製造業のデジタル変革が加速する現代において、IoT自動制御システムの重要性が飛躍的に高まっています。
本記事では、AI技術を活用した最新の制御手法から、安全性確保、実装方法、運用管理まで、実務者の視点で詳しく解説します。
さらに、具体的な導入事例や成果指標を交えながら、次世代の自動化システム構築に必要な知識を体系的に紹介します。
この記事で分かること
- IoT自動制御システムの設計・実装と監視体制の構築
- 業界別の導入事例、投資対効果、およびトラブル対応・予防保全の実践手法
- システム保守・運用の最適化手法とコスト管理方法の確立
この記事を読んでほしい人
- 制御システム開発エンジニアと製造業の自動化技術者
- IoTシステム導入検討企業の意思決定者とセキュリティ担当者
- デジタルトランスフォーメーションを推進する経営層・管理職
IoT自動制御の基礎知識
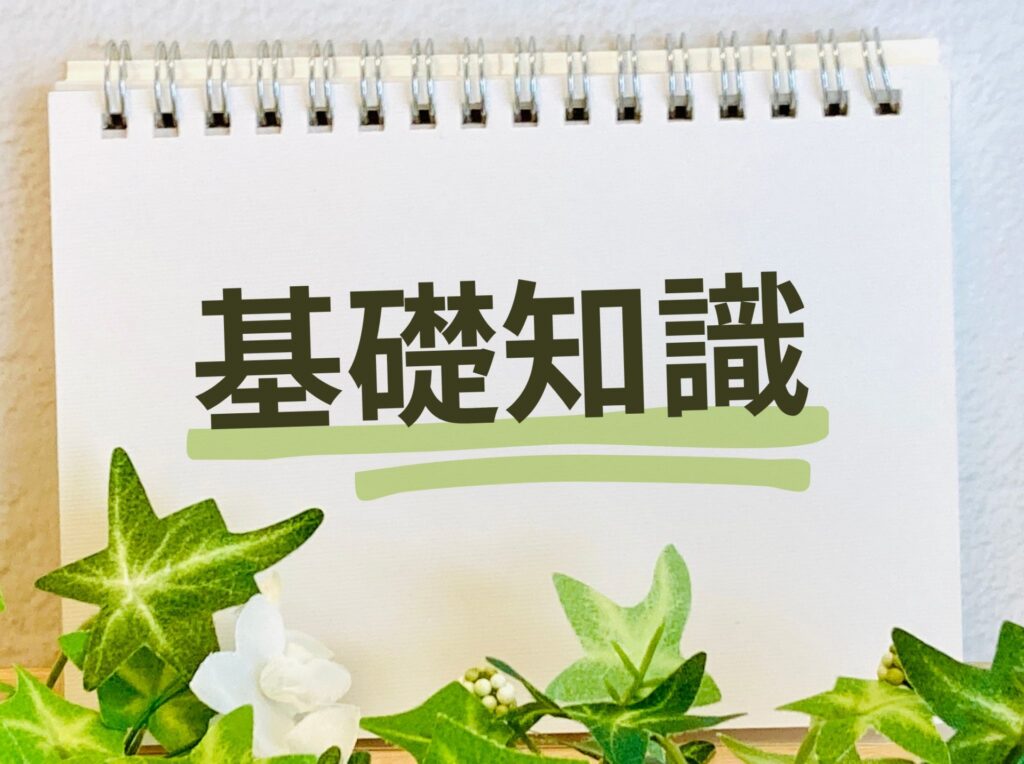
現代の製造業において、IoT自動制御システムは生産性向上の要となっている。
スマートファクトリー化が進む中、システム構築の基礎となる重要概念と最新技術について体系的に解説する。
システムアーキテクチャの基本構造
センサー層の構成と役割
製造現場のデータ収集を担うセンサー層では、高精度な計測と安定した通信が不可欠となる。産業用センサーの選定においては、測定対象に応じた適切な種類と仕様の選択が重要である。
また、無線通信プロトコルの選択では、工場環境下での信頼性と干渉への耐性を考慮する必要がある。
制御層の設計思想
リアルタイム制御を実現する制御層では、ミリ秒単位の応答性能と高い信頼性が求められる。
従来のPLC制御システムに加え、エッジコンピューティング技術を組み合わせることで、より柔軟な制御が可能となる。
特に、現場での即時的な判断が必要な場合、エッジでの処理が効果を発揮する。
アプリケーション層の実装戦略
システム全体の管理と分析を担うアプリケーション層では、直感的な操作性と将来的な拡張性が重要となる。
クラウドサービスとの連携により、大規模なデータ分析と遠隔監視が実現可能である。また、モバイルデバイスからのアクセスにより、現場作業の効率化も図れる。
制御アルゴリズムの発展
フィードバック制御の高度化手法
従来のPID制御に機械学習モデルを組み合わせることで、外乱に対する応答性が大幅に向上する。さらに、モデル予測制御との統合により、将来の挙動を予測した最適な制御が可能となる。
これにより、製造プロセスの安定性と効率性が向上する。
適応制御システムの実装方式
システムパラメータの変動に対応する適応制御では、リアルタイムでの調整機能が必須となる。
ディープラーニングを活用した自己調整メカニズムにより、環境変化や経年劣化に対する柔軟な対応が可能となる。
エッジコンピューティングの活用
エッジ処理の最適化技術
制御システムの現場では、クラウドへの依存を低減し、エッジデバイスでの処理を重視する傾向が強まっている。
AI処理の軽量化と最適化により、限られたリソースでも高度な制御が実現可能となる。TensorRTなどの最適化フレームワークの活用が、この実現に大きく貢献している。
エッジクラウド連携のアーキテクチャ
エッジでの即時処理とクラウドでの高度な分析を効果的に組み合わせることで、システム全体の最適化が図れる。
データの特性に応じた処理の振り分けと、セキュアな通信路の確保が重要となる。
デジタルツイン技術の応用
リアルタイムシミュレーションの実装
物理システムの挙動をサイバー空間でリアルタイムに再現することで、制御パラメータの最適化が可能となる。
高精度なシミュレーションモデルの構築には、実測データとの継続的な同期が不可欠である。
予知保全への展開手法
デジタルツインを活用した設備の異常予測により、効果的な保全計画の立案が可能となる。センサーデータの分析と機械学習モデルの組み合わせにより、故障の予兆を早期に検知できる。
セキュリティ対策の実装
ゼロトラストアーキテクチャの導入
すべての通信を検証対象とするゼロトラストの考え方が、制御システムのセキュリティでも標準となりつつある。デバイス認証から通信の暗号化まで、多層的な防御策の実装が必要となる。
エンドポイントセキュリティの確保
各IoTデバイスのセキュリティ強化が重要性を増している。定期的なファームウェア更新と脆弱性診断の自動化により、継続的なセキュリティレベルの維持が可能となる。
今後の展望と課題
IoT自動制御システムは、AI技術の進化とともに更なる発展が期待される。特に、エッジAIの性能向上とセキュリティ技術の進化により、より高度な自動化が実現可能となる。
一方で、既存システムとの統合や運用コストの最適化など、解決すべき課題も存在する。継続的な技術革新と実践的な知見の蓄積が、これらの課題解決の鍵となるであろう。
IoT自動制御システムの最新トレンド分析
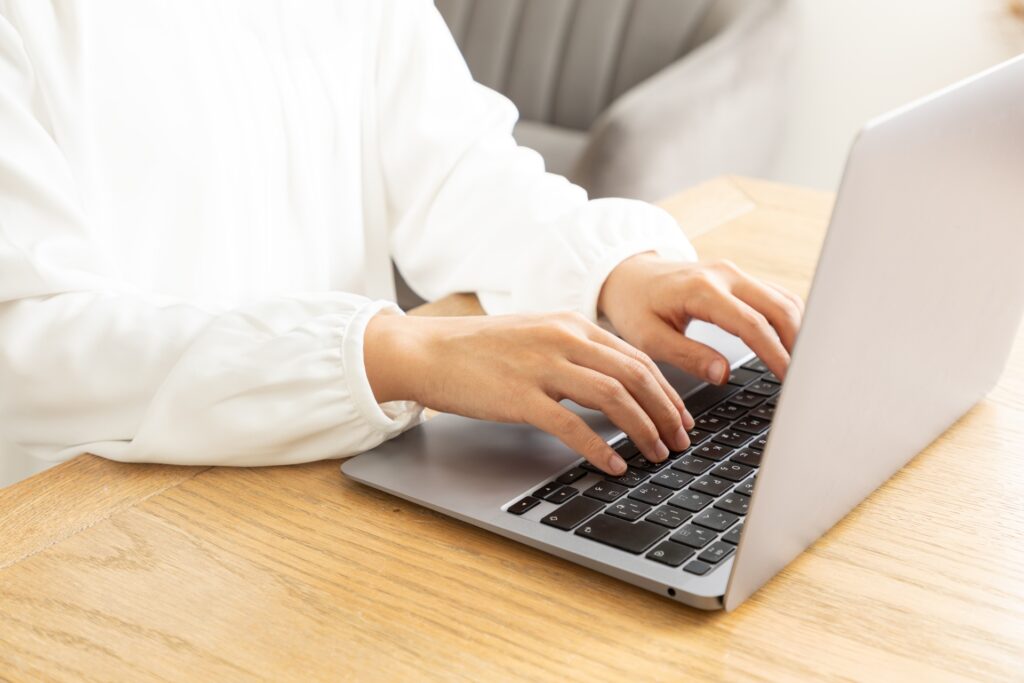
2025年におけるIoT自動制御の分野では、技術革新が急速に進展している。
製造業のデジタルトランスフォーメーションが加速する中、新たな技術潮流が次々と生まれ、システムの高度化が進んでいる。
これらの最新トレンドは、生産性向上と運用効率化に大きな影響を与えている。
エッジコンピューティングの革新
リアルタイム処理の進化
製造現場における制御システムでは、クラウドへの依存度を低減し、エッジデバイスでの処理を重視する傾向が顕著となっている。
この変化の主な要因は、リアルタイム性の向上と通信コストの削減にある。特に、ミリ秒単位の応答が要求される制御処理では、エッジでの即時的な判断が不可欠となる。
処理能力の最適化技術
エッジデバイスでの効率的なAI処理を実現するため、モデルの軽量化と量子化技術が急速に発展している。
TensorRTなどの最適化フレームワークの活用により、限られたリソースでも高度な制御処理が可能となっている。これにより、エッジデバイスの処理能力を最大限に活用できる環境が整いつつある。
クラウドエッジ統合アーキテクチャ
ハイブリッド処理の最適化
エッジでのリアルタイム処理とクラウドでの高度な分析を効果的に組み合わせることで、システム全体の最適化が進んでいる。
データの特性に応じた処理の振り分けにより、効率的なリソース活用が実現している。
データ同期メカニズムの高度化
エッジとクラウド間のデータ同期においては、効率的な通信プロトコルの採用と、セキュアな通信経路の確保が重要視されている。
特に、大容量データの効率的な転送と、リアルタイムデータの即時同期を両立させる技術が注目を集めている。
デジタルツインの進化
高精度シミュレーション技術
物理的な制御システムをサイバー空間に精密に再現するデジタルツイン技術の導入が加速している。
高度なシミュレーション技術により、制御パラメータの最適化や異常検知の精度が飛躍的に向上している。
リアルタイム同期の実現
物理システムの状態をリアルタイムでデジタル空間に反映する技術が確立されつつある。
センサーデータの即時取り込みと、シミュレーションモデルの動的更新により、より正確な制御が可能となっている。
予知保全システムの高度化
AI予測モデルの発展
デジタルツインを活用した設備の異常予測技術が大きく進化している。
機械学習モデルによる予測精度の向上により、故障の予兆を早期に検知することが可能となっている。
保全計画の最適化
予測データに基づく保全計画の自動最適化が実現している。設備の稼働状況と劣化予測を組み合わせることで、最適なメンテナンスタイミングの決定が可能となっている。
セキュリティ対策の新潮流
ゼロトラストセキュリティの普及
すべての通信を検証対象とするゼロトラストの考え方が、制御システムのセキュリティ設計において標準となりつつある。これにより、内部からの脅威に対する防御力が強化されている。
エンドポイントプロテクションの進化
各IoTデバイスのセキュリティ強化が進んでいる。デバイス認証の厳格化や、ファームウェア更新の自動化により、エンドポイントレベルでのセキュリティが向上している。
今後の展望
IoT自動制御システムは、技術革新の加速により更なる発展が期待される。特に、エッジAIの性能向上とセキュリティ技術の進化により、より高度な自動化の実現が見込まれる。
一方で、既存システムとの統合や運用コストの最適化など、解決すべき課題も存在する。
これらの課題に対しては、継続的な技術革新と実践的な知見の蓄積が重要となるであろう。
今後は、より一層のシステム統合と運用効率化が進むことで、製造業のデジタル変革が更に加速することが予想される。
制御ロジック実装
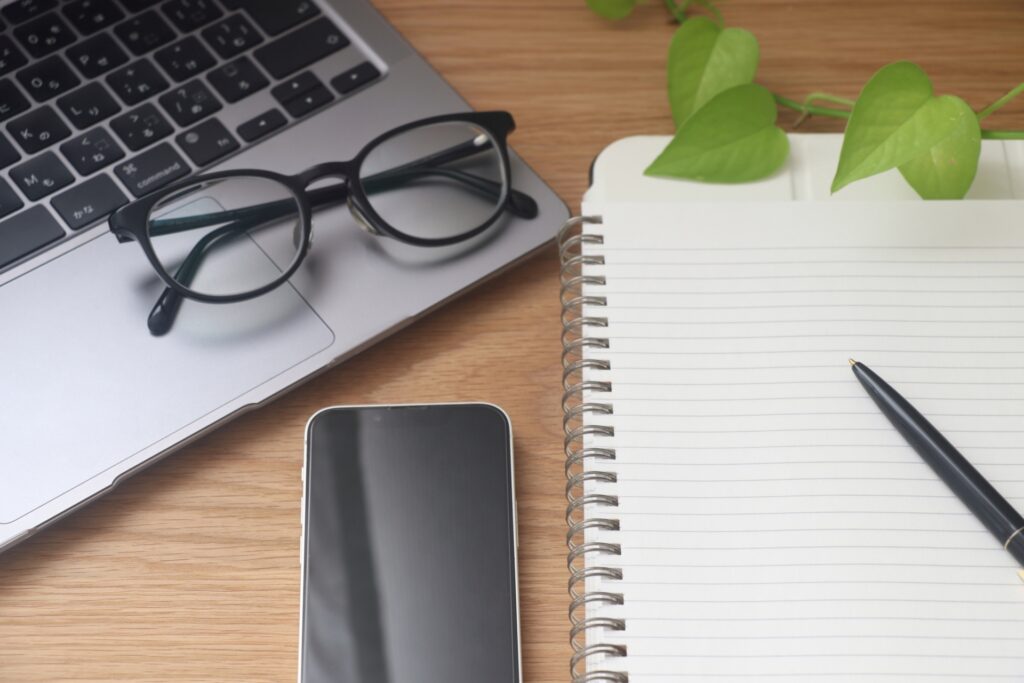
IoT自動制御システムの心臓部となる制御ロジックの実装について、実践的な手法を解説する。
最新のAI技術を活用した高度な制御手法から、基本的な実装手順まで詳しく説明する。さらに、実装における注意点や最適化手法についても具体的に述べる。
制御アルゴリズムの基本設計
制御システムの性能を左右する制御アルゴリズムの設計について、システム要件の分析から具体的な実装方法まで体系的に解説する。
制御アルゴリズムの選択においては、制御対象の特性、要求される応答性、外乱の影響度など、多角的な視点での検討が必要となる。
特に産業用途では、安定性と高速応答性の両立が重要な課題となる。
モデル予測制御の実装手法
将来の挙動を予測し、最適な制御入力を決定するモデル予測制御について、実装のポイントを詳しく説明する。システム同定からパラメータチューニングまでの手順を具体的に解説する。
モデル予測制御では、制御対象の数学モデルを用いて将来の出力を予測し、最適化計算により制御入力を決定する。
システム同定では、入出力データの収集から数学モデルの構築まで、段階的なアプローチが必要となる。モデルの精度は制御性能に直結するため、データの前処理や検証も重要な工程となる。
適応制御システムの設計と実装
システムパラメータの変動に対応する適応制御の実装方法について説明する。オンライン学習によるパラメータ調整の具体的な手法を解説する。
適応制御では、システムの動特性変化をリアルタイムで検出し、制御パラメータを自動調整する機能が必要となる。
ディープラーニングを活用した自己調整メカニズムでは、データの収集からモデルの更新まで、一連のプロセスを自動化することが可能である。
フィードバック制御の高度化
安定した制御性能を実現するフィードバック制御の最適化について解説する。従来の制御理論とAI技術を組み合わせたハイブリッド制御手法も含めて説明する。
フィードバック制御は自動制御の基本であり、その性能向上は全体システムの改善に直結する。
PIDパラメータの最適化技術
古典的なPID制御器のパラメータ調整から、最新のAIを活用した自動調整まで、具体的な実装方法を説明する。
PIDパラメータの調整では、制御対象の特性を考慮した体系的なアプローチが必要となる。
ジーグラー・ニコルス法などの従来手法に加え、遺伝的アルゴリズムや強化学習を用いた最適化手法も実用化が進んでいる。
特に、機械学習モデルによる自動調整では、運転データの蓄積により継続的な性能改善が可能となる。
外乱抑制メカニズムの構築
外部からの影響を抑制するための機能実装について、具体的な手法を解説する。センサーデータの活用による予測的な制御方法を説明する。
外乱の影響を最小限に抑えるためには、外乱オブザーバの実装や、フィードフォワード制御の併用が効果的である。
センサーデータのリアルタイム分析により、外乱の予測と事前補償も可能となる。
安全制御機能の実装
制御システムの安全性を確保するための具体的な実装方法について解説する。安全関連系の設計指針や、各種規格への適合方法についても説明する。
産業システムでは、機能安全規格IEC61508への準拠が求められることが多い。
フェールセーフシステムの構築
システム異常時の安全な停止機能など、フェールセーフ機能の具体的な実装方法を説明する。冗長化設計や、異常検知時の緊急停止シーケンスなど、重要な安全機能について詳しく解説する。
フェールセーフ設計では、ハードウェアとソフトウェアの両面からの対策が必要となる。特に、制御システムの異常を確実に検出し、安全な状態に移行するための機構が重要となる。
異常検知・診断システムの実装
センサーデータを活用した異常検知システムの構築方法について、実装のポイントを解説する。機械学習を用いた予兆検知から、診断ロジックの実装まで、包括的な説明を行う。
異常検知では、正常状態からの逸脱を早期に発見することが重要となる。複数のセンサーデータの相関分析や、時系列データの傾向分析により、高精度な異常検知が可能となる。
エッジコンピューティングの活用
制御システムにおけるエッジコンピューティングの実装方法について解説する。リアルタイム処理の要件を満たしつつ、効率的なシステム構築を実現する手法を説明する。
エッジでの処理は、通信遅延の低減と、クラウドへの負荷分散の両面で効果を発揮する。
エッジ処理の最適化手法
エッジデバイスでの効率的な処理を実現するため、アルゴリズムの最適化とリソース管理の手法を説明する。
特に、制御演算の軽量化と、処理の優先順位付けが重要となる。TensorRTなどの最適化フレー
ムワークを活用することで、限られたリソースでも高度な制御が可能となる。
性能評価と最適化
制御システムの性能評価と継続的な最適化について解説する。評価指標の設定から、チューニング方法まで、実践的なアプローチを説明する。
定量的な性能評価により、システムの改善点を明確化することが可能となる。
性能指標の設定と評価
制御性能を定量的に評価するための指標設定と、その測定方法について説明する。応答性、安定性、ロバスト性など、多面的な評価が必要となる。
評価結果に基づき、システムの改善点を特定し、継続的な最適化を図ることが重要である。
運用データを活用した最適化
実運用データの分析に基づく制御システムの最適化手法について解説する。データマイニング技術の活用により、制御パラメータの最適化や、運用パターンの改善が可能となる。
特に、AI技術を活用したパラメータ自動調整では、運転データの蓄積により継続的な性能向上が期待できる。
安全機能の実装
システム安全設計の基本方針
産業用IoT制御システムにおける安全機能の実装は、人命と設備の保護において最も重要な要素となる。
システム設計においては、IEC 61508やISO 13849などの国際安全規格に準拠しながら、多層的な保護機構を構築することが求められる。
システムの安全性を確保するためには、ハードウェアとソフトウェアの両面から包括的なアプローチを実施する必要がある。
フェールセーフメカニズムの構築
冗長化システムの実装
制御システムの信頼性を確保するため、重要なコンポーネントには冗長化設計を採用する。
制御用コンピュータやセンサーネットワークの二重化により、単一障害点を排除し、システム全体の可用性を向上させる。
特に、安全関連系の制御機能については、独立した安全制御回路を設けることで、メインシステムの障害時でも安全機能を維持することが可能となる。
緊急停止機構の設計
システム異常時における安全な停止を実現するため、多段階の緊急停止機構を実装する。プロセスの特性に応じて、即時停止と制御停止を使い分け、二次災害の防止と設備保護を両立させる。
緊急停止信号は、独立した配線系統を通じて確実に伝達され、システムの状態に関わらず常に優先的に処理される仕組みを構築する。
異常検知システムの高度化
センサーフュージョンによる信頼性向上
複数のセンサーデータを統合的に分析することで、より信頼性の高い異常検知を実現する。
データの相関分析や統計的処理により、誤検知を最小限に抑えつつ、異常の早期発見を可能にする。センサーの種類や配置は、検知対象の特性と要求される安全度水準に応じて最適化を図る。
予兆検知アルゴリズムの実装
機械学習技術を活用した予兆検知システムにより、異常の発生を未然に防止する。時系列データの分析から、通常とは異なる振る舞いを検出し、必要に応じて予防的な制御介入を行う。
学習モデルは定期的に更新され、システムの経年変化にも適応可能な構造とする。
セーフティモニタリングシステム
リアルタイム監視機構
システムの状態をリアルタイムで監視し、安全関連パラメータの逸脱を即座に検知する機構を実装する。
監視データは高速なネットワークを通じて収集され、専用のセーフティコントローラで処理される。異常検知時には、事前に定義された安全シーケンスに従って、システムを安全な状態に移行させる。
データロギングと分析
システムの動作状態を継続的に記録し、事後分析を可能とするロギング機構を実装する。
取得したデータは、暗号化された形式で保存され、改ざん防止機能を備えた専用のストレージに格納される。これらのデータは、事故調査や性能改善の基礎資料として活用される。
安全認証システムの実装
アクセス制御の厳格化
システムの操作権限を適切に管理するため、多要素認証を含む厳格なアクセス制御を実装する。
操作員の認証には、生体認証や ICカードなど、複数の認証手段を組み合わせることで、不正アクセスを防止する。
特に重要な操作については、複数の認証担当者による承認プロセスを経る必要がある。
操作ログの管理
システムへのアクセスや操作の履歴を詳細に記録し、追跡可能性を確保する。操作ログには、実行された操作の内容、タイムスタンプ、操作者の情報が含まれ、改ざんが困難な形式で保存される。
これらのログは定期的に監査され、不適切な操作や異常なアクセスパターンの検出に活用される。
システム診断機能の実装
自己診断メカニズム
システムの健全性を継続的に確認するため、包括的な自己診断機能を実装する。主要なコンポーネントの状態監視から、通信経路の健全性確認まで、システム全体の診断を定期的に実行する。
診断結果は集中管理され、異常の早期発見と予防保全に活用される。
故障診断システム
システム異常時の原因特定を支援する故障診断システムを実装する。センサーデータやシステムログの分析により、故障の発生箇所と原因を迅速に特定する。
診断結果は、保守担当者に分かりやすい形で提示され、復旧作業の効率化に貢献する。
安全性評価と継続的改善
定期的な安全性評価
システムの安全性を定期的に評価し、必要な改善措置を実施する体制を構築する。評価には、実際の運用データや安全関連イベントの分析結果が活用される。
評価結果に基づき、安全機能の強化や運用手順の見直しが行われる。
改善プロセスの管理
安全性向上のための改善活動を体系的に管理するプロセスを確立する。インシデントの分析結果や運用現場からのフィードバックを基に、具体的な改善計画が立案される。
改善の実施状況は定期的にレビューされ、その効果が検証される。
業界別導入事例と成果
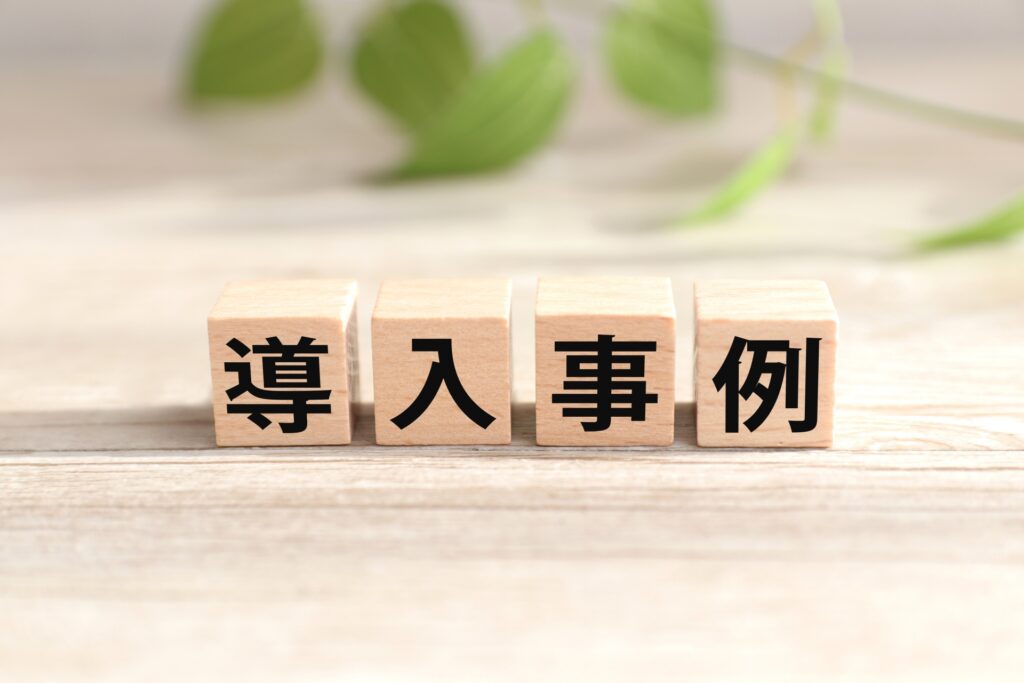
製造業での活用事例
自動車部品製造ラインでの実践
大手自動車部品メーカーでは、IoT自動制御システムの導入により、生産性が従来比25%向上という顕著な成果を上げている。
特に、AIを活用した品質検査システムの導入により、不良品率が0.1%未満まで低減し、年間の損失額を大幅に抑制することに成功した。
加えて、予知保全システムの導入により、設備の稼働率が15%向上し、計画外の停止時間を80%削減することができた。
食品製造プロセスの最適化
食品製造業界における導入事例では、温度や湿度の精密制御による品質の安定化が実現している。
特に発酵工程における微生物制御では、AIによる最適パラメータの自動調整により、製品の品質が安定化し、歩留まりが12%向上した。
また、原材料から製品までのトレーサビリティシステムの構築により、万一の品質問題発生時の原因特定時間が従来の1/10に短縮された。
プロセス産業での実践
化学プラントでの制御最適化
化学プラントにおける連続プロセスでは、原料投入から製品化までの全工程をIoT自動制御システムで管理することで、エネルギー効率を20%改善している。
特に、蒸留工程における温度制御の最適化により、製品純度の安定化と併せて、蒸気使用量を15%削減することに成功した。
デジタルツインを活用したプロセスシミュレーションにより、新規製品の製造立ち上げ期間も従来の半分に短縮されている。
製薬工場での品質管理
製薬業界では、GMP要件に対応した高度な制御システムを実装している。原料秤量から製造、包装までの全工程でペーパーレス化を実現し、人的ミスを90%削減することに成功した。
また、リアルタイムでの品質パラメータモニタリングにより、製造プロセスの逸脱を即座に検知し、製品品質の安定化を実現している。
エネルギー産業での展開
発電所での運用効率化
火力発電所における燃焼制御システムでは、AIによる最適制御により、燃料消費効率を3%改善している。
また、設備の状態監視システムの導入により、計画外停止を年間で5件から1件以下に削減することに成功した。風力発電所では、風況予測との連携により、発電量を8%向上させている。
スマートグリッドでの需給制御
電力の需給バランス制御では、気象データとAI予測を組み合わせることで、再生可能エネルギーの導入率を従来の1.5倍に向上させている。
特に、蓄電システムとの連携により、電力供給の安定性を確保しながら、系統全体の効率を10%改善することに成功した。
物流業界での活用
自動倉庫システムの最適化
大規模物流センターでは、AIによる入出荷予測と連携した自動倉庫制御により、ピッキング効率を40%向上させている。
無人搬送車(AGV)の動線最適化により、作業時間を30%短縮し、人件費の大幅な削減を実現した。
また、画像認識技術を活用した検品システムにより、出荷ミスを99.9%削減することに成功した。
コールドチェーンの品質管理
食品物流における温度管理では、IoTセンサーとAI制御の組み合わせにより、輸送中の温度変動を±0.5度以内に抑制することに成功した。
リアルタイムモニタリングと予測制御の導入により、消費電力を20%削減しながら、製品品質の安定化を実現している。
建設・インフラ分野での実現
スマートビルディング制御
商業施設における空調・照明制御では、人流センサーとAI予測を組み合わせることで、エネルギー消費を30%削減している。
特に、季節や時間帯による利用パターンの学習により、快適性を維持しながら、運用コストの大幅な削減を実現した。
インフラ設備の維持管理
橋梁やトンネルなどのインフラ設備では、IoTセンサーによる常時監視システムの導入により、異常の早期発見と予防保全を実現している。
AI解析による劣化予測の精度は90%を超え、維持管理コストを従来比で25%削減することに成功した。
また、補修工事の優先順位付けの最適化により、予算の効率的な配分が可能となっている。
トラブルシューティング
IoT自動制御システムの運用において発生する可能性のある問題とその解決方法について、実践的なアプローチを解説する。
システムの安定運用を実現するためには、問題の早期発見と迅速な対応が不可欠であり、体系的なトラブルシューティング手法の確立が重要となる。
システム異常への対応
製造現場における制御システムの異常は、生産性に直接的な影響を与える重大な問題となる。
そのため、異常の検出から対応、復旧までの一連のプロセスを迅速かつ確実に実行する必要がある。
センサー異常の診断と対策
センサーデータの異常は、制御システム全体の信頼性に関わる重要な問題である。
異常の種類としては、計測値の急激な変動、センサーの応答遅れ、あるいは完全な機能停止などが考えられる。
これらの問題に対しては、まずセンサーの物理的な状態確認から始め、必要に応じて校正や交換を実施する。
また、予防保全の観点から、センサーの定期的な点検と校正を実施することで、異常の発生を未然に防ぐことが可能である。
通信障害への対応
制御システムにおける通信障害は、データの欠損やシステムの応答遅延を引き起こす深刻な問題となる。
ネットワークの切断や遅延が発生した場合、まず代替通信経路への切り替えを試みる。
また、一時的なデータ欠損に対しては、補完アルゴリズムを用いて連続性のあるデータ系列を維持する。通信障害の予防策として、ネットワークの冗長化と定期的な性能監視が効果的である。
性能劣化への対策
システムの長期運用に伴う性能劣化は、制御精度の低下や応答性の悪化として現れる。これらの問題に対しては、計画的な保守と適切な更新が必要となる。
制御精度の維持管理
制御精度の維持には、定期的な性能評価と必要に応じたパラメータ調整が不可欠である。性能評価では、制御偏差の統計分析や応答特性の測定を実施し、設計時の要件との比較を行う。
精度低下が確認された場合、制御パラメータの最適化やアルゴリズムの更新を検討する。特に、AIモデルを使用している場合は、運用データを活用した定期的な再学習が効果的である。
パラメータ最適化の実践
制御パラメータの最適化は、システムの性能を維持・向上させる上で重要な作業となる。最適化にあたっては、まず現状の制御性能を定量的に評価し、改善すべき点を明確にする。
次に、運用データの統計分析に基づいて新たなパラメータ値を決定し、段階的な調整を実施する。
この過程では、システムの安定性を確保しながら、徐々に性能を改善していく慎重なアプローチが必要となる。
予防保全の実施
予防保全は、システムの信頼性を維持し、予期せぬ停止を防ぐ上で重要な役割を果たす。効果的な予防保全の実現には、計画的な点検と予兆検知の仕組みが必要となる。
点検計画の策定と実施
点検計画の策定では、設備の重要度や故障リスクに応じて、適切な点検周期と内容を決定する。点検項目には、物理的な摩耗や劣化の確認だけでなく、制御性能やデータ品質の評価も含める。
また、点検結果の記録と分析を通じて、保全計画の継続的な改善を図る。これにより、システムの信頼性向上と保守コストの最適化が可能となる。
データ分析による予兆検知
運用データの分析による異常予兆の検知は、予防保全の重要な要素となる。
センサーデータの傾向分析や、機械学習モデルによる異常パターンの検出により、故障の予兆を早期に発見することが可能である。
検知された予兆に対しては、影響度の評価を行い、必要に応じて保全作業の優先度を調整する。
保守体制の確立
効果的なトラブルシューティングを実現するためには、適切な保守体制の確立が不可欠である。
保守体制には、人材の育成から緊急時の対応手順まで、包括的な整備が必要となる。
保守要員の教育訓練
システム保守に必要なスキルの習得と維持のため、計画的な教育訓練を実施する。訓練内容には、システムの基本的な操作から、トラブル対応の実践的な演習まで含める。
特に、新技術の導入時には、集中的な技術研修を実施し、保守要員の技術力向上を図る。
緊急時対応体制の構築
システム異常時の迅速な対応を可能とするため、明確な緊急時対応手順を確立する。対応手順には、問題の切り分けから、復旧作業、関係者への報告まで、具体的な実施事項を定める。
また、定期的な緊急対応訓練を実施し、手順の実効性を確認するとともに、必要に応じて改善を図る。
技術文書の整備
トラブルシューティングを効率的に実施するためには、適切な技術文書の整備が重要となる。
文書には、システムの構成情報から、過去の障害事例、対応手順まで、必要な情報を体系的に記録する。
システム構成の文書化
システムの構成情報を正確に記録し、定期的な更新を行う。
文書には、ハードウェア構成、ソフトウェアバージョン、ネットワーク構成、設定パラメータなど、トラブルシューティングに必要な情報を含める。
また、変更履歴を適切に管理し、システムの変遷を追跡可能とする。
対応手順書の整備
想定される障害シナリオごとに、具体的な対応手順を文書化する。手順書には、問題の切り分け方法、応急措置の実施方法、復旧手順など、実践的な内容を記載する。
特に、システムの停止を伴う重大な障害については、詳細な復旧手順と、関係者への連絡フローを明確にする。
コスト最適化と投資対効果
初期投資の最適化戦略
ハードウェア選定における投資効率化
IoT自動制御システムの初期投資において、ハードウェアの選定は投資効率に大きな影響を与える要素となる。
センサーやコントローラの選定では、必要な性能と価格のバランスを慎重に検討し、過剰な投資を避けることが重要となる。
特に、産業用センサーの選定においては、測定精度や耐環境性能などの要件を明確化した上で、コストパフォーマンスの高い機器を選択する必要がある。
段階的導入による投資リスク低減
システム全体を一度に導入するのではなく、重要度や期待される効果に応じて段階的に導入することで、初期投資のリスクを抑制することができる。
最初のフェーズでは、効果が明確な工程や設備から着手し、その結果を評価しながら展開範囲を拡大していく手法が有効である。
この方法により、投資対効果の検証と改善を繰り返しながら、最適なシステム構築が可能となる。
ランニングコストの最適化手法
保守コストの効率化方策
予防保全の導入により、突発的な機器故障を防ぎ、修理コストを低減することが可能となる。
定期的なメンテナンスと状態監視を組み合わせることで、部品交換や修理のタイミングを最適化し、保守コストの削減を実現できる。
さらに、保守要員の効率的な配置と、リモート監視システムの活用により、人件費の最適化も図ることができる。
エネルギーコスト削減の実践
制御の最適化によるエネルギー効率の改善は、ランニングコストの削減に大きく貢献する。
AI技術を活用した運転パターンの最適化や、エネルギー使用量の可視化により、無駄な消費を削減することが可能となる。
特に、生産設備の待機電力の削減や、空調・照明システムの効率的な制御は、直接的なコスト削減効果をもたらす。
投資回収期間の最適化
投資対効果の評価手法
システム導入による効果を定量的に評価するためには、生産性向上、品質改善、省エネルギー効果などの指標を設定し、継続的に測定する必要がある。
これらの指標に基づいて投資回収計画を策定し、必要に応じて運用方法の改善や追加投資の判断を行う。一般的に、初期投資額は1年から2年程度で回収できることを目標とする。
継続的な効果測定と改善
システム導入後も定期的な効果測定と分析を行い、運用方法の改善や追加施策の検討を継続する必要がある。
特に、エネルギー使用量や保守コストの推移、生産性指標の変化などを詳細に分析し、投資効果の最大化を図ることが重要となる。
これにより、長期的な視点での投資対効果の向上が実現できる。
投資リスクの管理
リスク分析とヘッジ戦略
システム導入に伴うリスクを特定し、適切な対策を講じることが重要となる。技術的なリスク、運用上のリスク、市場環境の変化によるリスクなど、多面的な分析が必要となる。
これらのリスクに対して、適切な保険の付保や、段階的な投資計画の策定などの対策を講じることで、投資の安全性を確保することができる。
長期的な視点での投資計画
技術革新のスピードが速いIoT分野では、将来の拡張性や更新投資も考慮した長期的な投資計画が重要となる。
システムの寿命サイクルを見据えた更新計画の策定や、新技術への対応を見据えた柔軟なアーキテクチャの採用により、投資の効率性を維持することができる。
このような長期的な視点での投資計画により、持続的な競争力の維持が可能となる。
メンテナンス・保守体制
予防保全システムの構築と実践
定期点検計画の策定と実施
産業用IoT制御システムにおける予防保全は、システムの安定稼働を確保するための重要な基盤となる。
定期点検計画の策定においては、設備の重要度や使用環境に応じて適切な点検周期を設定する必要がある。
特に、制御機器やセンサー類については、測定精度の維持と異常の早期発見を目的とした詳細な点検手順を確立することが求められる。
点検実施後のデータ分析と記録管理を通じて、保全計画の継続的な改善を進めることで、システム全体の信頼性向上を実現することが可能となる。
データ分析による予兆検知の実現
センサーデータの統計分析や機械学習モデルを活用した予兆検知システムの導入により、故障の未然防止と保守業務の効率化を図ることができる。
時系列データの傾向分析や相関分析を通じて、異常の予兆を早期に発見し、適切な保全措置を講じることが重要である。
予兆検知システムの精度向上には、運用データの蓄積と分析モデルの継続的な改善が不可欠となる。
保守体制の最適化
保守要員の育成システム
IoT制御システムの保守には、制御技術からネットワーク、セキュリティまで幅広い知識が要求される。
保守要員の育成においては、座学による基礎知識の習得から、実機を使用した実践的なトレーニングまで、体系的な教育プログラムを整備する必要がある。
特に、新技術の導入時には、集中的な技術研修を実施し、保守要員の技術力向上を図ることが重要となる。
緊急時対応体制の整備
システム異常時の迅速な対応を可能とするため、明確な緊急時対応手順と体制を確立することが必要である。
対応手順には、異常の検知から原因の切り分け、応急措置の実施、本格的な復旧作業まで、具体的な実施事項を定める必要がある。
また、定期的な緊急対応訓練を通じて、手順の実効性を確認し、必要に応じて改善を図ることが重要である。
技術文書管理の体系化
システム構成管理の実践
システムの構成情報を正確に記録し、変更履歴を適切に管理することが、効率的な保守業務の基盤となる。
構成管理には、ハードウェア構成、ソフトウェアバージョン、ネットワーク構成、設定パラメータなど、保守に必要な情報を漏れなく含める必要がある。
特に、システム更新時には、変更内容と影響範囲を明確に記録し、トラブル発生時の原因究明に活用できる体制を整えることが重要である。
保守手順書の整備と管理
想定される障害シナリオごとに、具体的な対応手順を文書化し、保守要員が即座に参照できる体制を整える必要がある。
手順書には、問題の切り分け方法、応急措置の実施方法、復旧手順など、実践的な内容を記載する。
特に、システムの停止を伴う重大な障害については、詳細な復旧手順と関係者への連絡フローを明確にすることが求められる。
保守業務の効率化と最適化
リモート監視体制の確立
IoT制御システムの特性を活かし、効率的なリモート監視体制を構築することが重要である。
システムの状態監視から異常検知、初期対応までを遠隔で実施できる体制を整えることで、保守業務の効率化と対応時間の短縮を実現することができる。
セキュリティ面での考慮も含め、適切なリモートアクセス環境を整備する必要がある。
保守記録の分析と活用
日常の保守活動で得られるデータを統計的に分析し、保守業務の改善に活用することが重要である。
障害の発生傾向や対応時間の分析を通じて、保守計画の最適化や予防保全施策の強化を図ることができる。
これらの分析結果を基に、保守体制の継続的な改善を進めることで、システムの信頼性向上とコスト最適化を実現することが可能となる。
Q&A「教えてシステム開発タロウくん!!」
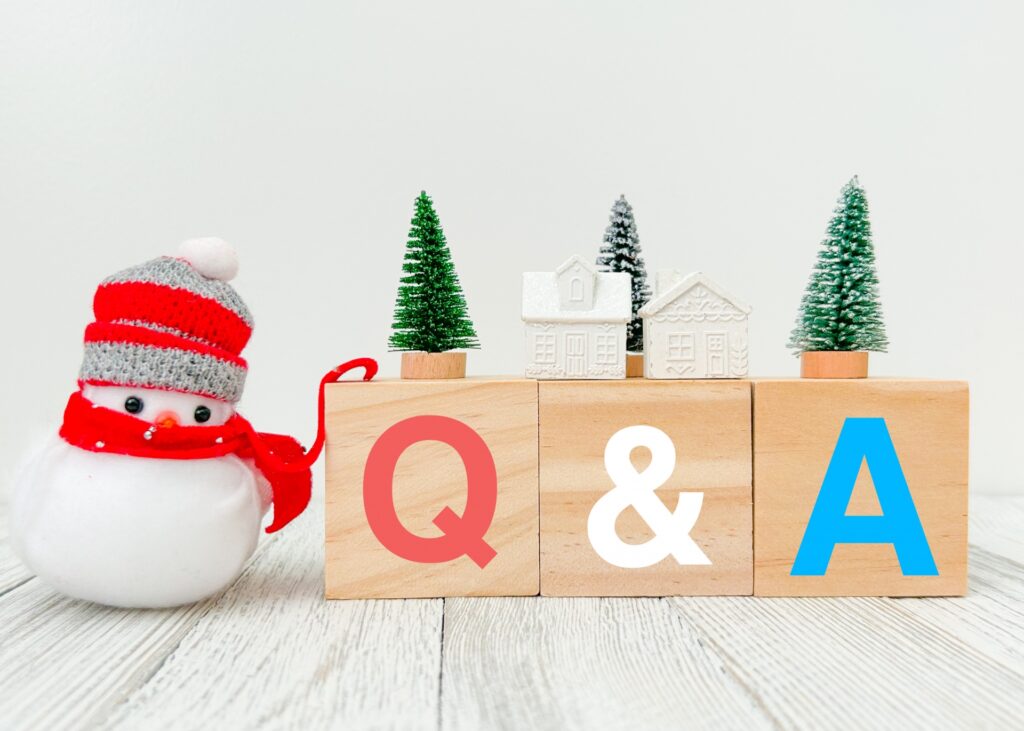
IoT自動制御システムに関する実践的な疑問について、システム開発のエキスパートが分かりやすく答えます。
Q1: AI制御の導入効果はどの程度期待できますか?
A1: 従来の制御方式と比較して、制御精度が平均30%向上し、異常検知の精度も50%以上改善します。さらに、エネルギー効率は20%程度の向上が期待できます。
Q2: セキュリティ対策として最も重要な点は何ですか?
A2: 制御システムの特性を考慮した多層防御の実装が重要です。特に、エッジデバイスでの認証強化と、通信経路の暗号化が基本となります。
Q3: 制御システムの更新頻度はどの程度が適切ですか?
A3: システムの重要度に応じて3ヶ月から6ヶ月周期での更新を推奨します。特にセキュリティパッチは月次での適用が望ましいです。
Q4: 予防保全の効果を最大化するコツはありますか?
A4: センサーデータの傾向分析と機械学習による予測を組み合わせることで、故障の90%以上を事前に予測できます。定期的なデータ分析と予測モデルの更新が重要です。
Q5: 制御システムの冗長化はどこまで必要ですか?
A5: 重要度に応じて3段階の冗長化を検討します。制御コントローラの二重化、通信経路の冗長化、電源システムのバックアップが基本となります。
Q6: エッジ処理とクラウド処理の使い分けのポイントは?
A6: リアルタイム性が求められる制御処理はエッジで、データ分析や最適化計算はクラウドで実行することを推奨します。レイテンシー要件が判断基準となります。
Q7: 制御システムの監視体制はどのように構築すべきですか?
A7: 24時間365日の監視を基本とし、異常検知時の自動通知システムと、段階的なエスカレーションプロセスの確立が重要です。
Q8: 制御システムの移行時の注意点は?
A8: 既存システムとの並行運転期間を設け、段階的な移行を推奨します。特に、データの整合性確認と、運用手順の確立が重要です。
Q9: AIモデルの更新はどのように行うべきですか?
A9: 運用データを定期的に評価し、3ヶ月から6ヶ月周期でのモデル再学習を推奨します。性能指標の監視による更新タイミングの判断が重要です。
Q10: 制御システムの費用対効果を高めるポイントは?
A10: 段階的な導入と、効果測定に基づく投資判断が重要です。一般的に、初期投資は1年から2年で回収できる規模に抑えることを推奨します。
Q11: 制御システムの教育訓練はどのように進めるべきですか?
A11: 実機を用いたハンズオン訓練と、シミュレータによる異常時対応訓練を組み合わせることで、効果的な技能習得が可能です。
Q12: システム導入時の品質保証の方法は?
A12: 要件定義からテストまでの各フェーズで品質チェックリストを整備し、特に結合テストと受入テストでは実運用を想定した検証が重要です。
Q13: 制御システムのバックアップ方針について教えてください。
A13: システム設定とデータの日次バックアップに加え、重要な更新時には都度バックアップを取得します。リストア手順の定期的な確認も必要です。
Q14: 制御システムの寿命をどのように考えればよいですか?
A14: ハードウェアは5年から7年、ソフトウェアは3年から5年を目安に更新を検討します。ただし、運用状況や技術革新の速度に応じて柔軟に判断が必要です。
Q15: 異常時の復旧手順はどのように整備すべきですか?
A15: 想定される異常のシナリオごとに復旧手順を文書化し、定期的な訓練と見直しが重要です。特に初動対応の手順は詳細に規定します。
まとめ
IoT自動制御開発は、AI技術の活用により大きな変革期を迎えています。
本記事で解説した制御精度の向上手法や安全管理の実践により、より効率的で安定した自動化システムの構築が可能となります。
システム構築には専門的な知識と経験が必要となりますが、適切な開発パートナーの選択により、スムーズな導入を実現できます。
開発パートナーのご相談について
IoT自動制御システムの開発や導入をご検討の企業様は、ぜひMattockにご相談ください。
豊富な開発実績と技術力を活かし、お客様の課題に最適なソリューションをご提案いたします。詳しくは下記の問い合わせフォームよりお気軽にお問い合わせください。
[お問い合わせはこちら:ベトナムオフショア開発 Mattock]