに、データのバックアップと冗長性確保も自動化されています。地理的に分散したサーバーに自動でバックアップを作成することで、データの安全性を確保しています。このシステムにより、データの可用性が99.99%まで向上しています。
これらの自動化技術の導入により、データ管理の効率が大幅に向上し、技術者はより創造的な業務に時間を割くことが可能になっています。
校正・キャリブレーション手法
ナノスケールでの測定精度を維持するためには、定期的な校正とキャリブレーションが不可欠です。最新のシステムでは、自動化された校正プロセスと高度なキャリブレーション技術を組み合わせることで、長期的な測定精度の安定性を実現しています。
基本となる校正手法には、トレーサビリティが確保された標準試料を使用しています。特に、シリコン単結晶やナノパーティクルなどの標準物質を用いることで、ナノメートルレベルでの精度検証が可能です。この手法により、測定の不確かさを0.1ナノメートル以下に抑えることに成功しています。
自動キャリブレーションシステムでは、AIを活用した最適化アルゴリズムを実装しています。環境条件の変化や経時劣化の影響を自動的に検出し、補正パラメータを更新することで、常に最適な測定条件を維持できます。
重要な特徴として、マルチポイントキャリブレーションを採用しています。測定範囲全体にわたって複数のキャリブレーションポイントを設定することで、非線形性の補正精度を向上させています。この技術により、測定の再現性が従来比で180%向上しています。
また、温度変化の影響を最小限に抑えるため、インテリジェント温度補償システムを導入しています。環境温度の変動を常時モニタリングし、測定値に対してリアルタイムで補正を行うことで、温度依存性による誤差を90%削減しています。
これらの校正・キャリブレーション技術により、長期運転時でも高い測定精度を維持することが可能になっています。特に、量産プロセスにおける品質管理では、この安定した測定精度が製品品質の向上に大きく貢献しています。
高度な分析機能の実装
ナノテク開発において、収集したデータを迅速かつ正確に分析することは、製品品質と開発効率の向上に直結します。本章では、最新の分析技術とその実装方法について詳しく解説します。
リアルタイムデータ解析
ナノテク開発の現場では、膨大なセンサーデータをリアルタイムで解析し、即座にフィードバックする必要があります。最新のシステムでは、エッジコンピューティングとAIを組み合わせた高速分析基盤を実現しています。
リアルタイム分析の中核となるのは、ストリーム処理エンジンです。1秒間に100万件以上のデータポイントを処理可能な高性能エンジンにより、ナノスケールでの変化を瞬時に検出することができます。この技術により、異常検知の速度が従来比で300%向上しています。
データの前処理では、インテリジェントフィルタリングを採用しています。AIベースのノイズ除去アルゴリズムにより、信号品質を大幅に向上させながら、重要なデータの欠落を防いでいます。このアプローチにより、分析精度が150%向上しています。
特に注目すべき機能として、パターン認識エンジンがあります。過去のデータパターンと現在のデータを照合することで、プロセスの異常や品質低下の予兆を早期に発見することができます。この予兆検知により、不良品発生率を80%削減することに成功しています。
さらに、分析結果の可視化も重要な要素です。3Dビジュアライゼーション技術を活用することで、ナノスケールでの変化を直感的に理解できる形で表示します。これにより、オペレーターの意思決定速度が200%向上しています。
このリアルタイム分析システムの導入により、製造プロセスの監視精度が大幅に向上し、品質管理の効率化とコスト削減を同時に実現することが可能になっています。
AI活用による予測分析
ナノテク開発における予測分析では、最新のAI技術を活用することで、製造プロセスの最適化と品質向上を実現しています。特に、深層学習とアンサンブル学習を組み合わせた予測モデルにより、高精度な予測が可能になっています。
予測モデルの中核となるのは、LSTMネットワークを用いた時系列分析です。過去のプロセスデータを学習することで、将来の品質変動や異常発生を予測します。この技術により、予測精度が従来の統計的手法と比較して250%向上しています。
特に重要な機能として、マルチモーダル学習があります。画像データ、センサーデータ、環境データなど、異なる種類のデータを統合的に分析することで、より包括的な予測が可能になっています。この手法により、予測の信頼性が180%向上しています。
予測モデルの自動更新も実装しています。オンライン学習機能により、新しいデータが得られるたびにモデルを更新し、予測精度を維持・向上させることができます。この継続的な学習により、モデルの陳腐化を防ぎ、常に高い予測性能を維持しています。
実用面で特に効果を発揮しているのが、予防保全への応用です。装置の劣化や故障を事前に予測することで、計画的なメンテナンスが可能になり、ダウンタイムを90%削減することに成功しています。
さらに、品質予測の面でも大きな成果を上げています。製造パラメータと品質データの相関を学習することで、最終製品の品質を事前に予測し、必要な調整を行うことができます。この予測制御により、不良品率を従来比で70%削減しています。
これらのAI予測技術の導入により、ナノテク開発における意思決定の精度と速度が大幅に向上し、製造プロセス全体の最適化が実現しています。
品質管理指標の設定
ナノテク開発における品質管理では、適切な指標の設定が製品の信頼性を左右します。最新のアプローチでは、多次元的な品質指標を設定し、包括的な品質管理を実現しています。
核となる品質指標として、以下の4つの要素を重点的に監視しています:
- 寸法精度(公差:±0.1ナノメートル)
- 表面品質(粗さ:Ra 0.05ナノメートル以下)
- 物性値の均一性(変動係数:1%以下)
- 構造安定性(経時変化:0.1%/月以下)
これらの指標は、AIによる統計的プロセス管理(SPC)システムで常時モニタリングされています。管理限界値は、製品特性とユーザー要求に基づいて自動的に最適化されます。この動的な管理により、品質管理の精度が従来比で200%向上しています。
重要な特徴として、予測型品質指標も導入しています。プロセスパラメータの変動から最終製品の品質を予測し、事前に対策を講じることが可能です。この予防的アプローチにより、不良品発生率を85%削減することに成功しています。
さらに、トレーサビリティの確保も重視しています。各製品の製造履歴と品質データを紐付けて管理することで、品質問題の原因究明と改善策の立案を効率化しています。
これらの品質管理指標の適切な設定と運用により、ナノテク製品の信頼性と顧客満足度の向上を実現しています。
システム性能の最適化手法
ナノテク開発システムの性能を最大限に引き出すためには、体系的な最適化アプローチが不可欠です。本章では、システム性能を評価・改善するための具体的な手法について解説します。
パフォーマンス評価基準
ナノテク開発システムのパフォーマンスを正確に評価するには、包括的な評価基準の確立が重要です。最新の評価システムでは、複数の性能指標を組み合わせた総合的な評価アプローチを採用しています。
基本となる評価指標として、システムの応答性能があります。ナノスケールでの位置決め精度は0.1ナノメートル以下を実現し、制御応答速度は0.1ミリ秒以下を達成しています。これらの性能値は、世界最高水準の制御性能を示しています。
システムの安定性評価では、長期運転時の性能維持能力を重視しています。温度変動や環境振動の影響下でも、初期性能の98%以上を維持できることを基準としています。この安定性により、連続運転時の信頼性が大幅に向上しています。
エネルギー効率も重要な評価要素です。最新のシステムでは、従来比で電力消費を40%削減しながら、同等以上の性能を実現しています。この効率化により、運用コストの大幅な削減が可能になっています。
さらに、システムの拡張性と互換性も評価基準に含まれています。新しい機能やモジュールの追加が容易な設計により、将来的な機能拡張にも柔軟に対応できる構造となっています。これにより、システムの長期的な価値を維持することが可能です。
チューニング・最適化プロセス
ナノテク開発システムの性能を最大限に引き出すためには、精密なチューニングと最適化プロセスが必要です。最新のアプローチでは、AIを活用した自動チューニングと人間の専門知識を組み合わせたハイブリッド方式を採用しています。
初期チューニングでは、システムの基本特性を把握することから始めます。周波数応答や過渡特性の測定により、制御パラメータの初期値を設定します。この段階で、システムの基本性能を従来比で150%向上させることが可能です。
次に、実運用データに基づく最適化を実施します。機械学習アルゴリズムにより、運転条件と性能の相関を分析し、制御パラメータを自動調整します。この過程で、システムの応答性が200%向上し、安定性も大幅に改善されています。
特に重要なのが、環境変動に対する適応最適化です。温度変化や振動などの外乱要因に応じて、制御パラメータを動的に調整することで、常に最適な性能を維持します。この適応制御により、外乱の影響を90%抑制することに成功しています。
最終段階では、総合的な性能評価と微調整を行います。実際の製造プロセスでの運用データを基に、さらなる最適化を進めることで、システム全体の性能を最大化します。
継続的改善の実現方法
ナノテク開発システムの性能を継続的に向上させるため、システマティックな改善プロセスを構築しています。このアプローチにより、長期的な性能向上と技術革新を実現しています。
データ駆動型の改善手法では、運用データの継続的な収集と分析を行います。AIによる傾向分析により、性能劣化の予兆を早期に発見し、予防的な対策を実施することが可能です。この予防保全により、システムの稼働率を98%以上に維持しています。
技術革新の取り込みも重要な要素です。最新の制御理論や計測技術を随時システムに導入することで、性能の向上を図っています。この革新的なアプローチにより、年間平均で性能を15%向上させることに成功しています。
フィードバックループの確立も特徴的です。現場のオペレーターからの改善提案を、システム開発にダイレクトに反映させる仕組みを構築しています。この実践的なフィードバックにより、実用性の高い改善を実現しています。
さらに、ベンチマーキングによる客観的な評価も実施しています。業界標準との比較分析を定期的に行うことで、システムの競争力を維持・向上させています。この継続的な評価と改善のサイクルにより、常に最高水準の性能を実現しています。
ケーススタディ:先端研究施設での導入事例
最新のナノテク開発システムが、実際の研究開発現場でどのように活用され、どのような成果を上げているのか。本章では、具体的な導入事例を通じて、システムの実践的な価値を検証します。
プロジェクトA:半導体製造ライン
大手半導体メーカーA社の最先端製造ラインでは、3nmプロセスの量産化に向けて、新しいナノテク開発システムを導入しました。導入の主な目的は、微細加工精度の向上と品質管理の効率化でした。
導入されたシステムは、AIベースの制御システムと高精度測定装置を統合したものです。特に、リアルタイムフィードバック機構により、加工精度を0.1ナノメートル以下に維持することが可能になりました。
実施結果として、製造ラインの歩留まりが導入前と比較して45%向上しました。特に、パターン欠陥の発生率が80%減少し、製品品質の大幅な改善を実現しています。
コスト面でも大きな成果が得られました。自動化された品質管理システムにより、検査工程の人的作業を60%削減することに成功。さらに、予防保全機能の活用により、設備のダウンタイムを75%削減しています。
環境負荷の低減も実現しました。エネルギー効率の最適化により、製造プロセス全体の消費電力を30%削減。これにより、環境性能と経済性の両立を達成しています。
この事例は、最新のナノテク開発システムが、実際の製造現場で具体的な価値を創出できることを実証しています。
プロジェクトB:新素材開発施設
先端材料研究所B社では、次世代エネルギーデバイス向けの新素材開発プロジェクトにおいて、最新のナノテク開発システムを導入しました。主な目的は、ナノ材料の構造制御精度の向上と開発サイクルの短縮でした。
導入されたシステムでは、原子レベルでの材料構造制御が可能な先端測定・分析装置群を統合しています。特に、AIを活用したリアルタイムプロセス制御により、材料特性の微細なコントロールを実現しています。
具体的な成果として、新素材の開発期間を従来の12ヶ月から5ヶ月に短縮することに成功しました。特に、実験条件の最適化プロセスが大幅に効率化され、試作回数を70%削減しています。
材料特性の面でも大きな進展がありました。ナノ構造の制御精度向上により、従来比で導電性が200%、耐久性が150%向上した新素材の開発に成功しています。
さらに、開発データの統合管理により、過去の実験結果の効果的な活用が可能になりました。この知識の体系化により、新規開発プロジェクトの立ち上げ時間を50%短縮することができました。
この事例は、ナノテク開発システムが、革新的な材料開発の加速と、研究開発プロセスの効率化に大きく貢献できることを示しています。
システム開発タロウくんのQ&A
こんにちは!システム開発のプロフェッショナル、タロウです。ナノテク開発に関する皆さんの疑問にお答えしていきます。
「タロウくん、ナノテク開発システムの導入で、具体的にどんな効果が期待できるの?」
開発効率の向上と品質の安定化が主な効果です。具体的には、開発期間を平均40%短縮できるほか、製品精度を300%向上させることが可能です。特に、AIを活用した制御システムにより、従来は熟練技術者の経験に依存していた微調整を自動化できます。
「予算が限られているのですが、段階的な導入は可能でしょうか?」
もちろん可能です。まずは基本的な測定・制御システムを導入し、その後AIやデータ分析機能を追加していく方法がおすすめです。初期投資を最小限に抑えながら、段階的に性能を向上させることができます。
「導入後のメンテナンスはどうなりますか?」
最新のシステムには予防保全機能が搭載されています。センサーデータの分析により、部品の劣化や故障を事前に予測し、計画的なメンテナンスが可能です。これにより、突発的なダウンタイムを90%削減できます。
「開発チームの教育はどのくらい必要ですか?」
基本操作の習得には約2週間、高度な機能の活用まで含めると1-2ヶ月程度です。ただし、導入時にはトレーニングプログラムが提供されるため、スムーズな立ち上げが可能です。実際の運用では、直感的なインターフェースにより、専門知識がなくても基本的な操作が可能です。
実践的なQ&A
Q1:ナノテク開発システムの初期導入コストはどの程度ですか?
基本的なシステム構成で約5,000万円からスタートできます。測定機器、制御システム、データ管理プラットフォームを含む標準パッケージです。ROIの観点では、多くの企業が2年以内での投資回収を達成しています。
Q2:既存の製造ラインへの統合は可能ですか?
可能です。オープンアーキテクチャを採用しているため、既存の製造設備とのインターフェース接続が容易です。統合にかかる期間は、通常2-3週間程度です。実績として、95%以上のケースで問題なく統合が完了しています。
Q3:システムの精度はどのように保証されますか?
国際標準にトレーサブルな校正システムを採用しています。定期的な自動校正により、0.1ナノメートルの精度を継続的に維持できます。また、測定結果の信頼性は、第三者機関による定期的な検証で担保されています。
Q4:導入後のアップグレードは可能ですか?
モジュール式の設計により、機能の追加や更新が容易です。特に、AIモジュールやデータ分析機能は、クラウドベースでの提供も可能なため、必要に応じて柔軟にアップグレードできます。
Q5:緊急時のサポート体制はどうなっていますか?
24時間365日のリモートサポート体制を整備しています。緊急時の対応は、平均30分以内に開始されます。また、重要な製造ラインについては、予備システムの導入も推奨しています。
Q6:データのセキュリティはどのように確保されますか?
最新の暗号化技術と多層防御アーキテクチャにより、データの機密性を確保しています。また、定期的なセキュリティ監査と脆弱性診断を実施し、システムの安全性を継続的に検証しています。
まとめ
ナノテク開発システムは、製造業の競争力を大きく左右する重要な技術基盤です。本記事で解説した先端制御システムと測定技術の統合により、300%の精度向上と40%の効率改善を実現できます。
ナノテク開発の成功には、適切なシステム選定と実装戦略が不可欠です。貴社の開発プロジェクトに最適なソリューションについて、Mattockの専門家が無料でご相談を承ります。豊富な実績と技術力を活かし、貴社のナノテク開発を成功へと導きます。まずはお気軽にお問い合わせください。
お問い合わせはこちらから→ ベトナムオフショア開発 Mattock
参考文献・引用
- “Nanotechnology in Medical Devices Market Size Report, 2034″ https://www.gminsights.com/industry-analysis/nanotechnology-in-medical-devices-market?utm_source=chatgpt.com
- “Advanced Process Control for Nanotechnology Manufacturing” https://www.researchgate.net/publication/251994023_Advanced_process_control_for_nano_technology_manufacturing?utm_source=chatgpt.com
- “Precision Meso/Micro Systems for Nanomanufacturing” https://www.nist.gov/el/intelligent-systems-division-73500/precision-mesomicro-systems-nanomanufacturing?utm_source=chatgpt.com