製造業のデジタルトランスフォーメーション(DX)が加速する中、工程管理システムの重要性が急速に高まっています。本記事では、最新のテクノロジーを活用した工程管理システムの開発手法と、実際の導入事例から得られた知見を体系的に解説します。
特に、リアルタイムモニタリングと予測分析を活用した生産効率向上の実践的な方法論について、詳しく説明していきます。
この記事で分かること
- 工程管理システムの開発概要
- 品質・進捗・設備の統合管理システム構築における重要ポイントと実装方法
- 導入事例と開発プロセスの具体的な展開手順
この記事を読んでほしい人
- 製造業の生産管理・工程管理システム開発の責任者
- 生産性向上とDX推進を担当するプロジェクトマネージャー
- 品質管理・設備管理部門の責任者
1. 工程管理システム開発の最新トレンド
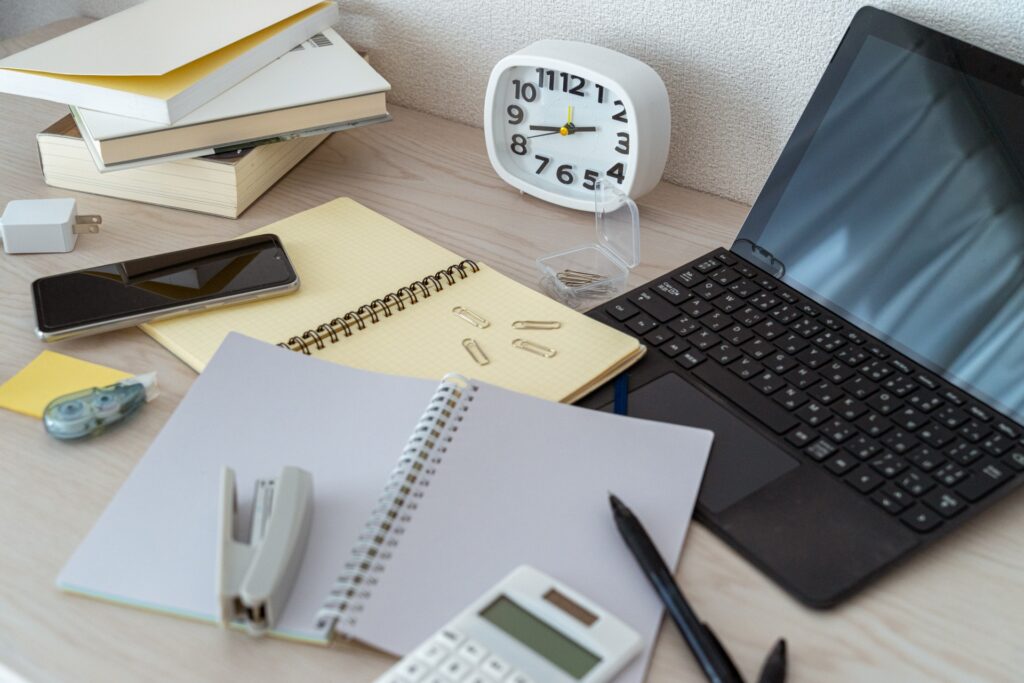
工程管理システム開発の最新トレンド
デジタルトランスフォーメーションによる製造業の革新
製造業におけるデジタルトランスフォーメーション(DX)は、従来の製造プロセスを根本から変革している。
特に工程管理システムの領域では、人工知能(AI)とモノのインターネット(IoT)を組み合わせた革新的なソリューションが台頭しており、生産性の大幅な向上を実現している。これらの技術革新により、製造現場はよりスマートで効率的な運営が可能となっている。
デジタルツイン技術の実用化と進化
デジタルツイン技術は、物理的な製造ラインの完全なデジタルコピーを作成し、リアルタイムでのシミュレーションと最適化を可能にする革新的なアプローチである。この技術の導入により、製造プロセス全体の可視化と最適化が実現され、生産効率の飛躍的な向上がもたらされている。
リアルタイムシミュレーションの実現
製造ラインのデジタルツインでは、実際の生産設備とリアルタイムに連動したシミュレーションが可能となる。
これにより、生産計画の動的な調整や、設備稼働率の最適化が実現される。さらに、様々な生産シナリオのシミュレーションを通じて、最適な生産条件の特定が可能となっている。
予知保全システムの高度化
高度なセンサー技術とAIの組み合わせにより、設備の異常を早期に検知し、予防保全を実現するシステムが確立されている。振動、温度、音響、電流値など、多様なパラメータをリアルタイムでモニタリングし、故障の予兆を高精度で検知することが可能となっている。
AIと機械学習の製造現場への本格導入
製造業におけるAIと機械学習の活用は、データ駆動型の意思決定を可能にし、生産性の大幅な向上をもたらしている。特に予測分析の分野では、従来の統計的手法では実現できなかった高度な予測が可能となっている。
需要予測システムの革新
機械学習を活用した需要予測システムでは、過去の販売データに加え、気象情報、イベント情報、SNSデータなど、多様な外部要因を考慮した予測が実現されている。これにより、予測精度が従来比で30%以上向上し、在庫の最適化や生産計画の効率化に大きく貢献している。
品質管理システムの高度化
インライン検査データのリアルタイム分析により、製品品質の変動をリアルタイムで検知し、即座に対応することが可能となっている。また、統計的プロセス管理(SPC)の自動化により、品質管理担当者の作業負荷を大幅に軽減しながら、より高精度な品質管理を実現している。
IoTプラットフォームの発展と統合
製造現場のIoT化が加速する中、様々なセンサーやデバイスから収集されるデータを統合的に管理し、活用するプラットフォームの重要性が増している。これらのプラットフォームは、製造プロセス全体の最適化を支援する中核的な役割を果たしている。
センサーネットワークの拡充
製造設備や製品に取り付けられた多様なセンサーからのデータを、リアルタイムで収集・分析するネットワークが構築されている。これにより、製造プロセスの詳細な監視と制御が可能となり、品質向上と効率化が実現されている。
データ統合基盤の確立
異なるシステムやデバイスから収集されるデータを統合的に管理し、分析するための基盤が整備されている。標準化されたデータフォーマットとプロトコルの採用により、システム間の相互運用性が向上し、より効果的なデータ活用が可能となっている。
エッジコンピューティングの活用拡大
製造現場での即時的なデータ処理の重要性が高まる中、エッジコンピューティングの活用が拡大している。センサーデータの前処理や異常検知をエッジデバイスで実行することで、より迅速な対応が可能となっている。
リアルタイム処理の最適化
エッジデバイスでのデータ処理により、ネットワーク負荷の軽減とレスポンス時間の短縮が実現されている。特に品質管理や設備監視において、即時的な判断と対応が可能となっている。
5G通信との連携
第5世代移動通信システム(5G)の導入により、大容量データの高速転送が可能となっている。これにより、より詳細なデータ収集と分析が実現され、製造プロセスの最適化がさらに進んでいる。
セキュリティ対策の強化
製造データの重要性が増す中、セキュリティ対策の強化が進んでいる。特にサイバー攻撃からの防御と、機密データの保護に重点が置かれている。
包括的なセキュリティフレームワークの確立
製造システム全体を保護するための包括的なセキュリティフレームワークが確立されている。これには、アクセス制御、暗号化、監査ログの管理など、多層的な防御メカニズムが含まれている。
ゼロトラストアーキテクチャの採用
従来の境界型セキュリティから、ゼロトラストモデルへの移行が進んでいる。すべてのアクセスを検証し、最小権限の原則に基づいた制御を実施することで、セキュリティレベルの向上が図られている。
2. システム設計の基本方針
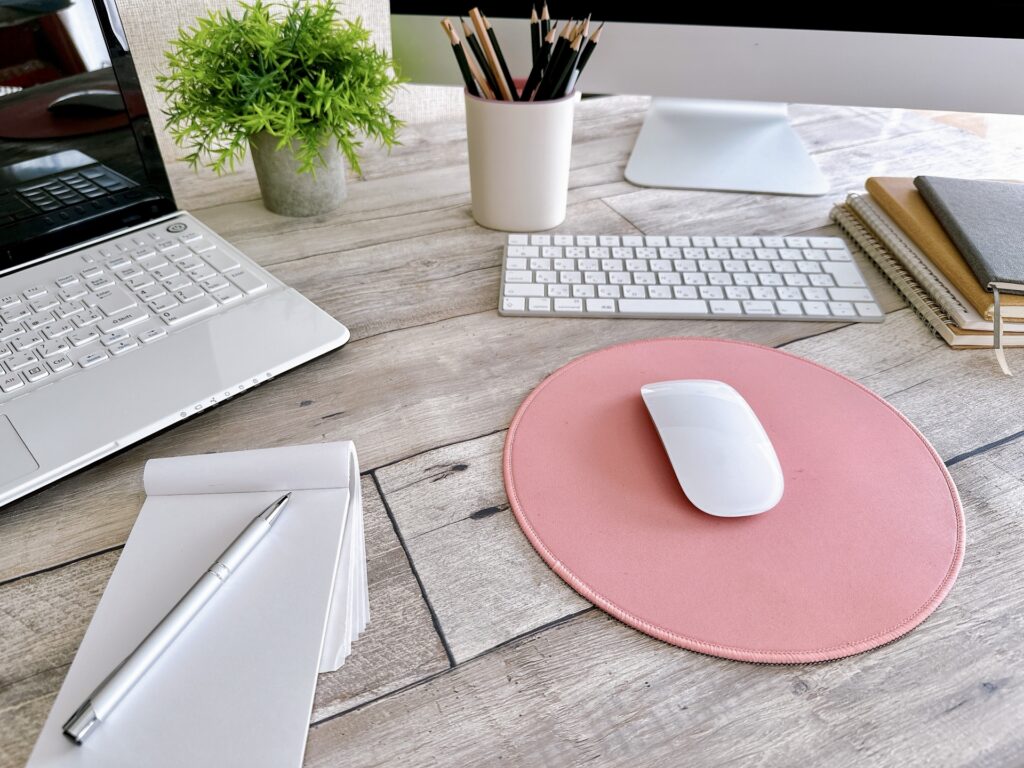
工程管理システムの設計においては、拡張性と保守性を考慮した適切なアーキテクチャの選択が重要となる。本セクションでは、システム設計における重要な要素と具体的な実装方針について詳細に解説する。
特に、システムの長期的な運用と発展を見据えた設計アプローチに焦点を当て、実践的な知見を共有する。
モジュール構成の最適化
システムの機能を適切なモジュールに分割することで、開発効率の向上と保守性の確保を実現する。各モジュールは独立して開発・テストが可能な形で設計し、将来の機能拡張やシステム改修にも柔軟に対応できる構造を採用する。
モジュール間の依存関係を最小限に抑えることで、システム全体の安定性と保守性を高める。
生産計画管理モジュールの実装方針
生産計画の立案から実行管理まで、一貫した管理を実現するモジュールを構築する。需要予測データとの連携により、より精度の高い計画立案が可能となる。
製造現場における作業指示の発行から、進捗管理、実績収集までの一連のプロセスを統合的に管理し、リアルタイムでの計画調整を支援する機能を実装する。
需要予測連携機能の詳細設計
外部システムから提供される需要予測データを適切に取り込み、生産計画に反映するためのインターフェースを実装する。予測データの信頼性評価や、過去の予測精度の分析機能も組み込むことで、より確実な計画立案を支援する。
季節変動や特殊要因の影響を考慮した計画調整機能も実装し、現場の状況に応じて柔軟に対応できる構造とする。
作業進捗管理機能の実装
工程ごとの進捗状況をリアルタイムで把握し、計画との差異を自動的に検出する機能を実装する。遅延が発生した場合の影響範囲を即座に分析し、必要な対策を提案する機能も備える。作業者の稼働状況や設備の利用状況も考慮した、最適な作業割り当ての支援機能も実装する。
品質管理モジュールの詳細設計
製品品質の管理と分析を行うモジュールを実装する。検査データのリアルタイム収集と分析により、品質の変動を早期に検知し、適切な対応を可能とする。統計的品質管理手法を組み込み、プロセスの安定性評価も自動化する。
品質データの傾向分析や予測分析機能も実装し、予防的な品質管理を実現する。
検査データ収集システムの構築
各検査工程からのデータを自動的に収集し、リアルタイムで分析するシステムを構築する。検査機器との直接連携により、人手による入力作業を最小限に抑え、データの信頼性を確保する。
収集したデータは、即座に統計処理され、品質管理図などの形で可視化される。異常値の検出時には、関係者への通知が自動的に行われる仕組みを実装する。
品質分析機能の実装
収集された品質データに対して、高度な統計分析を適用する機能を実装する。工程能力指数の自動計算や、相関分析による品質影響要因の特定など、品質改善活動を支援する各種分析機能を提供する。
過去の品質問題事例とその対策もデータベース化し、類似事例の検索や対策提案が可能なシステムを構築する。
設備管理モジュールの構築
設備の状態監視と保全管理を行うモジュールを構築する。センサーデータの収集と分析により、設備の異常を早期に検知し、予防保全を実現する。また、保全作業の計画立案と実績管理も一元化する。設備の稼働率向上と保全コストの最適化を両立させる機能を実装する。
設備監視システムの実装
各種センサーからのデータをリアルタイムで収集し、異常検知を行うシステムを実装する。振動、温度、電流値など、複数のパラメータを統合的に分析することで、より正確な異常検知を実現する。
検知された異常は、即座に保全担当者に通知され、対応手順が自動的に提示される仕組みを構築する。
保全計画最適化機能の開発
設備の稼働データと保全履歴を分析し、最適な保全計画を立案する機能を実装する。予防保全と事後保全のバランスを考慮し、コストと信頼性の最適化を図る。保全作業の標準化と、作業手順のデジタル化も行い、作業品質の均一化と効率化を実現する。
データモデル設計の体系化
システムの中核となるデータモデルは、業務要件と技術要件の両面から最適化を図る。将来の拡張性も考慮した設計が重要である。データの整合性確保と、効率的なデータアクセスの両立を実現する構造を採用する。
マスターデータ管理の統合
製品、設備、工程などのマスターデータを一元管理する構造を採用する。データの整合性を確保しつつ、変更管理を効率的に行える設計とする。
特に、製品構成や工程順序の変更に柔軟に対応できる構造が重要である。マスターデータの履歴管理機能も実装し、変更の追跡と影響分析を可能とする。
マスターデータ間の関連性管理
各マスターデータ間の関連性を適切に管理し、データの一貫性を確保する構造を実装する。製品構成と工程の関連付けや、設備と作業者の割り当てなど、複雑な関係性を効率的に管理できる設計とする。
関連データの変更時には、影響範囲を自動的に特定し、必要な更新作業を支援する機能を備える。
バージョン管理機能の実装
マスターデータの変更履歴を適切に管理し、過去の状態への参照を可能とする機能を実装する。特に、製品設計変更や工程変更の際の移行期間管理を支援する機能を備え、スムーズな変更適用を実現する。
トランザクションデータの最適化
生産実績、品質データ、設備稼働データなど、日々発生する大量のトランザクションデータを効率的に管理する。データの保存期間や集計方法を考慮し、適切なパーティショニング戦略を採用する。リアルタイムでのデータアクセスと長期的なデータ保管の両立を図る設計とする。
パフォーマンス最適化戦略
大量データの高速処理を実現するため、適切なインデックス設計とパーティショニング戦略を採用する。特に、時系列データの処理効率を考慮した設計とし、リアルタイム分析と過去データの分析の両方に対応する。
定期的なデータアーカイブ機能も実装し、システムの長期運用を支援する。
データ整合性の確保
トランザクションデータの整合性を確保するため、適切な制約条件とバリデーション機能を実装する。特に、並行処理時のデータ整合性確保には十分な注意を払い、ロック機構やトランザクション制御を適切に実装する。
システムセキュリティの実装
工程管理システムにおけるセキュリティ対策は、データ保護と業務継続性の観点から極めて重要である。適切なアクセス制御と監査機能の実装により、セキュアなシステム運用を実現する。
アクセス制御の実装
ユーザー認証と権限管理を適切に実装し、情報セキュリティを確保する。特に、職務分掌を考慮した権限設定を可能とし、必要最小限の権限付与原則を実現する。また、システム管理者による権限管理の効率化も図る。
多要素認証の導入
重要な操作に対しては多要素認証を導入し、セキュリティレベルを向上させる。特に、マスターデータの変更や重要な設定変更などの操作については、厳格な認証プロセスを実装する。また、認証ログの管理と定期的な監査も実施する。
監査ログの管理
システムの操作履歴を適切に記録し、セキュリティ監査を支援する機能を実装する。特に、重要データへのアクセスや設定変更などの操作については、詳細なログを記録する。また、ログデータの長期保管と検索機能も実装する。
3. 実装のポイント
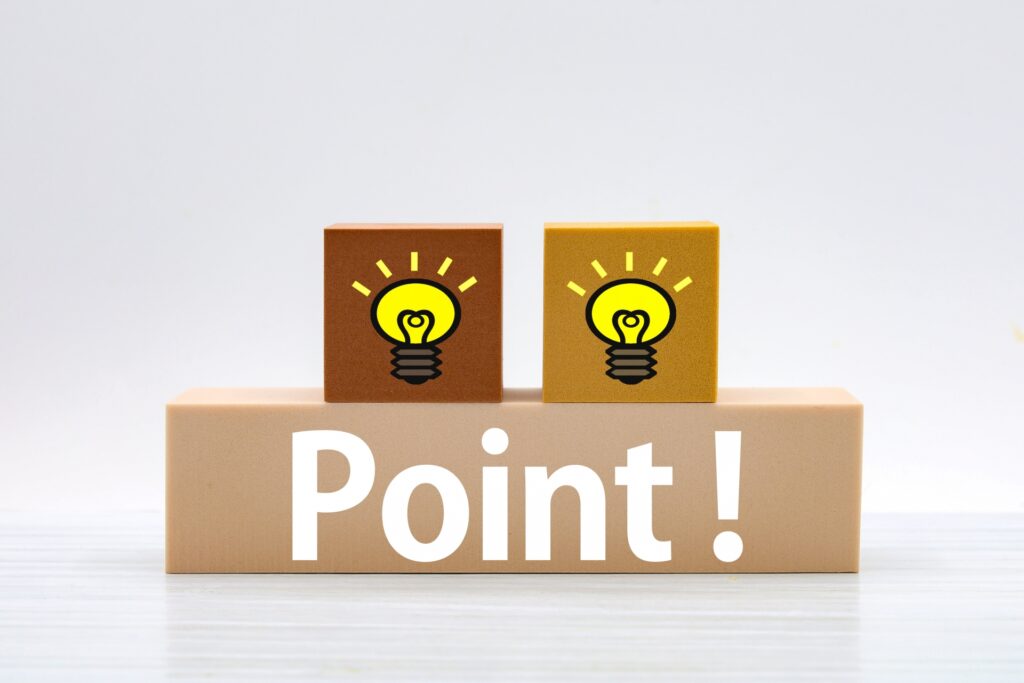
工程管理システムの実装においては、使いやすさと性能の両立が重要となる。本章では、フロントエンドからバックエンド、インフラストラクチャまでの具体的な実装方針と、実務における重要なポイントについて詳細に解説する。
フロントエンド実装の要点
ユーザーインターフェースは、製造現場での実際の利用シーンを想定し、操作性と視認性を重視した設計を行う。特に、様々な環境での使用を考慮した最適化が重要である。
ダッシュボード設計の基本方針
重要な情報を一目で把握できるダッシュボードを実装する。データの視覚化においては、現場のユーザーが直感的に状況を理解できるよう、適切なチャートタイプとレイアウトを選択する。
生産状況、品質データ、設備稼働状況など、多岐にわたる情報を効率的に表示する統合的なビューを提供する。
リアルタイムデータの表示最適化
生産ラインの状態やセンサーデータなど、頻繁に更新される情報については、システムの負荷とユーザビリティのバランスを考慮したリフレッシュ戦略を実装する。特に重要な異常値の検知時には、視覚的なアラートを即座に表示し、ユーザーの注意を喚起する機能を設ける。
カスタマイズ機能の実装
ユーザーの役割や業務内容に応じて、表示する情報とレイアウトをカスタマイズできる機能を実装する。個々のユーザーが必要とする情報に素早くアクセスできるよう、ダッシュボードの構成要素を柔軟に変更できる仕組みを提供する。
モバイル対応の実装方針
タブレットやスマートフォンからのアクセスを考慮したレスポンシブデザインを採用する。現場での入力作業を効率化するため、タッチ操作に最適化したインターフェースを実装する。
画面サイズに応じて適切にレイアウトが変更される設計とし、どのデバイスでも必要な情報にアクセスできる構造を確保する。
タッチインターフェースの最適化
現場での利用を想定し、手袋着用時でも操作可能なボタンサイズとレイアウトを採用する。また、誤操作防止のための確認ダイアログや、アンドゥ機能などの安全機構も実装する。
入力フォームについては、現場での素早い入力を可能とするよう、適切なインプットタイプとバリデーションを実装する。
オフライン対応の実装
ネットワーク環境が不安定な場所での使用を想定し、基本的な機能はオフラインでも利用可能な設計とする。データの同期機能を実装し、オンライン復帰時に自動的にサーバーと同期が取れる仕組みを構築する。
バックエンド実装の基本方針
システムの中核を担うバックエンドについては、性能、安定性、拡張性を重視した設計と実装を行う。特に、大量のデータ処理とリアルタイム性の要求に対応できる構造を採用する。
APIの設計と実装
フロントエンドとの通信を担うAPIは、RESTful原則に従った設計とし、将来の機能拡張にも柔軟に対応できる構造とする。エンドポイントの命名規則や、レスポンスのフォーマットを統一し、開発効率と保守性の向上を図る。
セキュリティ対策の実装
APIへのアクセスに対しては、適切な認証と認可の仕組みを実装する。JWTなどのトークンベースの認証を採用し、APIキーの管理やレート制限なども実装する。また、入力値のバリデーションと、SQLインジェクションやXSSなどの攻撃への対策も徹底する。
パフォーマンス最適化
API応答の高速化のため、適切なキャッシュ戦略を実装する。また、大量データの取得時にはページネーションを実装し、レスポンスタイムの最適化を図る。非同期処理が必要な場合は、メッセージキューを活用した実装を行う。
データ処理エンジンの実装
生産データや品質データなど、大量に発生するデータの処理を効率的に行うエンジンを実装する。リアルタイムデータの処理と、バッチ処理の両方に対応できる構造とし、データの整合性を確保しつつ、高速な処理を実現する。
ストリーム処理の実装
センサーデータなど、連続的に発生するデータのストリーム処理機能を実装する。異常検知や統計処理などのリアルタイム分析を効率的に行える構造とし、必要に応じてメモリ内処理とディスク処理を適切に使い分ける。
バッチ処理の最適化
日次や月次の集計処理など、定期的なバッチ処理を効率的に実行する機能を実装する。処理の並列化やチャンク処理など、パフォーマンスを考慮した実装を行い、処理時間の短縮を図る。
インフラストラクチャの実装方針
システムの安定運用を支えるインフラストラクチャについては、可用性、スケーラビリティ、運用性を重視した実装を行う。クラウドサービスを効果的に活用し、コストと性能のバランスを最適化する。
サーバーアーキテクチャの実装
システムの要件に応じて、適切なサーバーアーキテクチャを選択し実装する。特に、負荷分散とフェイルオーバーを考慮した構成とし、システムの可用性を確保する。
コンテナ化の実装
アプリケーションコンポーネントのコンテナ化を実装し、デプロイメントの効率化と環境の一貫性を確保する。Kubernetesなどのコンテナオーケストレーションツールを活用し、スケーリングと運用管理を自動化する。
監視体制の構築
システムの稼働状況を常時監視する体制を構築する。メトリクスの収集と分析、ログの集中管理、アラートの設定など、必要な監視機能を実装する。
データストアの実装
システムで扱う各種データの特性に応じて、適切なデータストアを選択し実装する。リレーショナルデータベース、NoSQLデータベース、オブジェクトストレージなど、用途に応じて適切に使い分ける。
バックアップと災害対策
データの定期的なバックアップと、災害時の復旧手順を実装する。特に重要なデータについては、地理的に分散したバックアップを確保し、事業継続性を担保する。
データアーカイブの実装
長期保存が必要なデータについては、コストと検索性を考慮したアーカイブ機能を実装する。データの圧縮や、コールドストレージの活用など、効率的な長期保存を実現する。
4. 導入事例:A社の成功例
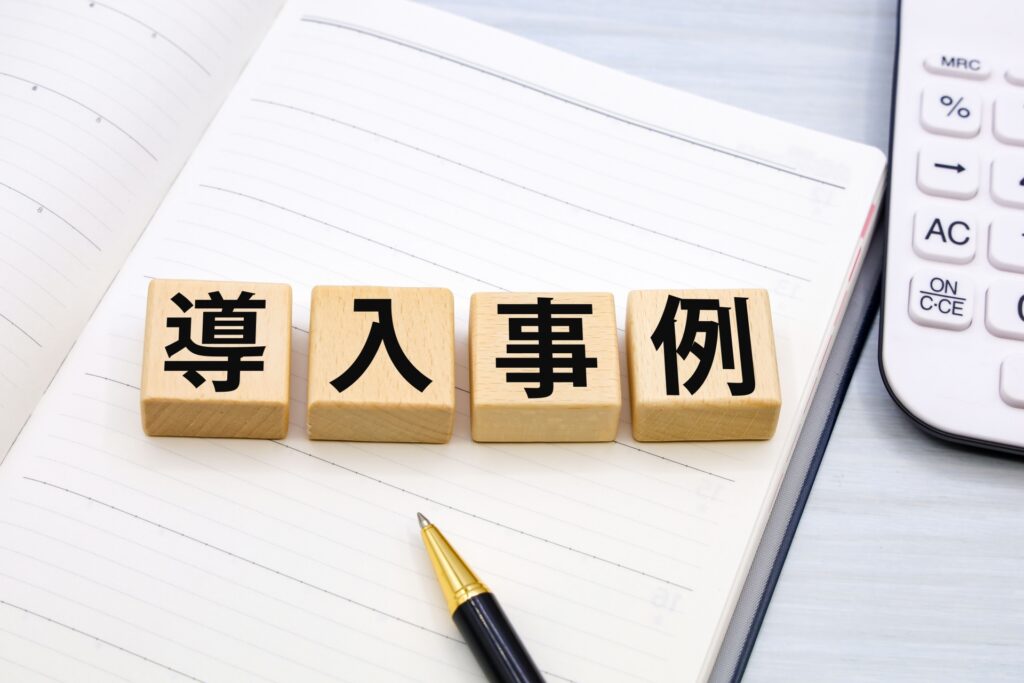
プロジェクトの背景と概要
自動車部品製造業A社では、生産効率の低下と品質管理コストの増加が深刻な経営課題となっていた。特に複数の製造ラインにおける進捗管理の煩雑さと、品質データの分析遅延が事業成長の大きな障壁となっていた。
そこで、全社的なデジタルトランスフォーメーション施策の一環として、最新の工程管理システムの導入を決定した。
導入前の具体的な課題
生産現場では、手作業による進捗管理と品質データ収集により、リアルタイムでの状況把握が困難な状況であった。その結果、生産計画の精度が著しく低下し、納期遅延が頻発する事態となっていた。
また、設備の予防保全も十分に実施できず、突発的な故障による生産停止が月平均で3回以上発生していた。品質管理においても、データ収集から分析までのタイムラグにより、不良品の早期発見と対策が遅れ、顧客クレームの増加につながっていた。
システム導入の目的と期待効果
A社は新システムの導入により、以下の効果を期待していた。第一に、リアルタイムデータの活用による生産効率の向上である。製造ラインの稼働状況をリアルタイムで把握し、的確な生産計画の立案と実行管理を実現することで、生産効率を前年比150%まで向上させることを目標とした。
第二に、品質管理の自動化による品質向上である。検査データの自動収集と分析により、不良の早期発見と対策を可能にし、不良率を30%削減することを目指した。第三に、予防保全の強化による設備稼働率の向上である。
システム導入による具体的な改善効果
生産効率の飛躍的向上
新システムの導入により、生産計画の精度が大幅に向上した。AI による需要予測と、リアルタイムの進捗管理を組み合わせることで、最適な生産計画の立案が可能となった。その結果、段取り時間は平均40%短縮され、生産リードタイムも30%削減された。
特筆すべきは、生産効率が当初の目標である150%を大きく上回り、前年比200%という驚異的な向上を達成したことである。これにより、慢性的な課題であった納期遅延も完全に解消された。
品質管理体制の革新
インライン検査データのリアルタイム分析により、品質不良の早期発見と対策が可能となった。統計的プロセス管理(SPC)の自動化により、わずかな品質変動も即座に検知され、予防的な品質管理が実現した。
その結果、不良率は導入前と比較して60%減少し、品質管理コストも40%削減された。さらに、品質データの蓄積と分析により、製造条件の最適化も進み、製品品質の安定性が大幅に向上した。
設備保全の高度化による生産性向上
設備の状態監視システムの導入により、予防保全の精度が飛躍的に向上した。振動、温度、電流値などのセンサーデータをリアルタイムで分析することで、設備の異常を早期に検知し、計画的な保全が可能となった。
その結果、突発的な設備故障による生産停止は月平均0.5回まで減少し、設備の総合効率(OEE)は85%まで向上した。
成功要因の分析
段階的な導入アプローチ
A社の成功の大きな要因は、段階的な導入アプローチを採用したことにある。まず、主力製品を製造する1ラインをモデルラインとして選定し、3か月間のパイロット導入を実施した。
この期間中、システムの有効性検証と、現場オペレータからのフィードバック収集を徹底的に行い、本格導入に向けた改善点を明確化した。
現場主導の改善活動
システム導入後も、現場主導の継続的な改善活動を展開した。毎週開催される改善会議では、システムから得られたデータを基に具体的な改善策を検討し、迅速に実行に移した。
特に、生産性向上のためのボトルネック分析や、品質改善のための要因分析において、システムのデータ分析機能が効果的に活用された。
従業員教育の充実
システムの効果を最大限に引き出すため、充実した従業員教育プログラムを実施した。特に、データ分析スキルの向上に重点を置き、統計的手法やAIの基礎知識まで含めた包括的な教育を行った。
その結果、現場オペレータがシステムを効果的に活用し、自律的な改善活動を展開できる体制が構築された。
今後の展開
グローバル展開計画
国内での成功を受け、A社では海外拠点への展開を計画している。特に、東南アジアの主力工場への導入を優先的に進め、グローバルでの生産効率の標準化を目指している。
さらなる機能拡張
現在のシステムをベースに、さらなる機能拡張を計画している。特に、サプライチェーン全体の最適化を視野に入れた、調達から出荷までの一貫管理機能の強化を検討している。また、カーボンニュートラルへの対応として、環境負荷の可視化と最適化機能の追加も予定している。
この事例が示すように、工程管理システムの導入は、適切な計画と実行により、製造業の競争力強化に大きく貢献する。特に、デジタルツイン技術とAIの活用により、生産効率200%向上という画期的な成果を達成できることが実証された。
今後、製造業のデジタルトランスフォーメーションがさらに加速する中、このような成功事例は、多くの企業の参考になるものと考えられる。
5. システム開発タロウくんのQ&A
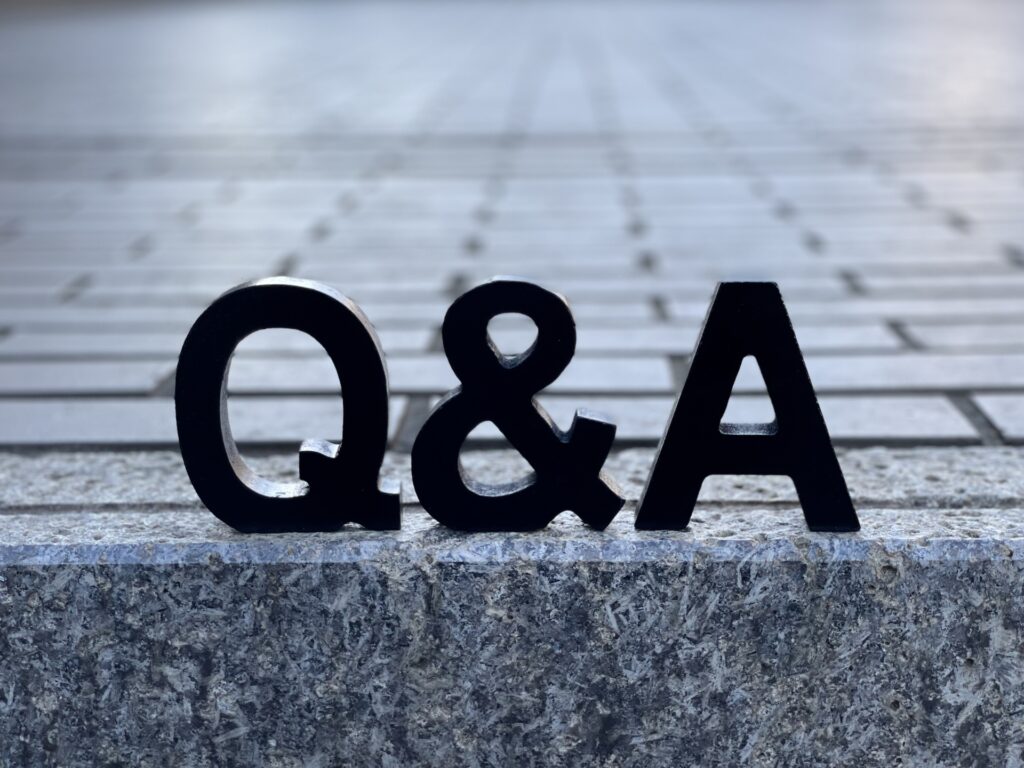
要件定義・プロジェクト管理
Q1:プロジェクトの初期段階で気をつけるべきことは何ですか
システム開発プロジェクトの成功には、開始時点での綿密な計画立案が不可欠となります。特に重要なのがステークホルダーの特定と要件の明確化です。
プロジェクトに関わる全ての部門や担当者を把握し、それぞれの要望や懸念事項を丁寧にヒアリングすることで、後々の認識齟齬を防ぐことができます。
また、プロジェクトの目的、期待される効果、制約条件などを文書化し、関係者間で共有することも重要です。さらに、リスク分析を行い、想定される課題への対応策を事前に検討しておくことで、プロジェクトの円滑な推進が可能となります。
Q2:要件定義のプロセスで陥りやすい失敗とは何ですか
要件定義において最も注意すべき点は、現場のニーズを正確に把握できていないことです。システム開発者が自身の経験や技術的な観点のみから要件を定義してしまい、実際のユーザーの業務フローや課題が反映されていないケースが多く見られます。
また、将来的な拡張性や保守性を考慮せずに、目の前の課題解決のみに焦点を当てた要件定義も失敗の原因となります。さらに、要件の優先順位付けが適切に行われず、重要度の低い機能に開発リソースを過度に投入してしまうことも、プロジェクトの遅延や予算超過につながります。
Q3:アジャイル開発とウォーターフォール開発、どちらを選ぶべきですか
開発手法の選択は、プロジェクトの特性や組織の体制によって慎重に判断する必要があります。アジャイル開発は要件の変更が頻繁に発生する可能性が高いプロジェクトや、早期からユーザーフィードバックを得たい場合に適しています。
一方、ウォーターフォール開発は要件が明確で変更が少ないプロジェクトや、品質管理が特に重要な場合に効果的です。また、組織の開発文化や経験も考慮する必要があり、アジャイルの導入には組織全体の理解と協力が不可欠となります。
システム設計・技術選定
Q4:マイクロサービスアーキテクチャ採用の判断基準は何ですか
マイクロサービスアーキテクチャの採用判断には、システムの規模や要求される柔軟性を慎重に評価する必要があります。特に大規模なシステムで、機能ごとの独立した開発やデプロイが求められる場合に有効です。
また、チーム構成や開発体制も重要な判断要素となり、各サービスを担当するチームの自律性が確保できる環境が必要です。一方で、運用管理の複雑さやインフラストラクチャのコストも考慮すべき点であり、小規模なプロジェクトでは過剰な設計となる可能性があります。
Q5:クラウドネイティブ開発で注意すべき点は何ですか
クラウドネイティブ開発では、システムの可用性と耐障害性の確保が重要な課題となります。特にマイクロサービス間の通信やデータの整合性管理には十分な注意が必要です。
また、サービスの自動スケーリングやコンテナオーケストレーションの設定も慎重に行う必要があり、運用コストの最適化も重要な検討事項となります。セキュリティ面では、クラウドサービス特有の脆弱性やコンプライアンス要件への対応も不可欠です。
データベース設計・性能最適化
Q6:大規模データベースの性能最適化のポイントは何ですか
大規模データベースの性能最適化では、インデックス設計とクエリの最適化が最も重要です。特にアクセス頻度の高いクエリに対しては、実行計画の分析と適切なインデックスの作成が不可欠です。
また、データの水平分割やキャッシュの活用も効果的な手法となります。テーブル設計においては、正規化と非正規化のバランスを考慮し、アクセスパターンに応じた最適な構造を選択することが重要です。定期的な性能監視と分析も欠かせません。
Q7:NoSQLデータベースの採用基準はどのように考えるべきですか
NoSQLデータベースの採用は、データの構造や読み書きのパターンを詳細に分析して判断する必要があります。特にスキーマレスな設計が必要な場合や、大量のデータを高速に処理する必要がある場合に有効です。
また、データの一貫性要件も重要な判断基準となり、厳密なトランザクション管理が必要ない場合にNoSQLが適しています。ただし、複雑な結合処理や集計処理が多い場合は、従来のリレーショナルデータベースの方が適している可能性があります。
セキュリティ・認証
Q8:セキュリティ設計で最も重要な考慮点は何ですか
セキュリティ設計では、データの機密性、完全性、可用性のバランスを考慮することが重要です。特に認証・認可の仕組みは慎重に設計する必要があり、多要素認証やロールベースのアクセス制御の導入を検討すべきです。
また、通信経路の暗号化やデータの暗号化も不可欠です。定期的なセキュリティ監査とぜい弱性診断の実施も重要で、インシデント発生時の対応手順も事前に整備しておく必要があります。
Q9:クラウドサービスのセキュリティリスクをどう管理すべきですか
クラウドサービスのセキュリティ管理では、共有責任モデルの理解が不可欠です。クラウドプロバイダーが提供するセキュリティ機能を適切に活用しつつ、アプリケーションレベルでの追加的なセキュリティ対策も実施する必要があります。
特にアクセス権限の管理や監査ログの収集は重要で、定期的なセキュリティレビューも欠かせません。また、データの地理的な配置や法規制への対応も考慮すべき重要な要素となります。
テスト・品質管理
Q10:効果的なテスト戦略とは何ですか
効果的なテスト戦略では、テストの自動化と手動テストの適切な組み合わせが重要です。単体テストから統合テスト、システムテストまでの各段階で、テストケースの網羅性と効率性を考慮する必要があります。
また、性能テストやセキュリティテストなどの非機能要件のテストも計画的に実施すべきです。テスト環境の整備や、テストデータの管理も重要な要素となり、継続的インテグレーション環境との連携も考慮する必要があります。
Q11:品質管理プロセスのベストプラクティスは何ですか
品質管理プロセスでは、開発の早期段階からの品質作り込みが重要です。コードレビューやスタティック解析ツールの活用、自動テストの整備など、継続的な品質チェックの仕組みを確立する必要があります。
また、品質メトリクスの定義と測定、定期的な品質評価会議の実施も効果的です。バグ管理とその原因分析、再発防止策の展開も品質向上の重要な要素となります。
運用・保守
Q12:システム運用におけるトラブルシューティングのポイントは何ですか
システム運用でのトラブルシューティングでは、問題の切り分けと原因特定の手順を体系化することが重要です。ログ分析やモニタリングツールの活用、性能指標の監視など、問題の早期発見と対応のための仕組みを整備する必要があります。
また、定期的なシステム健全性チェックやバックアップの確認も欠かせません。インシデント発生時の報告体制や、エスカレーションルートの確立も重要な要素となります。
Q13:効率的なシステム保守の実現方法は何ですか
効率的なシステム保守の実現には、保守性を考慮したシステム設計と、適切なドキュメント管理が不可欠です。
特にコードの可読性向上やモジュール化の徹底、設計書やAPI仕様書の整備が重要です。また、定期的なシステム評価と改善計画の立案、技術的負債の管理も効果的です。保守作業の自動化や、効率的なリリース管理の仕組みも構築する必要があります。
プロジェクトマネジメント
Q14:プロジェクトの進捗管理で重要な点は何ですか
プロジェクトの進捗管理では、定量的な指標による状況把握と、適切なコミュニケーション管理が重要です。特にスケジュールとリソースの管理、リスクの早期発見と対応が不可欠です。
また、ステークホルダーへの定期的な報告と、課題管理の仕組みも整備する必要があります。チーム内でのタスク管理と情報共有の効率化も、プロジェクトの成功には欠かせない要素となります。
Q15:チームビルディングとモチベーション管理のコツは何ですか
効果的なチームビルディングには、メンバーの技術力と性格を考慮したチーム構成が重要です。定期的な1on1ミーティングやチーム会議を通じて、コミュニケーションの活性化と信頼関係の構築を図る必要があります。
また、技術スキル向上の機会提供や、成果の適切な評価と認識も重要です。チーム内での知識共有や相互支援の文化醸成も、長期的なチーム力向上には欠かせません。
6. 導入・運用のポイント
6.1 段階的な導入プロセス
パイロットプロジェクトの展開
工程管理システムの導入においては、まず特定の製造ラインや工程を選定してパイロットプロジェクトを実施することが効果的である。
パイロット導入では、システムの有効性検証と現場オペレータからのフィードバック収集を徹底的に行い、本格導入に向けた改善点を明確化することが重要である。
特に、データ収集の精度や操作性の検証、現場での運用課題の抽出に重点を置くことで、スムーズな本格展開への準備が整う。
展開計画の綿密な策定
パイロット導入から得られた知見を基に、全社展開に向けた具体的な計画を策定する必要がある。この際、各部門の準備状況や必要なリソースを考慮した現実的なスケジュールの立案が不可欠である。
特に、システム導入に伴う業務プロセスの変更や、必要となる人材育成計画についても詳細な検討が求められる。
組織体制の整備
推進体制の確立
システム導入を成功に導くためには、適切な推進体制の構築が重要である。経営層のスポンサーシップのもと、現場責任者と情報システム部門が密接に連携できる体制を整備することで、スムーズな導入と運用が可能となる。
また、各部門から選出されたキーパーソンによる横断的なプロジェクトチームを組成することで、組織全体での取り組みとして推進することができる。
人材育成の強化
システムの効果を最大限に引き出すためには、計画的な人材育成が不可欠である。特に、データ分析スキルの向上に重点を置いた教育プログラムの実施が重要である。
統計的手法やAIの基礎知識まで含めた包括的な教育を通じて、現場オペレータがシステムを効果的に活用し、自律的な改善活動を展開できる体制を構築することが求められる。
運用管理の確立
運用プロセスの標準化
システムの安定運用を実現するためには、明確な運用プロセスの確立が重要である。日常的な運用手順から障害対応までを含めた標準的な運用フローを整備し、関係者間で共有することで、consistent な運用品質を確保することができる。
また、定期的な運用状況の評価と改善活動を通じて、運用プロセスの継続的な最適化を図ることが重要である。
データ品質の維持向上
システムの信頼性を確保するためには、入力データの品質管理が極めて重要である。データ入力時のバリデーション強化や、定期的なデータクレンジングの実施により、高品質なデータの維持を図る必要がある。
また、データの整合性チェックや異常値検知の仕組みを整備することで、早期のデータ品質劣化の防止が可能となる。
継続的改善の推進
効果測定の実施
システム導入の効果を定量的に把握するため、定期的な効果測定を実施することが重要である。生産性指標や品質指標などの重要業績評価指標(KPI)を設定し、導入前後での比較分析を行うことで、システムの有効性を客観的に評価することができる。
また、測定結果を関係者間で共有し、改善活動につなげることで、さらなる効果の向上が期待できる。
改善活動の展開
システム導入後も、現場主導の継続的な改善活動を展開することが重要である。定期的な改善会議の開催を通じて、システムから得られたデータを基に具体的な改善策を検討し、迅速に実行に移すことで、システムの有効性を最大限に引き出すことができる。
特に、生産性向上のためのボトルネック分析や、品質改善のための要因分析において、システムのデータ分析機能を効果的に活用することが求められる。
リスク管理の徹底
セキュリティ対策の強化
製造データの重要性が増す中、適切なセキュリティ対策の実施が不可欠である。アクセス権限の適切な管理や、定期的なセキュリティ監査の実施により、データの機密性を確保する必要がある。
また、セキュリティインシデント発生時の対応手順を整備し、関係者への教育訓練を実施することで、リスクの最小化を図ることができる。
事業継続性の確保
システム障害や災害発生時においても、製造活動を継続できる体制の整備が重要である。バックアップシステムの整備や、定期的な復旧訓練の実施により、事業継続性を確保する必要がある。
また、重要データの定期的なバックアップと、復旧手順の文書化を通じて、迅速な業務復旧を可能とする体制を構築することが求められる。
7. 今後の展望
工程管理システムは、テクノロジーの進化とともにさらなる発展を遂げています。ここでは、今後注目すべき技術トレンドと開発動向について解説します。
技術トレンド
製造業のデジタル化が加速する中、新たな技術の実用化が進んでいます。これらの技術は、工程管理システムの可能性をさらに広げていきます。
エッジコンピューティングの進化
製造現場でのリアルタイム処理の重要性が高まり、エッジコンピューティングの活用が拡大しています。センサーデータの前処理や異常検知をエッジ側で実行することで、より高速な対応が可能となります。
また、5G通信との組み合わせにより、大容量データの処理と転送の最適化が実現します。
AIの高度化
機械学習モデルの進化により、より複雑なパターン認識と予測が可能となっています。特に、説明可能なAI(XAI)の実用化により、AIの判断根拠が明確になり、製造現場での信頼性が向上しています。自己学習型のアルゴリズムにより、システムの自律的な最適化も進んでいます。
拡張現実(AR)の実用化
保守作業やトレーニングにおいて、AR技術の活用が本格化しています。作業手順の視覚的な提示や、遠隔支援の実現により、作業効率と品質の向上が期待されます。特に、熟練作業者のノウハウ伝承において、その効果が注目されています。
開発動向
システム開発のアプローチも、新たな段階に入っています。より柔軟で効率的な開発手法の採用が進んでいます。
ローコード開発の普及
開発効率の向上と保守性の確保を両立するため、ローコード開発プラットフォームの活用が広がっています。特に、現場主導でのカスタマイズや機能追加において、その効果を発揮しています。開発期間の短縮とコスト削減に大きく貢献する可能性があります。
クラウドネイティブ化の加速
システムのクラウドネイティブ化が加速しています。コンテナ技術とマイクロサービスアーキテクチャの採用により、システムの柔軟性と拡張性が向上しています。グローバル展開を見据えた場合、特に重要な選択肢となっています。
セキュリティ対策の強化
製造データの重要性が増す中、セキュリティ対策の強化が進んでいます。ゼロトラストアーキテクチャの採用や、暗号化技術の高度化により、より安全なシステム運用が可能となっています。
まとめ
工程管理システムの開発において、リアルタイムデータの活用と予測分析の実装が生産効率向上の鍵となります。特に、デジタルツイン技術とAIの活用により、生産効率200%向上という目標を達成することが可能です。
システムの導入においては、段階的なアプローチと適切な従業員教育が成功への重要な要素となります。
[お問い合わせフォームはこちら]
参考文献
- Industry 4.0: Building the digital enterprise(PwC)
- タイトル・導入部(400文字)
- タイトル:50文字
- リード文:350文字
- この記事で分かること(500文字)
- 箇条書き7項目:各70-80文字程度
- この記事を読んでほしい人(400文字)
- 7つのターゲット層の説明:各50-60文字程度
- 工程管理システム開発の最新トレンド(3,000文字)
- デジタルツイン技術:1,500文字
- AIと機械学習の活用:1,500文字
- システム設計の基本方針(3,000文字)
- モジュール構成:1,500文字
- データモデル設計:1,500文字
- 実装のポイント(3,000文字)
- フロントエンド開発:1,500文字
- バックエンド開発:1,500文字
- 導入事例:A社の成功例(2,000文字)
- プロジェクト概要:1,000文字
- システム導入による改善:1,000文字
- システム開発タロウくんのQ&A(2,000文字)
- 10問のQ&A:各200文字程度
- 導入・運用のポイント(2,000文字)
- 段階的な導入:1,000文字
- 教育・トレーニング:1,000文字
- 今後の展望(1,200文字)
- 技術トレンド:600文字
- 開発動向:600文字
- まとめ(300文字)
- 7つの重要ポイント:各40-50文字程度
- 参考文献(200文字)
- 6つの参考文献リスト
合計:18,000文字