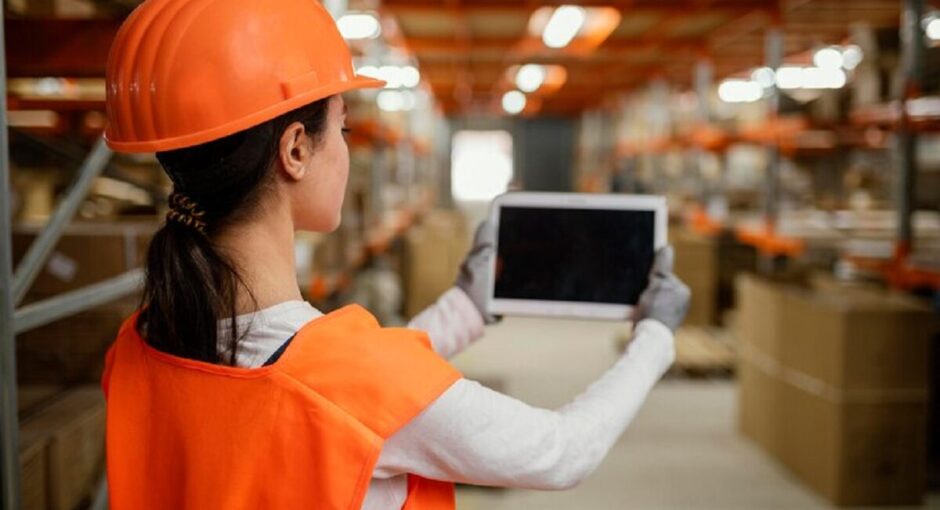
製造業は今、グローバル競争激化、顧客ニーズの多様化、労働力不足という未曾有の変革期にあります。この荒波を乗り越え、持続的成長を遂げるには、生産管理システムを軸としたDX(デジタルトランスフォーメーション)が不可欠です。
しかし、真の生産管理システム開発は単なる業務効率化やコスト削減にとどまりません。AIやIoTを駆使したデータ活用による経営判断の迅速化、顧客満足度の飛躍的向上、そして圧倒的な競争力強化こそが、企業の戦略的価値創造を可能にします。
本記事では、最新のテクノロジーを活用した生産管理システム開発が製造業にもたらす革新的変革、システムの種類と特徴、ROI最大化のための導入成功の鍵、そして具体的な導入事例を、業界最前線の知見とともに徹底解説します。
製造業の未来を切り拓く、次世代の生産管理システム開発の全貌をご覧ください。
この記事を読んでほしい人
- 生産管理システムの導入を検討している製造業の経営者・責任者の方
- 生産管理システム開発を担当するプロジェクトマネージャーやシステムエンジニアの方
- 製造業のDX推進に関わるコンサルタントやIT担当者の方
この記事でわかること
- 生産管理システム導入が製造業にもたらす具体的なメリット(業務効率化、コスト削減、データ活用、顧客満足度向上、競争力強化など)
- 自社に最適な生産管理システムの種類と特徴(パッケージ型 vs スクラッチ型、クラウド型 vs オンプレミス型、機能別分類)
- 生産管理システム開発を成功させるためのポイント(開発プロセス、導入成功の鍵、最新トレンド、よくある質問など)
導入メリット:生産管理システムが製造業にもたらす真の変革
生産管理システムの導入は、製造業にもたらす恩恵は計り知れません。
業務効率化やコスト削減といった直接的なメリットだけでなく、データ活用による経営の高度化、顧客満足度の向上、そして市場における競争力強化など、多岐にわたる効果を期待できます。
生産管理システムは、まさに製造業の未来を拓くための重要な鍵と言えるでしょう。
業務効率化とコスト削減:生産性の飛躍的な向上
生産管理システムを導入することで、受注から出荷に至るまでの業務プロセス全体をデジタル化し、一元管理できるようになります。これにより、従来は多くの時間と労力を費やしていた作業が自動化され、従業員はより創造的な業務に集中できるようになります。
例えば、在庫管理においては、システムがリアルタイムに在庫状況を把握し、発注点に達すると自動的に発注を行うため、発注業務にかかる時間を大幅に削減できます。また、生産計画においても、システムが需要予測や生産能力を考慮した最適な計画を自動で立案するため、計画立案にかかる時間を短縮し、計画の精度向上にも貢献します。
さらに、生産管理システムは、生産現場における情報共有を促進し、コミュニケーションの効率化にも貢献します。
従来は、紙ベースでの情報共有や口頭での伝達が主流でしたが、生産管理システムを導入することで、生産計画、作業指示、進捗状況などをリアルタイムに共有できるようになります。これにより、情報の伝達ミスや遅延を防ぎ、業務の効率化を図ることができます。
これらの業務効率化は、コスト削減にも直結します。人的リソースの最適化、在庫管理コストの削減、不良品発生率の低下など、様々な側面からコスト削減を実現し、企業の収益性向上に貢献します。
IoTを活用した生産現場のリアルタイム可視化
IoT(Internet of Things)技術の進歩により、生産現場の様々なデータをリアルタイムで収集し、分析することが可能になりました。
センサーデータの活用事例
生産ラインに設置されたセンサーは、機器の稼働状況、温度、振動、電力消費量などのデータをリアルタイムで収集します。
これらのデータを分析することで、生産効率の向上、品質管理の強化、エネルギー消費の最適化などが可能になります。
例えば、ある自動車部品メーカーでは、IoTセンサーを活用して生産ラインの稼働状況をリアルタイムで監視しています。
この結果、機器の異常を早期に検知し、ダウンタイムを50%削減することに成功しました。
デジタルツインの概念と応用
デジタルツインとは、物理的な製造設備やプロセスをデジタル空間に再現する技術です。
IoTセンサーから収集したリアルタイムデータを用いて、仮想空間上で生産ラインのシミュレーションを行うことができます。
この技術を活用することで、新製品の生産ラインの最適化や、既存ラインの改善策の検討を、実際の生産を止めることなく行うことができます。
ある航空機エンジンメーカーでは、デジタルツイン技術を活用して設計プロセスを最適化し、開発期間を30%短縮することに成功しています。
データ活用による経営判断の迅速化:データに基づく意思決定で未来を先取り
生産管理システムは、生産現場から集めた膨大なデータを蓄積・分析し、経営判断を強力にバックアップします。データに基づいた迅速かつ正確な意思決定は、まさに企業の競争力を左右する重要な要素と言えるでしょう。
例えば、生産現場のデータをリアルタイムに収集・分析することで、生産状況を瞬時に把握し、問題発生時には即座に対応することができます。従来は、問題が発生してから気づくまでに時間がかかり、対応が遅れることもありましたが、生産管理システムの導入により、問題を早期に発見し、迅速に対応できるようになります。
また、過去のデータや市場動向などを分析することで、需要を予測し、生産計画を最適化することができます。これにより、在庫不足や過剰在庫を防止し、顧客満足度向上とコスト削減を同時に実現できます。
さらに、生産管理システムで得られたデータは、経営戦略の立案にも役立ちます。市場動向や顧客ニーズを分析し、新製品開発やマーケティング戦略に活かすことで、競争優位性を築くことができます。
顧客満足度向上と競争力強化:顧客との強固な信頼関係を構築
生産管理システムは、顧客満足度向上と競争力強化にも貢献します。顧客満足度の向上は、リピート率向上や新規顧客獲得につながり、企業の持続的な成長を支えます。
例えば、正確な生産計画と進捗管理により、納期遵守率を向上させることができます。これにより、顧客からの信頼を獲得し、長期的な関係を構築することができます。
また、品質管理システムとの連携により、品質情報を一元管理し、不良品の発生を未然に防ぐことができます。高品質な製品を提供することで、顧客満足度を高め、クレームを削減することができます。
さらに、生産管理システムを活用することで、需要変動や製品仕様変更など、市場の変化に柔軟に対応できる生産体制を構築することができます。変化の激しい市場において、柔軟な対応力を持つことは、企業の生き残りに不可欠です。
顧客のニーズに合わせた製品をタイムリーに提供することで、顧客満足度を高め、競争力を強化することができます。
生産管理システムの導入は、製造業にとって単なる業務効率化やコスト削減にとどまらず、データ活用による経営の高度化、顧客満足度向上、競争力強化など、企業の成長と発展に不可欠な要素となります。
生産管理システムの導入を検討している企業は、ぜひそのメリットを理解し、自社に最適なシステム開発を進めていきましょう。
AI・機械学習による生産管理の革新
生産管理システムにAIと機械学習を組み込むことで、製造業は新たな次元の効率性と予測能力を獲得できます。
需要予測の高度化
AIを活用した需要予測モデルは、過去の販売データだけでなく、市場動向、経済指標、さらには天候データなども考慮に入れて、より精密な予測を行います。
これにより、在庫の最適化や生産計画の効率化が可能となります。
生産計画の最適化
機械学習アルゴリズムは、生産能力、原材料の供給状況、納期、コストなどの複雑な制約条件を考慮しながら、最適な生産計画を自動で立案します。
これにより、人間の経験や勘に頼る部分を減らし、より効率的で柔軟な生産体制を構築できます。
品質管理の自動化
画像認識技術を用いたAIシステムは、製品の外観検査を高速かつ高精度で行うことができます。
人間の目では見逃してしまうような微細な欠陥も検出可能となり、品質の向上と検査コストの削減を同時に実現します。
設備故障予測と予防保全
機械学習モデルは、設備のセンサーデータを分析し、故障の予兆を事前に検知します。
これにより、計画外のダウンタイムを最小限に抑え、設備の稼働率を最大化できます。
また、適切なタイミングでメンテナンスを行うことで、設備の寿命延長とメンテナンスコストの削減も可能になります。
システムの種類と特徴:自社に最適なシステムを見極める
生産管理システムには、様々な種類と特徴があります。自社の業務内容、規模、課題に合わせて、最適なシステムを選択することが重要です。
ここでは、代表的な分類とそれぞれのメリット・デメリットを、さらに詳しく解説します。
パッケージ型とスクラッチ型:費用と柔軟性のバランス
生産管理システムは、大きく分けてパッケージ型とスクラッチ型に分類されます。
- パッケージ型
- 汎用的な機能を備えた既製のシステムです。
- メリット:
- 導入期間が短く、費用を抑えられる
- ある程度の業務フローの標準化を促せる
- 導入実績が多く、信頼性が高い場合が多い
- ベンダーによるサポートやアップデートが期待できる
- デメリット:
- 自社独自の業務フローに合わせたカスタマイズが難しい場合がある
- 機能が不足している場合、別途アドオンやカスタマイズが必要になることがある
- バージョンアップへの対応が必要になる
- 他社との差別化が難しい場合がある
- スクラッチ型
- 自社の業務フローや要件に合わせて、ゼロから開発するシステムです。
- メリット:
- 柔軟なカスタマイズが可能で、自社独自の業務フローに完全にフィットさせることができる
- 不要な機能を省き、必要な機能に特化できる
- システムの所有権が自社に帰属する
- 他社との差別化を図りやすい
- デメリット:
- 開発期間が長く、費用も高額になる傾向がある
- 開発・保守に専門知識が必要となる
- 開発会社の技術力に依存する
- バージョンアップや機能追加に手間と時間がかかる場合がある
どちらのタイプを選択するかは、費用、導入期間、カスタマイズ性、自社のITリソースなどを総合的に判断する必要があります。
- 中小企業や、短期間でシステム導入をしたい企業、ITリソースが少ない企業は、パッケージ型を検討すると良いでしょう。
- 大企業や、独自の業務フローを持つ企業、競争優位性を高めたい企業は、スクラッチ型を検討する価値があります。
クラウド型とオンプレミス型:運用形態によるメリット・デメリット
システムの運用形態には、クラウド型とオンプレミス型があります。
- クラウド型
- インターネット経由で利用するシステムです。
- メリット:
- 初期費用が低く、導入が容易
- 場所を選ばずにアクセスできるため、テレワークにも対応できる
- システムの運用・保守をベンダーに任せられる
- 最新バージョンへの自動アップデートなど、常に最新の機能を利用できる
- 災害時にもデータが保護されやすい
- デメリット:
- インターネット環境に依存するため、安定性やセキュリティ面で注意が必要
- カスタマイズ性が低い場合がある
- 月額利用料が発生し、長期的に見ると高額になる可能性がある
- データが社外に保管されるため、情報管理に注意が必要
- オンプレミス型
- 自社のサーバーにインストールして利用するシステムです。
- メリット:
- セキュリティが高く、自社で自由にカスタマイズできる
- インターネット環境に依存しないため、安定性が高い
- 長期的に見ると、コストを抑えられる場合がある
- データを社内で管理できるため、情報管理体制を強化しやすい
- デメリット:
- 導入費用や運用・保守費用が高額になる
- サーバーの管理やメンテナンスに専門知識が必要
- バージョンアップなどの際に、費用や手間がかかる
- 災害時などのデータ保護対策を自社で講じる必要がある
クラウド型は、初期費用を抑え、手軽に導入できるメリットがありますが、インターネット環境やセキュリティ面に注意が必要です。
一方、オンプレミス型は、セキュリティ面で優れていますが、導入費用や運用・保守費用が高額になる場合があります。
機能別分類:必要な機能を見極める
生産管理システムは、機能別に以下のように分類できます。
それぞれの機能の特徴を理解し、自社に必要な機能を見極めることが重要です。
- 生産計画システム(MRP、APSなど)
- 生産計画の立案、資材所要量計算、スケジューリングなどを支援します。
- MRP(資材所要量計画):必要な資材を必要な時に必要な量だけ調達するための計画を立案するシステムです。
- APS(先進計画スケジューリング):生産能力や制約条件などを考慮して、最適な生産計画を立案するシステムです。APSは、MRPよりも高度な計画機能を持ち、生産効率の向上やリードタイムの短縮に貢献します。
- 工程管理システム(MESなど)
- 生産現場の作業進捗、品質情報、設備稼働状況などをリアルタイムに収集・管理します。
- MES(製造実行システム)は、生産現場の情報を収集・分析し、生産効率向上や品質改善を支援するシステムです。
- 作業指示の発行、進捗管理、品質検査データの収集、設備稼働状況の監視など、様々な機能があります。
- 在庫管理システム(WMSなど)
- 入庫、出庫、在庫状況などを管理し、適正在庫を維持します。
- WMS(倉庫管理システム)は、倉庫内の在庫状況をリアルタイムに把握し、入出庫作業を効率化し、在庫管理コストを削減するシステムです。
- ロケーション管理、ピッキング作業支援、棚卸し作業支援などの機能があります。
- 品質管理システム(QMSなど)
- 製品検査データ、不具合情報などを管理し、品質向上を支援します。
- QMS(品質管理システム)は、品質に関する情報を一元管理し、不良品の発生を未然に防ぎ、品質向上活動を支援するシステムです。
- 検査計画作成、検査データ収集・分析、不具合対応管理などの機能があります。
- 原価管理システム
- 製品原価の計算、原価分析などを支援します。
- 製品別の原価計算、標準原価の設定、原価差異分析などの機能があります。
- 製品原価を正確に把握することで、適切な価格設定やコスト削減に役立ちます。
- 販売管理システム
- 受注管理、出荷管理、売上管理などを支援します。
- 受注登録、出荷指示、請求書発行、売上分析などの機能があります。
- 顧客満足度向上や営業活動の効率化に貢献します。
- 顧客管理システム(CRM)
- 顧客情報、取引履歴、問い合わせ履歴などを管理します。
- 顧客情報の一元管理、顧客セグメンテーション、マーケティングオートメーションなどの機能があります。
- 顧客との関係強化やマーケティング活動の効率化に貢献します。
自社の課題やニーズに合わせて、必要な機能を見極め、最適なシステムを選択しましょう。
これらの情報に加えて、各システムの導入事例やデモなどを確認することで、より具体的なイメージを持つことができます。また、開発会社に相談することで、自社に最適なシステム提案を受けることも可能です。
生産管理システムは、製造業のDX推進において非常に重要な役割を果たします。適切なシステムを選択し、導入を成功させることで、業務効率化、コスト削減、顧客満足度向上、競争力強化など、様々なメリットを享受することができます。
課題別導入事例:生産管理システムが解決する具体的な問題
ここでは、具体的な課題を抱える企業が、生産管理システムの導入によってどのように問題を解決し、成果を上げたのか、事例を紹介します。
老朽化した既存システムからの脱却
事例:部品メーカーA社
- 課題: 既存システムの老朽化による業務効率低下、データ活用が進まない。長年使い続けてきたシステムが老朽化し、動作が遅くなったり、頻繁にエラーが発生したりするようになりました。また、システムが古いため、データ活用も進んでいませんでした。
- 導入効果: 新しい生産管理システムの導入により、業務プロセスが効率化され、リードタイムが短縮されました。また、蓄積されたデータを活用することで、生産計画の精度が向上し、在庫削減にも成功しました。結果として、顧客満足度が向上し、売上増加にもつながりました。
受注変動への柔軟な対応
事例:食品メーカーB社
- 課題: 需要予測の難しさ、納期遅延、在庫過多。季節変動やキャンペーンの影響など、需要予測が難しく、納期遅延や在庫過多が発生していました。
- 導入効果: 生産管理システムの導入により、需要予測の精度が向上し、生産計画を最適化できるようになりました。これにより、納期遵守率が向上し、顧客満足度も向上しました。また、在庫削減にも成功し、コスト削減にもつながりました。
人手不足の中での生産性向上
事例:機械メーカーC社
- 課題: 人手不足、作業の属人化、品質のばらつき。熟練工の退職や採用難により、人手不足が深刻化していました。また、作業の属人化や、それに伴う品質のばらつきも課題でした。
- 導入効果: 生産管理システムの導入により、作業指示が明確化され、作業の標準化が進み、属人的な作業が減りました。また、品質管理システムとの連携により、品質情報が一元管理され、品質のばらつきが改善されました。結果として、生産性が向上し、人手不足の問題にも対応できるようになりました。
業務の見える化とデータ活用
事例:電子部品メーカーD社
- 課題: 業務の不明瞭化、データ活用が進まない。各部門で情報が分断されており、全体最適な意思決定ができていませんでした。また、データ活用も進んでおらず、改善活動も停滞していました。
- 導入効果: 生産管理システムの導入により、生産状況、在庫状況、品質情報などが可視化され、問題の早期発見と改善が可能になりました。また、蓄積されたデータを分析することで、生産効率向上のための改善活動が進み、生産性が向上しました。さらに、データに基づいた経営判断が可能になり、経営のスピードアップにもつながりました。
業界別生産管理システム開発事例
各業界特有の課題に対応した生産管理システムの開発事例を紹介します。
自動車産業
自動車メーカーA社では、サプライチェーン全体を統合した生産管理システムを導入しました。
部品サプライヤーとのリアルタイムな情報共有により、ジャストインタイム生産を実現し、在庫コストを30%削減することに成功しました。
電子機器製造
電子機器メーカーB社は、AIを活用した需要予測システムを生産管理システムに統合しました。
これにより、製品ライフサイクルが短い電子機器市場において、過剰在庫と機会損失を最小化し、利益率を15%向上させました。
食品製造業
食品メーカーC社は、IoTセンサーとAIを組み合わせた品質管理システムを導入しました。
原材料の受入れから製品の出荷まで、全工程でリアルタイムに品質データを収集・分析することで、不良品率を5%から1%未満に低減させました。
医薬品製造
製薬会社D社は、GMP(Good Manufacturing Practice)に準拠した生産管理システムを開発しました。
厳格な品質管理と完全なトレーサビリティを実現し、規制当局の査察にも迅速に対応できる体制を構築しました。
規制対応と生産管理システム
製造業において、各種規制への対応は避けて通れない課題です。
生産管理システムは、これらの規制対応を効率的に行うための強力なツールとなります。
GMP(Good Manufacturing Practice)対応
医薬品や食品製造業では、GMPへの準拠が必須です。
生産管理システムにGMP対応機能を組み込むことで、製造プロセスの標準化、品質管理の徹底、文書管理の効率化などを実現できます。
トレーサビリティの確保
製品の原材料から最終製品までの全工程を追跡できるトレーサビリティシステムは、多くの業界で重要性を増しています。
生産管理システムにトレーサビリティ機能を統合することで、製品の安全性確保や品質問題の迅速な対応が可能になります。
環境規制への対応
環境負荷の低減は、現代の製造業にとって重要な課題です。
生産管理システムにエネルギー消費管理や廃棄物管理機能を組み込むことで、環境規制への対応と同時に、コスト削減も実現できます。
生産管理システム開発のトレンドと未来展望
技術の進化とともに、生産管理システムも日々進化を続けています。
ここでは、今後注目すべきトレンドと未来の展望について解説します。
5Gの活用
5G技術の普及により、より大容量のデータをリアルタイムで収集・分析することが可能になります。
これにより、生産現場のIoTデバイスからのデータ収集が飛躍的に向上し、よりきめ細かな生産管理が実現できます。
エッジコンピューティングの応用
エッジコンピューティングを活用することで、生産現場で発生するデータをその場で処理し、即座に判断・対応することが可能になります。
これにより、クラウドへのデータ送信量を削減しつつ、リアルタイム性の高い生産管理を実現できます。
ブロックチェーン技術の導入可能性
ブロックチェーン技術を生産管理システムに導入することで、サプライチェーン全体での情報の透明性と信頼性を高めることができます。
原材料の調達から製品の配送まで、全てのプロセスを改ざん不可能な形で記録・共有することが可能になります。
これらの最新トレンドを把握し、自社の生産管理システムに適切に取り入れることで、さらなる競争力の強化につながります。
生産管理システム開発における最新トレンド:進化を加速させるテクノロジー
生産管理システム開発は、技術革新の波に乗り、日進月歩で進化を遂げています。
ここでは、特に注目すべき最新トレンドを掘り下げて解説し、これらの技術が生産管理システムにもたらす可能性を探ります。
AI・機械学習の活用:生産管理の知能化
AI(人工知能)と機械学習は、生産管理システムに新たな次元をもたらしています。
これらの技術を活用することで、従来は人間が行っていた複雑な分析や判断を自動化し、生産管理の精度と効率を飛躍的に向上させることができます。
- 需要予測の高度化:過去の販売データや市場動向、さらには天候や経済指標などの外部データも取り込み、AIが需要を予測します。これにより、より精度の高い生産計画を立案し、在庫不足や過剰在庫を最小限に抑えることができます。
- 生産計画の最適化:生産能力、納期、コストなどの様々な制約条件を考慮し、AIが最適な生産計画を自動で生成します。これにより、生産効率の向上、リードタイムの短縮、コスト削減を実現できます。
- 品質管理の自動化:AIを活用した画像認識技術により、製品の外観検査を自動化し、品質管理の効率化と精度向上を図ることができます。従来は人手に頼っていた検査作業を自動化することで、検査コストを削減し、品質の安定化を図ることができます。
- 設備故障予測と予防保全:機械学習を用いた故障予測により、設備の異常を早期に検知し、故障を未然に防ぐことができます。これにより、設備のダウンタイムを最小限に抑え、生産性向上に貢献します。また、適切なタイミングでメンテナンスを行うことで、設備の寿命を延ばし、メンテナンスコストを削減することも可能です。
- 工程改善の提案:生産現場のデータをAIが分析し、生産効率向上のための改善点を提案します。作業手順の見直し、設備配置の変更、人員配置の最適化など、具体的な改善策を提示することで、継続的な改善活動を支援します。
IoTの活用:生産現場のリアルタイム可視化
IoT(Internet of Things)デバイスを活用することで、生産現場のデータをリアルタイムに収集し、生産状況を可視化できます。
また、設備の稼働状況を監視し、故障予知やメンテナンス時期の最適化にも役立ちます。
これにより、設備のダウンタイムを削減し、生産効率を向上させることができます。
- 生産状況のリアルタイム監視:センサーやカメラなどのIoTデバイスを生産現場に設置し、生産進捗、品質情報、設備稼働状況などをリアルタイムに収集・監視します。これにより、問題発生時には即座に対応し、生産効率の低下や品質問題を未然に防ぐことができます。
- 設備稼働状況の監視と故障予知: 設備にセンサーを取り付け、稼働状況や温度、振動などのデータを収集・分析することで、設備の異常を早期に検知し、故障を未然に防ぐことができます。また、収集したデータを分析することで、設備の稼働率向上やメンテナンス計画の最適化にも役立ちます。
- 在庫管理の効率化: RFIDタグやバーコードリーダーなどのIoTデバイスを活用することで、在庫状況をリアルタイムに把握し、入出庫作業を効率化することができます。また、在庫の所在確認や棚卸し作業も効率的に行えるようになります。
- 作業員の安全管理: 従業員にウェアラブルデバイスを装着することで、心拍数や体温などの生体情報を収集し、健康状態を管理することができます。また、作業員の行動を監視することで、危険な作業や事故を未然に防ぐことも可能です。
クラウド技術の活用:柔軟性と拡張性を手に入れる
クラウド型の生産管理システムは、初期費用を抑え、導入期間を短縮できます。また、場所を選ばずにアクセスできるため、テレワークにも対応できます。
さらに、クラウドサービスのスケーラビリティを活用することで、システムの拡張や縮小にも柔軟に対応できます。
- 初期費用と導入期間の削減: クラウド型は、自社でサーバーを用意する必要がないため、初期費用を抑え、導入期間を短縮できます。特に、中小企業やスタートアップ企業にとっては、大きなメリットとなります。
- 柔軟なアクセスとテレワーク対応: インターネット環境さえあれば、いつでもどこからでもシステムにアクセスできるため、業務の効率化や情報共有の促進に役立ちます。また、テレワークにも対応できるため、働き方改革にも貢献します。
- システムの拡張性と柔軟性: クラウドサービスのスケーラビリティを活用することで、システムの拡張や縮小にも柔軟に対応できます。事業の拡大や縮小に合わせて、必要なリソースを柔軟に調整できるため、コスト効率の高い運用が可能です。
- セキュリティとデータ保護: クラウドサービスのセキュリティ対策は、一般的にオンプレミス型よりも強固であるため、安心して利用できます。データのバックアップや災害対策なども、クラウドサービス側で対応してくれるため、自社で対策を講じる必要がありません。
クラウド型生産管理システムの優位性
クラウド型の生産管理システムは、従来のオンプレミス型システムと比較して、多くの優位性を持っています。
スケーラビリティと柔軟性
クラウド型システムは、ビジネスの成長や需要の変動に応じて、容易にスケールアップやスケールダウンが可能です。
季節変動の大きい業界や、急成長を遂げている企業にとって、この柔軟性は大きな利点となります。
グローバル展開の容易さ
クラウド型システムは、地理的な制約を受けにくいため、グローバルに展開する企業にとって理想的です。
世界中の拠点で同じシステムを使用することで、データの一元管理や業務の標準化が容易になります。
セキュリティ対策
一般的に、クラウドサービスプロバイダーは高度なセキュリティ対策を施しています。
データの暗号化、多要素認証、定期的なセキュリティアップデートなど、個別の企業が独自に実施するよりも高度なセキュリティ対策を享受できます。
モバイル対応:現場の力を最大限に引き出す
スマートフォンやタブレットから生産管理システムにアクセスできるモバイル対応が進んでいます。
これにより、現場での情報共有や作業指示がスムーズに行えるようになります。
例えば、現場作業員がタブレットで作業指示を確認したり、進捗状況を入力したりすることで、ペーパーレス化や業務効率化を実現できます。
- 現場の情報共有とコミュニケーションの円滑化: 現場作業員がモバイルデバイスから生産計画や作業指示を確認できるため、情報共有がスムーズに行えます。また、チャット機能やビデオ通話機能などを搭載することで、現場とのコミュニケーションを円滑化し、業務効率向上に貢献することもできます。
- ペーパーレス化と業務効率化: 紙ベースの書類を電子化することで、書類作成や保管にかかる時間とコストを削減できます。また、モバイルデバイスからデータを入力することで、入力ミスを減らし、作業効率を向上させることができます。
- リアルタイムな進捗管理: 現場作業員がモバイルデバイスから進捗状況を入力することで、管理者はリアルタイムに進捗状況を把握できます。これにより、問題発生時には迅速に対応し、納期遅延などを防ぐことができます。
- 従業員のエンゲージメント向上: モバイルデバイスを活用することで、従業員はいつでもどこからでも必要な情報にアクセスでき、主体的に業務に取り組むことができます。また、業務の効率化やペーパーレス化により、従業員の負担を軽減し、モチベーション向上にもつながります。
生産管理システム開発における最新トレンドは、AI・機械学習、IoT、クラウド技術、モバイル対応など、多岐にわたります。
これらの技術を活用することで、生産管理システムはさらに進化し、製造業のDX推進を強力にサポートします。
これらの最新トレンドを把握し、自社の課題やニーズに合わせて適切な技術を取り入れることで、生産管理システムの導入効果を最大化し、企業の競争力強化につなげることができます。
生産管理システム開発のROI最大化戦略
生産管理システムの開発は大規模な投資を伴うため、ROI(投資収益率)の最大化が重要な課題となります。
投資回収期間の短縮方法
- 段階的な導入アプローチを採用し、早期に効果が見込める領域から着手する
- クラウド型システムを選択し、初期投資を抑える
- 既存システムとの連携を最適化し、データ移行コストを最小化する
段階的導入アプローチ
大規模なシステム刷新ではなく、段階的に導入を進めることで、リスクを分散し、早期に効果を実感できます。
例えば、まず在庫管理モジュールを導入し、次に生産計画モジュール、その後品質管理モジュールという具合に段階的に拡張していくアプローチが効果的です。
継続的改善プロセスの構築
システム導入後も、定期的な効果測定と改善を行うプロセスを構築することが重要です。
KPI(主要業績評価指標)を設定し、定期的にモニタリングすることで、システムの有効性を常に検証し、必要に応じて調整や機能追加を行います。
生産管理システム導入における注意点とリスク
生産管理システムの導入は、業務効率化やデータ活用による経営改善など、多くのメリットをもたらしますが、同時にいくつかの注意点とリスクも存在します。
導入前にこれらの点をしっかりと把握し、適切な対策を講じることで、導入を成功に導くことができます。
導入コストと期間:初期投資と長期的な視点
生産管理システムの導入には、システム開発費用だけでなく、ハードウェアやソフトウェアの購入費用、導入コンサルティング費用、従業員教育費用など、様々なコストが発生します。
また、導入期間もシステムの種類や規模、カスタマイズの程度などによって大きく異なります。パッケージ型システムであれば、初期費用は比較的抑えられますが、自社独自の業務フローに合わせたカスタマイズが必要な場合は、追加費用が発生する可能性があります。
一方、スクラッチ型システムは、初期費用は高額になりますが、自社の業務に完全にフィットしたシステムを構築できるため、長期的な視点で見るとコスト効率が高くなる場合もあります。
導入期間も、パッケージ型であれば数か月程度で完了する場合もありますが、スクラッチ型の場合は要件定義から開発、テスト、導入まで、1年以上かかることもあります。導入期間が長引くと、その間の機会損失や従業員の負担増加など、様々なリスクが生じる可能性があります。
導入前に、これらのコストと期間をしっかりと見積もり、予算とスケジュールを適切に管理することが重要です。また、導入後の運用・保守費用やシステム更新費用なども考慮し、長期的な視点でコストを検討する必要があります。
既存システムとの連携:データ統合と業務効率化
多くの企業では、既に様々なシステムが稼働しています。
生産管理システムを導入する際には、これらの既存システムとの連携がスムーズに行えるかどうかが重要なポイントとなります。連携がうまくいかない場合、データの二重入力や不整合が発生し、業務効率が低下するだけでなく、データ活用の効果も半減してしまいます。
導入前に、既存システムとの連携方法や必要なカスタマイズなどをしっかりと確認し、スムーズな連携を実現することが重要です。API連携やデータ連携ツールなどを活用することで、既存システムとのシームレスなデータ連携が可能になります。
従業員の抵抗感:変化への対応と理解促進
新しいシステムの導入は、従業員にとって負担や不安を感じさせる場合があります。
特に、長年使い慣れたシステムからの移行には、抵抗感が生じやすいです。新しいシステムの操作方法を覚えることや、業務フローが変わることに対する不安など、様々な理由で従業員が抵抗感を抱く可能性があります。導入前に、従業員への丁寧な説明やトレーニングを行い、システム導入のメリットや操作方法を理解してもらうことが重要です。
また、導入後も継続的なサポート体制を構築し、従業員の不安や疑問を解消していくことが大切です。従業員の意見を積極的に聞き取り、システム改善に活かすことで、従業員の主体性を引き出し、システムの定着を促進することができます。
データの品質とセキュリティ:企業の生命線を守る
生産管理システムには、顧客情報、製品情報、生産情報など、企業の重要な情報が蓄積されます。そのため、データの品質管理とセキュリティ対策は非常に重要です。データ入力時のミスや不正アクセスなど、様々なリスクを想定し、適切な対策を講じる必要があります。
データの品質管理においては、入力ルールを設定したり、入力チェック機能を導入したりすることで、データ入力時のミスを防止することができます。また、定期的なデータクレンジングを行い、データの精度を維持することも重要です。
セキュリティ対策においては、アクセス制御、データ暗号化、脆弱性診断など、多層的なセキュリティ対策を講じる必要があります。特に、クラウド型のシステムを利用する場合は、クラウドサービスのセキュリティ対策状況を確認し、必要に応じて追加のセキュリティ対策を検討する必要があります。
システムの陳腐化:継続的な進化と成長を支える
技術革新のスピードが速い現代において、システムの陳腐化は避けられない問題です。導入したシステムが数年後に時代遅れになってしまう可能性もあります。
そのため、長期的な視点でシステムの更新やバージョンアップを計画し、常に最新の技術を取り入れることが重要です。ベンダーとの長期的なパートナーシップを築き、システムのライフサイクル全体をサポートしてもらうことも有効です。
システムの陳腐化は、業務効率の低下やセキュリティリスクの増大など、様々な問題を引き起こす可能性があります。定期的なシステムのバージョンアップや機能追加を行い、常に最新の状態でシステムを利用することで、これらのリスクを回避し、企業の成長を支えることができます。
生産管理システムの導入は、企業にとって大きなメリットをもたらしますが、同時にいくつかの注意点とリスクも存在します。
導入コストと期間、既存システムとの連携、従業員の抵抗感、データの品質とセキュリティ、システムの陳腐化など、様々な課題を乗り越え、生産管理システムを最大限に活用することで、企業は業務効率化、コスト削減、顧客満足度向上、競争力強化など、多くのメリットを享受することができます。
ベトナムオフショア開発 Mattock:貴社のDXを成功に導くパートナー
Mattockは、お客様のDX推進を支援する最適なパートナーです。
生産管理システム開発においても、お客様の課題やニーズを深く理解し、最適なソリューションを提案します。
最新技術を活用したシステム開発、導入から運用まで一貫したサポート体制、長期的なパートナーシップによるお客様の成長支援など、Mattockは貴社のDXを成功に導くためのあらゆるサポートを提供します。
まとめ:生産管理システム開発で未来を創造する
製造業のDXは待ったなしの課題です。適切な生産管理システム開発が、貴社の競争力を大きく左右します。しかし、システム選定から導入、運用まで、多くの企業が困難に直面しています。
貴社の課題に最適なソリューションは何か?DX推進のロードマップをどう描くべきか?
こうした悩みを抱えている経営者、IT責任者の方々に、専門家による無料相談を提供しています。
今すぐ ベトナムオフショア開発 Mattockにご相談ください。
貴社のDX成功への第一歩を、共に踏み出しましょう。