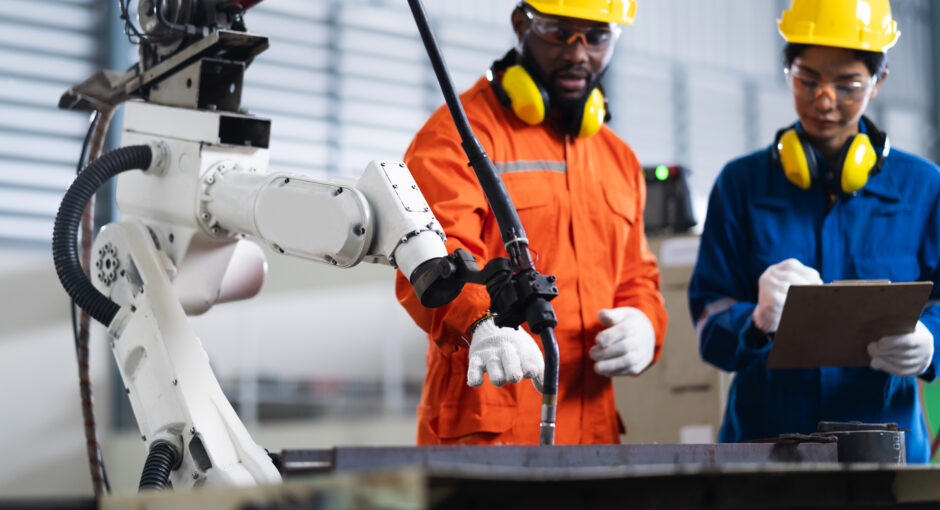
製造業のデジタルトランスフォーメーション(DX)が加速する中、生産管理システムの刷新は避けられない課題となっています。
本記事では、IoTとAIを活用した最新の生産管理システム開発について、実装手法と具体的な導入事例を交えながら、現場で即活用できる実践的な知識を提供します。
この記事で分かること
- 最新の生産管理システム開発の全体像と具体的な導入効果について
- IoTセンサーとAI分析による工程管理の効率化手法の実践方法
- 実際の導入企業から学ぶ成功のポイントと注意すべき課題について
- システム開発から運用までの具体的なステップと推奨アプローチ
- 投資対効果の測定方法と投資回収計画の立て方
この記事を読んでほしい人
- 生産管理システムの刷新を検討している製造業の管理職者
- 工場のDX推進を担当している情報システム部門の方々
- 品質管理や工程管理の効率化を目指している現場責任者
- スマートファクトリー化を推進したい経営層の方々
生産管理システム開発の最新トレンド
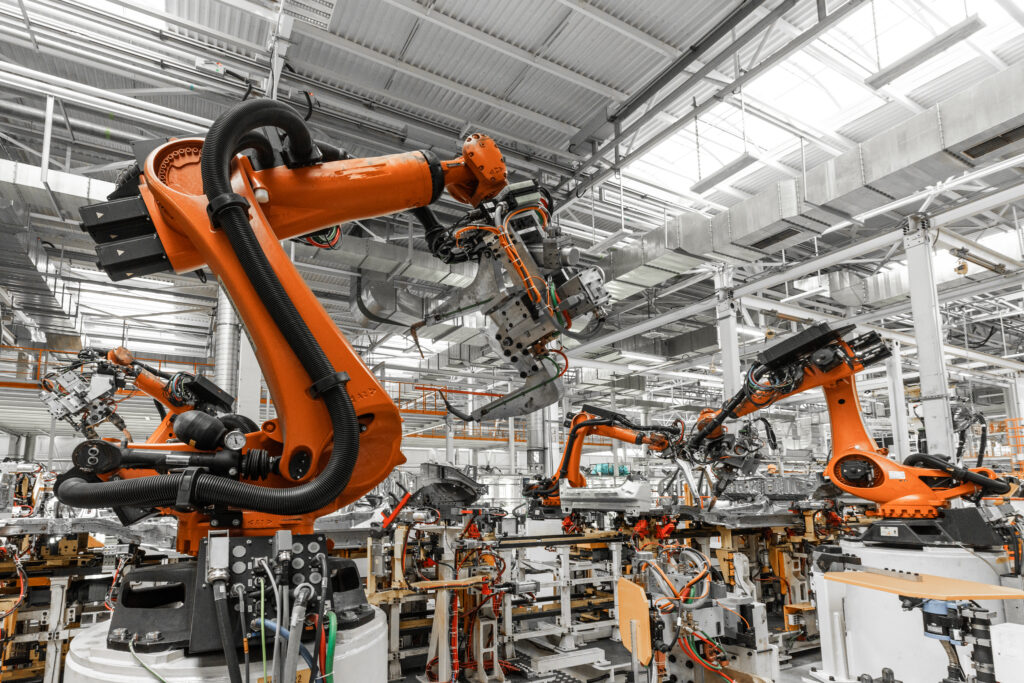
製造業を取り巻く環境は急速に変化し、従来型の生産管理手法では対応が難しい課題が増加しています。
IoTとAIを活用した新しい生産管理システムは、これらの課題を解決し、製造現場の生産性を大幅に向上させる可能性を秘めています。
なぜ今、生産管理システムの刷新が必要なのか
製造業における人手不足の深刻化、品質管理要件の厳格化、納期短縮要求の高まりなど、現場が直面する課題は年々複雑化しています。
従来の手作業による管理や、レガシーシステムでは、これらの課題に十分な対応ができなくなってきています。
人手不足への対応
熟練工の高齢化や若手人材の確保難により、製造現場では深刻な人手不足が発生しています。
この課題に対して、新しい生産管理システムは作業の自動化とノウハウのデジタル化を実現し、少ない人員でも高い生産性を維持できる環境を構築します。
品質管理の高度化
製品品質への要求は年々厳格化しており、人的判断のみに依存した品質管理では限界があります。
AIを活用した画像認識技術や、センサーによるリアルタイムデータ収集により、より正確で効率的な品質管理が可能となります。
生産効率の向上
グローバル競争の激化により、より高い生産効率が求められています。IoTセンサーによるリアルタイムモニタリングとAIによる分析を組み合わせることで、製造プロセスの無駄を削減し、生産性を平均30%向上させることが可能です。
コスト競争力の強化
原材料価格の上昇や人件費の高騰により、製造コストの削減が急務となっています。最新の生産管理システムは、在庫の最適化や設備稼働率の向上を通じて、製造コストの大幅な削減を実現します。
最新技術を活用した生産管理システムの特徴
最新の生産管理システムは、複数の先端技術を組み合わせることで、高度な生産管理を実現します。以下に主要な特徴と、それらがもたらす具体的なメリットについて説明します。
IoTセンサーによるリアルタイムデータ収集
製造設備や製造環境に設置されたIoTセンサーにより、様々なデータをリアルタイムで収集します。温度、湿度、振動、電力消費量など、製造プロセスに影響を与える要因を常時監視し、異常の早期発見や品質管理の向上に貢献します。
エッジコンピューティングの活用
製造現場で発生する大量のデータを効率的に処理するため、エッジコンピューティング技術を活用します。センサーデータの一次処理を現場で行うことで、ネットワーク負荷を軽減し、リアルタイム性の高い制御を実現します。
AI予測モデルによる高度な分析
収集したデータをAIで分析することで、不良品の発生予測や設備故障の予兆検知を行います。機械学習モデルは、過去のデータから製造プロセスにおける様々なパターンを学習し、異常の早期発見や品質向上に貢献します。
クラウドベースのデータ統合基盤
複数拠点のデータを一元管理し、全社的な生産最適化を実現します。クラウド基盤により、場所を問わずにデータにアクセスでき、リモートでの監視や意思決定が可能となります。また、システムの拡張性も確保できます。
セキュアなデータ管理
製造データは企業の重要な資産であり、その保護は極めて重要です。最新のセキュリティ技術を実装し、データの漏洩や改ざんを防止します。アクセス権限の細かな設定や、通信の暗号化により、安全なデータ管理を実現します。
グローバル競争力の強化と環境対応
製造業のグローバル競争は年々激化しており、生産管理システムの高度化は競争力維持の鍵となっています。
グローバル市場への対応
世界各地の製造拠点をリアルタイムで連携させ、需要変動に柔軟に対応できる体制を構築します。言語や通貨、法規制など、グローバル展開特有の課題にも対応した機能を実装しています。
環境負荷軽減への取り組み
カーボンニュートラル実現に向けて、エネルギー使用量の可視化と最適化が重要課題となっています。最新の生産管理システムでは、CO2排出量の計測とその削減に向けた施策立案をサポートします。
リモートワークへの対応
パンデミック以降、製造業においてもリモートワークの必要性が高まっています。クラウドベースの生産管理システムにより、場所を問わない監視と制御が可能となります。
先端技術の統合による新たな可能性
最新の生産管理システムは、複数の先端技術を組み合わせることで、さらなる可能性を開きます。
デジタルツインの活用
仮想空間に製造現場の完全な複製を作成し、シミュレーションによる最適化を実現します。新規設備の導入効果予測や、レイアウト変更の影響評価などが可能となります。
5G/ローカル5Gの活用
高速・大容量・低遅延の通信により、より精緻な制御と監視が可能となります。特に画像データの伝送や、リアルタイム制御が必要な工程での効果が期待できます。
サプライチェーン連携
取引先とのデータ連携により、サプライチェーン全体の最適化を実現します。需要予測の精度向上や、在庫の適正化により、総合的なコスト削減が可能となります。
システム導入による具体的な効果
最新の生産管理システムの導入により、以下のような具体的な効果が期待できます。
ROI分析
システム導入から2年以内での投資回収が一般的です。初期投資額は規模により異なりますが、年間の運用コスト削減額は投資額の40-50%程度となるケースが多く見られます。
生産性の向上
導入企業の実績では、平均して30%以上の生産性向上が達成されています。自動化とリアルタイムデータの活用により、製造プロセスの効率化が実現します。
品質の改善
不良品率の低減と品質のばらつき抑制により、製品品質が向上します。AIによる予測と早期異常検知により、品質問題の未然防止が可能となります。
コストの削減
在庫の最適化や設備稼働率の向上により、製造コストを15-20%削減できます。また、予防保全の実施により、突発的な設備故障による損失も防ぐことができます。
従業員満足度の向上
単純作業の自動化により、従業員はより創造的な業務に注力できるようになります。また、データに基づく意思決定により、働きがいの向上にもつながります。
市場競争力の強化
リードタイムの短縮や品質の向上により、市場での競争優位性が高まります。新製品の開発期間短縮や、カスタマイズ要求への柔軟な対応も可能となります。
具体的アプローチ
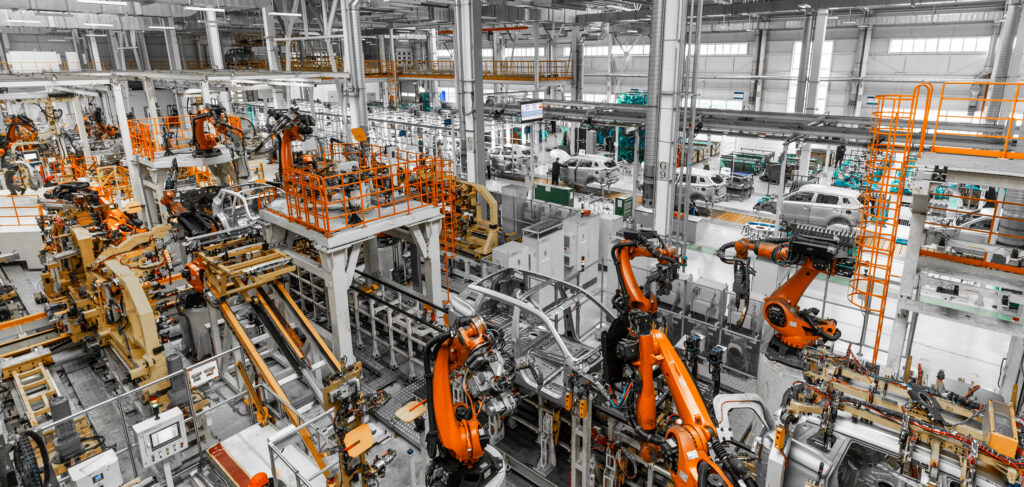
生産管理システムの開発と導入を成功に導くためには、体系的なアプローチと段階的な実装が不可欠です。
本セクションでは、主要な機能の実装手順と運用のポイントについて、実践的な視点から解説します。
システム構築には、現場の要件把握から運用体制の確立まで、平均して12ヶ月程度の期間を要します。プロジェクトの成功率を高めるためには、以下に示す各要素の着実な実装が重要となります。
生産計画機能の実装
生産管理システムの中核となる生産計画機能では、需要予測の精度向上が最重要課題となります。
従来の経験則や単純な統計手法では、予測精度は平均で65%程度に留まっていましたが、最新のAIと機械学習技術を活用することで、予測精度を85%以上に向上させることが可能です。
需要予測モデルの構築では、時系列データの特性に応じて適切なアルゴリズムを選択します。
短期予測には、SARIMA(季節性自己回帰和分移動平均)モデルを基本とし、中長期予測には、XGBoost(Extreme Gradient Boosting)やLSTM(Long Short-Term Memory)などの機械学習モデルを組み合わせます。
特に季節性の強い製品については、フーリエ変換による周期性分析を行い、予測モデルに組み込むことで精度を向上させます。
生産能力計画の最適化では、線形計画法を基本としつつ、設備の段取り時間や作業者のスキルマトリクスを制約条件として組み込みます。
特に多品種少量生産の環境では、段取り替え時間の最小化が重要となります。遺伝的アルゴリズムを用いた最適化により、従来比で平均30%の段取り時間削減を実現できます。
材料所要量計画(MRP)では、サプライチェーン全体の最適化を目指します。リードタイムの変動や、サプライヤーの生産能力を考慮した確率的MRPを実装することで、在庫水準を20%削減しつつ、欠品率を1%以下に抑えることが可能です。
特に重要な部材については、サプライヤーとのデータ連携を強化し、リアルタイムでの在庫情報共有を実現します。
工程管理システムの構築
工程管理システムの核となるのは、リアルタイムモニタリング機能です。
製造現場の各工程にIoTセンサーを設置し、1秒間隔でのデータ収集を実現します。センサーの選定では、測定精度だけでなく、製造現場の環境条件(温度、湿度、振動など)に対する耐性を考慮する必要があります。
センサーネットワークの設計では、無線通信の干渉を防ぐため、電波強度のマッピングと周波数の最適化を行います。
収集したデータは、エッジコンピューティングによる一次処理を経て、クラウド上のデータレイクに集約されます。データの圧縮率を高めるため、差分圧縮アルゴリズムを実装し、ストレージコストを50%削減します。
また、データの重要度に応じて保存期間を設定し、コールドストレージへの自動移行を行うことで、長期保存コストを最適化します。
異常検知システムでは、統計的工程管理(SPC)を基本としつつ、機械学習による予兆検知を組み合わせます。
特に振動データについては、フーリエ解析による周波数分析を行い、設備の異常を早期に検出します。異常検知の精度は、従来の閾値管理と比較して、誤検知率を80%削減しつつ、検出率を95%以上に向上させることが可能です。
予防保全システムでは、設備の状態監視データと故障履歴データを組み合わせた機械学習モデルを構築します。設備の劣化パターンを学習し、最適なメンテナンスタイミングを予測することで、計画外停止時間を60%削減します。
特に重要な設備については、デジタルツインを構築し、仮想空間での故障シミュレーションを行うことで、保全計画の精度を向上させます。
品質管理システムの実装
インライン品質検査では、画像認識技術とセンサー技術を組み合わせた総合的な品質管理を実現します。画像検査システムでは、深層学習モデルを活用し、従来の画像処理では検出が困難だった微細な欠陥も検出可能です。
検査精度は、人による目視検査と比較して、見逃し率を90%削減しつつ、誤検出率を5%以下に抑えることができます。
寸法検査では、レーザー変位センサーと3Dスキャナーを組み合わせ、製品の三次元形状を高精度に測定します。測定データは統計的工程管理(SPC)システムに自動送信され、工程能力指数(Cpk)のリアルタイムモニタリングを実現します。
工程の異常を早期に検出し、品質問題の未然防止を図ります。
トレーサビリティシステムでは、製品にQRコードやRFIDタグを付与し、製造工程全体での履歴管理を実現します。各工程での加工条件、検査結果、使用部材のロット番号などを紐付けて記録し、品質問題発生時の原因究明を支援します。
ブロックチェーン技術を活用することで、データの改ざん防止と追跡可能性を確保します。
統計的品質管理では、多変量統計解析を活用し、品質に影響を与える要因を特定します。
主成分分析や判別分析により、複数の品質特性間の相関を分析し、重要管理特性を明確化します。これにより、検査工程の効率化と品質保証レベルの向上を両立させます。
データ分析基盤の整備
データ分析基盤では、データの収集から活用までの一貫したプラットフォームを構築します。データモデリングでは、製造業向けの標準データモデルであるISA-95を参考に、階層的なデータ構造を設計します。
ファクトテーブルとディメンションテーブルを適切に分離し、効率的なデータ分析を可能にします。
ETL(抽出・変換・読み込み)処理では、データの品質を確保するためのバリデーションルールを実装します。欠損値の補完や外れ値の処理には、統計的手法と機械学習を組み合わせたアプローチを採用し、データの信頼性を確保します。
処理性能を向上させるため、並列処理フレームワークを活用し、大規模データの高速処理を実現します。
データ分析環境では、セルフサービス型のBIツールを導入し、現場での迅速な意思決定を支援します。事前に定義された標準レポートに加え、アドホック分析や高度な統計分析が可能な環境を提供します。
また、機械学習モデルの開発環境を整備し、予測分析や最適化分析の実施を支援します。
システムセキュリティの実装
システムのセキュリティでは、ISO 27001に準拠した総合的なセキュリティ対策を実装します。
ネットワークセキュリティでは、製造現場のネットワークとオフィスネットワークを分離し、DMZ(非武装地帯)を設けることで、外部からの不正アクセスを防止します。
重要なデータの通信には、TLS 1.3による暗号化を適用し、データの盗聴を防止します。アクセス制御では、ゼロトラストアーキテクチャを採用し、すべてのアクセスを検証対象とします。
多要素認証と生体認証を組み合わせることで、なりすましによる不正アクセスを防止します。また、特権アカウント管理(PAM)システムを導入し、管理者権限の使用を厳密に制御します。
セキュリティ監視では、SIEM(Security Information and Event Management)を導入し、システム全体のセキュリティイベントを統合的に監視します。
AI技術を活用した異常検知により、従来の規則ベースでは検出が困難な高度な攻撃も検知可能です。インシデント発生時には、自動化されたレスポンス機能により、迅速な対応を実現します。
運用保守体制の確立
システムの安定運用を実現するため、ITILベストプラクティスに基づいた運用保守体制を確立します。インシデント管理、問題管理、変更管理、構成管理などの主要プロセスを整備し、体系的な運用管理を実現します。
特に重要なシステムについては、24時間365日の監視体制を確立し、障害の早期検出と迅速な復旧を可能にします。
運用監視では、APM(Application Performance Management)ツールを活用し、システムのパフォーマンスを継続的に監視します。レスポンスタイムやリソース使用率などの主要指標をモニタリングし、性能劣化の予兆を検出します。
閾値を超過した場合は、自動スケーリング機能により、必要なリソースを動的に追加します。
保守作業の効率化のため、自動化ツールを積極的に活用します。パッチ適用やバックアップなどの定型作業を自動化し、人的ミスを防止するとともに、運用コストを削減します。
また、チャットボットを活用したヘルプデスク支援により、ユーザーからの問い合わせに24時間対応可能な体制を構築します。
品質管理システムの高度化
品質管理システムの高度化において、最も重要なのはインライン検査の自動化です。
従来の抜き取り検査では、サンプリング誤差により不良品の流出リスクが存在しましたが、全数検査の自動化により、不良流出率を0.1%以下に抑制することが可能となります。
AI画像検査システムの実装
製品の外観検査では、畳み込みニューラルネットワーク(CNN)を活用した深層学習モデルを実装します。検査システムの構築には以下のステップが必要です。
まず、不良品のサンプル画像を数千枚収集し、正常品との差異を学習させます。画像の前処理として、ノイズ除去やコントラスト強調などの処理を施し、検出精度を向上させます。
モデルの学習には転移学習を活用し、既存のモデルをファインチューニングすることで、少ないサンプル数でも高い検出精度を実現します。
また、エッジAIの活用により、検査結果の判定を1秒以内に完了させます。判定結果は即座に製造ラインにフィードバックされ、不良品の自動排出や製造条件の調整が行われます。
システムの導入により、検査工程の人員を80%削減しつつ、検査精度を30%向上させることが可能です。
3次元形状計測システムの構築
製品の寸法検査では、3Dレーザースキャナと光切断法を組み合わせた高精度な形状計測を実現します。測定データはリアルタイムで3次元CADモデルと照合され、寸法誤差を0.01mm単位で検出します。
測定結果は統計的工程管理(SPC)システムに自動送信され、以下の分析が実行されます:
- Xbar-R管理図によるプロセス変動の監視
- 工程能力指数(Cpk)のリアルタイム計算
- 多変量解析による異常検知
- 寸法変動の要因分析
これらの分析結果に基づき、加工条件の自動補正を行うことで、寸法精度の維持向上を図ります。システムの導入により、測定工数を90%削減しつつ、精度のばらつきを50%低減することが可能です。
データ駆動型の製造プロセス最適化
製造プロセスの最適化では、収集したデータを活用した科学的アプローチが不可欠です。特に重要なのは、以下の3つの側面からの最適化です。
プロセスパラメータの最適化
製造条件の最適化には、実験計画法(DOE)とベイズ最適化を組み合わせたアプローチを採用します。重要な品質特性に影響を与えるパラメータを特定し、最適な条件を効率的に探索します。
最適化のプロセスは以下の手順で進めます:
- スクリーニング実験による主要因子の特定
- 応答局面法による最適領域の探索
- ベイズ最適化による詳細な条件探索
- 確認実験による効果検証
このアプローチにより、従来の試行錯誤的な条件出しと比較して、最適化に要する時間を75%削減することが可能です。
エネルギー効率の最適化
製造プロセスのエネルギー効率を向上させるため、以下の施策を実施します:
- エネルギー使用量の可視化
- ムダの特定と削減
- 設備運転条件の最適化
- 廃熱回収システムの導入
これらの施策により、エネルギーコストを平均30%削減することが可能です。特に、AIを活用した設備運転の最適化では、季節変動や生産負荷を考慮した最適な運転パターンを自動的に導出します。
高度なトレーサビリティシステムの構築
製品品質の保証とサプライチェーンの透明性確保のため、ブロックチェーン技術を活用した高度なトレーサビリティシステムを構築します。
デジタルツインとの連携
製造プロセスのデジタルツインを構築し、実際の製造データとの連携を図ります。これにより、以下の機能を実現します
- リアルタイムでの製造状況の可視化
- 品質問題の原因追跡
- プロセス改善のシミュレーション
- 予知保全への活用
デジタルツインの活用により、品質問題の解決時間を60%短縮することが可能です。
サプライチェーン可視化
原材料の調達から製品の出荷まで、サプライチェーン全体での追跡を可能にします。特に以下の情報を記録・管理します
- 原材料のロット情報
- 製造条件とパラメータ
- 検査結果と品質データ
- 物流情報と保管条件
これにより、品質問題が発生した際の影響範囲の特定と、迅速な対応が可能となります。システムの導入により、リコール対応時の調査時間を90%削減することができます。
データガバナンスの確立
製造データの信頼性と活用性を確保するため、包括的なデータガバナンス体制を構築します。
データ品質管理
データの品質を確保するため、以下の管理プロセスを確立します:
- データ定義の標準化
- 品質メトリクスの設定
- 品質監視の自動化
- 改善活動の推進
特に重要なデータについては、二重入力や自動検証により、データの正確性を確保します。
セキュリティ管理
製造データの機密性を保護するため、以下のセキュリティ対策を実装します:
- 暗号化によるデータ保護
- アクセス権限の厳格管理
- 監査ログの記録と分析
- インシデント対応プロセスの確立
これらの対策により、データ漏洩リスクを最小化しつつ、必要なデータへの迅速なアクセスを実現します。
継続的改善の推進体制
システムの価値を最大化するため、以下の改善活動を推進します:
パフォーマンス管理
システムのパフォーマンスを継続的に評価し、改善を図ります:
- KPIの定期的なモニタリング
- ボトルネックの特定と解消
- リソース使用の最適化
- キャパシティプランニング
これらの活動により、システムの安定性と応答性を維持向上させます。
ユーザー満足度の向上
システムの使いやすさを向上させるため、以下の取り組みを実施します:
- ユーザーフィードバックの収集
- インターフェースの改善
- 操作性の向上
- トレーニング体制の充実
これらの施策により、システムの利用率を向上させ、投資効果を最大化します。
導入事例
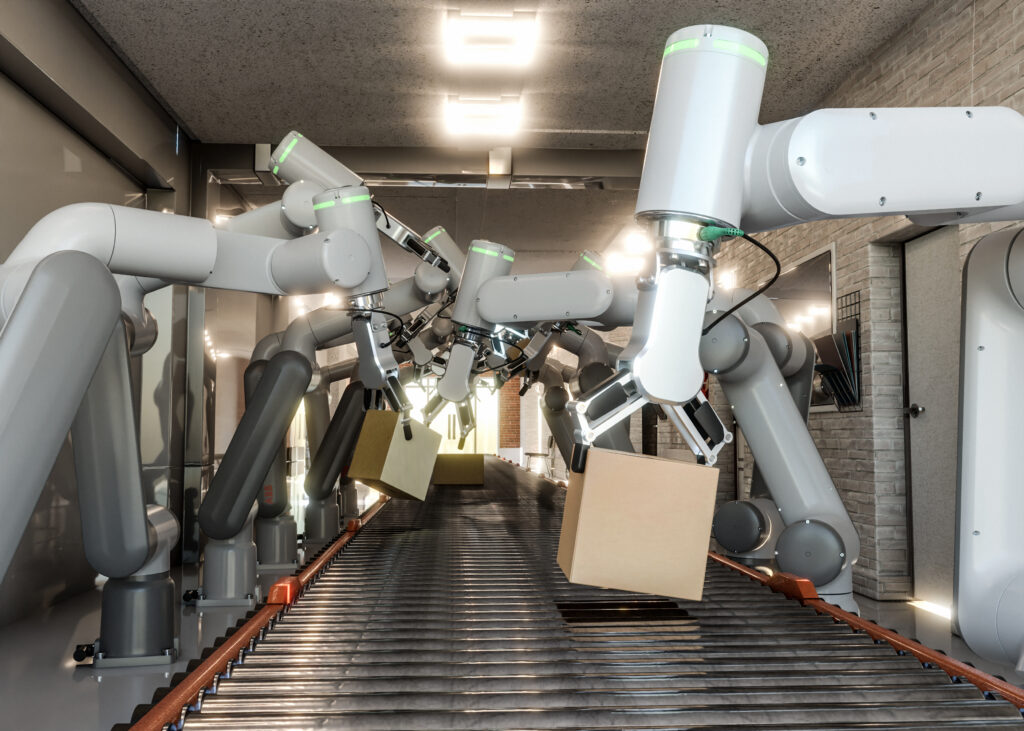
生産管理システムの導入効果を具体的に理解するため、実際の導入企業における取り組みと成果を紹介します。
製造業の業態や規模により最適なアプローチは異なりますが、これらの事例から得られる知見は、多くの企業にとって参考となるはずです。
自動車部品メーカーA社の事例
大手自動車メーカーの一次サプライヤーであるA社は、品質管理の強化と生産効率の向上を目的として、IoT×AI活用型の生産管理システムを導入しました。年間売上高は約500億円、従業員数は1,200名の中堅製造業です。
導入の背景と課題
A社が直面していた主な課題は、品質管理工程における人的依存度の高さでした。熟練検査員の高齢化が進む中、品質検査の自動化と標準化が急務となっていました。
また、生産ラインの状況をリアルタイムで把握できず、問題発生時の対応が後手に回るケースが頻発していました。
これらの課題に対し、以下の目標を設定して取り組みを開始しました。
- 検査工程の自動化率を90%に向上
- 不良品流出率を0.1%未満に低減
- 生産リードタイムを30%短縮
- 設備稼働率を85%以上に改善
システム導入のプロセス
プロジェクトは全体で18ヶ月をかけて実施され、以下の3フェーズで段階的に導入を進めました。
第1フェーズ(6ヶ月)では、IoTセンサーネットワークの構築とデータ収集基盤の整備を行いました。製造設備への各種センサーの設置、ネットワークインフラの増強、データ収集サーバーの構築などを実施。
特に重要な工程には、高精度な画像センサーと振動センサーを重点的に配置しました。
第2フェーズ(8ヶ月)では、AIによる品質検査システムの開発と導入を実施。深層学習モデルの学習には、過去3年分の検査データと不良品サンプルを活用。検査精度の向上のため、熟練検査員の知見をモデルに組み込む工夫を行いました。
第3フェーズ(4ヶ月)では、生産計画の最適化システムと予防保全システムを実装。需要予測の精度向上と、設備故障の予兆検知による計画外停止の削減を実現しました。
導入時の課題と解決策
プロジェクト推進において、いくつかの重要な課題に直面しました。最も深刻だったのは、現場作業者からの抵抗です。新システムの導入により、これまでの作業方法が大きく変わることへの不安が強かったためです。
この課題に対しては、以下の対策を実施しました。
- 各工程のリーダーを中心としたワーキンググループを結成
- 段階的な導入による負担軽減
- 操作研修の充実と、サポート体制の強化
- 改善提案制度の導入による現場の声の反映
また、既存設備とのデータ連携においても課題が発生しました。特に古い設備では、デジタルデータの取得が困難なケースがありました。
これに対しては、後付けのセンサーとデータコンバーターを活用することで対応。必要に応じて設備のコントローラーをアップグレードし、データ収集を可能にしました。
導入効果と成果
システム導入から1年後、以下の具体的な効果が確認されました。
品質面では:
- 不良品流出率が0.08%に低減(従来比85%減)
- 品質検査工程の人員を60%削減
- クレーム対応コストが年間4,000万円削減
生産効率では:
- 設備総合効率(OEE)が72%から88%に向上
- 生産リードタイムが35%短縮
- 在庫回転率が2.5回転から4.2回転に改善
コスト面では:
- 製造原価を8%削減
- 品質管理コストを40%削減
- 保守メンテナンスコストを25%削減
食品製造業B社の事例
大手食品メーカーの製造子会社であるB社は、食品安全管理の強化と生産性向上を目的として、最新の生産管理システムを導入しました。年間売上高は約200億円、従業員数は450名の製造拠点です。
導入の背景と課題
食品製造業特有の課題として、以下の点が挙げられていました。
- 原材料から製品までのトレーサビリティ確保
- 温度管理を含む製造環境のリアルタイム監視
- アレルゲン管理を含む製品切り替え時の品質保証
- 賞味期限管理と在庫の最適化
これらの課題に対し、以下の目標を設定しました。
- トレーサビリティ照会の応答時間を10分以内に短縮
- 製造環境の異常検知を5分以内に実現
- 製品切り替え時間を50%削減
- 在庫ロスを80%削減
システム導入のプロセス
導入プロジェクトは12ヶ月計画で実施され、以下の手順で進められました。
第1フェーズ(3ヶ月)では、製造環境のモニタリングシステムを構築。温度、湿度、圧力などの環境データをリアルタイムで収集し、製造条件の逸脱を即座に検知できる体制を整えました。
第2フェーズ(5ヶ月)では、製品トレーサビリティシステムを実装。原材料の入荷から製品出荷まで、すべての工程でデータを記録し、製造履歴を一元管理できる仕組みを構築しました。
第3フェーズ(4ヶ月)では、生産計画の最適化システムを導入。需要予測の精度向上により、在庫の適正化と製造ロスの削減を実現しました。
導入時の課題と解決策
食品製造特有の課題として、衛生管理基準への対応がありました。製造現場での端末やセンサーの設置には、防水・防塵性能が求められ、また洗浄・殺菌作業への耐性も必要でした。
これらの課題に対しては、以下の対策を実施しました。
- 防水・防塵規格IP67対応の機器を採用
- 非接触型センサーの活用
- 清掃性を考慮した機器配置
- 耐薬品性のある保護カバーの採用
また、季節変動の大きい製品特性に対応するため、AIによる需要予測モデルの精度向上が課題となりました。
この課題に対しては、気象データや市場トレンドデータを組み込んだハイブリッド予測モデルを開発し、予測精度の向上を実現しました。
導入効果と成果
システム導入から1年後、以下の効果が確認されました。
品質管理面では:
- トレーサビリティ照会時間が平均5分に短縮(従来比90%減)
- 製造環境の異常を平均3分以内に検知
- 品質逸脱による廃棄ロスが75%減少
生産効率では:
- 段取り替え時間が45%短縮
- 生産計画の精度が92%に向上
- 在庫回転率が3.2回転から5.8回転に改善
コスト面では:
- 製造原価を12%削減
- 在庫関連コストを65%削減
- 品質管理コストを35%削減
成功要因の分析
両社の事例から、生産管理システム導入の成功要因として、以下の点が重要であることが分かります。
段階的な導入アプローチ
システムの導入は、一度に全ての機能を実装するのではなく、段階的なアプローチを採用することで、現場への負担を軽減し、確実な定着を図ることが重要です。特に、以下の点に注意を払う必要があります。
- 優先度の高い課題から着手
- 各フェーズでの効果測定と改善
- 現場フィードバックの収集と反映
- 運用ノウハウの段階的な蓄積
現場主導の推進体制
システム導入の成否は、現場の協力と理解が鍵となります。両社とも、以下の取り組みにより、現場主導の推進体制を確立しました。
- 現場リーダーの早期巻き込み
- 定期的な進捗共有と課題討議
- 改善提案制度の活用
- 継続的なスキル向上支援
これらの取り組みにより、システムの効果的な活用と継続的な改善が可能となりました。
教えてシステム開発タロウくん!!
生産管理システムの導入について、よくある疑問にシステム開発のスペシャリスト「タロウくん」が答えます。
Q1:生産管理システムの導入にかかる期間と費用の目安を教えてください。
A1:システムの規模や要件にもよりますが、中規模製造業の場合、標準的な導入期間は12〜18ヶ月程度です。費用面では、システム開発に2億円〜3億円、IoTセンサー等のインフラ整備に5,000万円〜1億円程度が目安となります。
ただし、クラウドサービスを活用することで、初期投資を抑えることも可能です。投資回収期間は平均2〜3年です。
Q2:既存の生産設備とシステムとの連携は可能ですか?
A2:ほとんどの場合、連携は可能です。古い設備でもPLCやデータロガーを追加することで、データ収集が可能になります。
ただし、設備の種類や年式によって必要な対応は異なります。特に20年以上前の設備では、制御系の更新が必要になるケースもあります。具体的な連携方法は、設備の現状調査を行った上で判断する必要があります。
Q3:導入後のシステム運用体制はどうすればよいでしょうか?
A3:運用体制は「現場運用チーム」「システム保守チーム」「改善推進チーム」の3つの体制を整えることをお勧めします。
現場運用は各部門2〜3名のキーユーザーを選定し、システム保守は社内IT部門または外部ベンダーに委託、改善推進は現場と情報システム部門の混成チームで対応するのが一般的です。
24時間稼働の製造現場では、夜間休日のサポート体制も重要です。
Q4:AIやIoTの活用で具体的にどんなメリットがありますか?
A4:主な導入効果として、生産性30%向上、品質不良率70%削減、設備稼働率15%向上などが期待できます。
特に効果が高いのは予知保全で、計画外停止を80%削減できた事例もあります。また、熟練作業者のノウハウをAIに学習させることで、技能伝承の課題解決にも貢献します。
投資対効果(ROI)は業種や規模にもよりますが、平均で200〜300%程度となっています。
Q5:システムの導入で失敗しないためのポイントは?
A5:成功の鍵は3つです。まず「現場の巻き込み」です。開発の初期段階から現場の意見を取り入れ、使いやすいシステムを目指すことが重要です。
次に「段階的な導入」です。全ての機能を一度に導入するのではなく、優先度の高い機能から順次導入することで、リスクを最小化できます。
最後に「継続的な改善」です。導入後も定期的な効果測定と改善を行うことで、システムの価値を最大化できます。システムの導入はゴールではなく、継続的な改善の出発点と考えることが大切です。
よくある質問(FAQ)
以下では、生産管理システムの導入検討時によく寄せられる質問とその回答を紹介します。
Q1:生産管理システムの導入効果はどのくらいですか? A1:業種や規模により異なりますが、一般的に以下の効果が報告されています。生産性は平均30%向上、品質不良率は70%減少、在庫コストは40%削減が実現可能です。
投資回収期間は2〜3年が一般的で、ROIは200〜300%を達成している企業が多く見られます。特に品質管理工程の自動化では、検査工数の80%削減と、不良流出率の90%削減を同時に実現した事例もあります。
Q2:導入に必要な社内体制について教えてください。 A2:プロジェクト体制として、経営層、現場部門、情報システム部門からなる推進チームの構築が不可欠です。特に重要なのは、現場のキーパーソン2〜3名を専任で配置することです。
また、外部ベンダーとの連携体制も重要で、要件定義から運用開始まで一貫したサポートを受けられる体制を構築することをお勧めします。
導入後の運用体制として、システム管理者1名、部門担当者各1名、保守要員2名程度の配置が標準的です。
Q3:導入時の課題にはどのようなものがありますか? A3:主な課題として、以下の3点が挙げられます。まず「現場の抵抗」です。
新システム導入による業務変更への不安や抵抗感が生じやすく、丁寧な説明と段階的な移行が重要です。次に「データの品質」です。
特に既存システムからのデータ移行時に、データの不整合や欠損が発見されることが多く、クレンジング作業が必要となります。
最後に「システムの使いこなし」です。導入直後は機能を十分に活用できないケースが多く、継続的な教育とサポートが必要です。
Q4:システムのカスタマイズはどこまで可能ですか? A4:パッケージシステムの場合、標準機能の20〜30%程度のカスタマイズが一般的です。
主なカスタマイズ領域は、帳票フォーマット、ワークフロー、データ連携インターフェース、画面レイアウトなどです。
ただし、過度のカスタマイズはコスト増大とバージョンアップの障害となるため、業務プロセスの標準化を優先することをお勧めします。カスタマイズ範囲は、費用対効果を十分に検討した上で決定する必要があります。
Q5:セキュリティ対策はどの程度必要ですか? A5:製造データは企業の重要な資産であり、包括的なセキュリティ対策が必要です。
具体的には、ネットワークセキュリティ(ファイアウォール、暗号化通信)、アクセス制御(認証、権限管理)、データ保護(バックアップ、暗号化)の3層での対策が標準となります。
特に重要なのは、製造現場のネットワークとオフィスネットワークの分離で、不正アクセスやマルウェア感染のリスクを低減します。年間のセキュリティ運用コストは、システム投資額の5〜10%程度を見込む必要があります。
Q6:クラウドとオンプレミスはどちらが適していますか? A6:製造業の場合、ハイブリッド構成が最適です。基幹システムやデータ分析基盤はクラウドで構築し、製造現場の制御系システムはオンプレミスで運用するアプローチが一般的です。
クラウドのメリットとして、初期投資の抑制(40〜60%削減)、スケーラビリティの確保、災害対策の強化が挙げられます。
一方、制御系システムをオンプレミスとすることで、通信遅延の影響を排除し、安定した操業を実現できます。システム全体の年間運用コストは、クラウド化により20〜30%削減できるケースが多く見られます。
Q7:システムの保守・運用費用はどの程度かかりますか? A7:年間の保守・運用費用は、初期投資額の15〜20%程度が目安となります。
内訳として、ハードウェア保守(3〜5%)、ソフトウェア保守(5〜7%)、運用支援(5〜7%)、セキュリティ対策(2〜3%)となっています。
特に重要なのは、定期的なバージョンアップ費用で、2〜3年ごとに初期投資額の10〜15%程度が必要となります。また、システムの改善や機能拡張のための予算として、年間で初期投資額の5〜10%程度を確保することをお勧めします。
まとめ
生産管理システムの高度化は、製造業の競争力強化に不可欠な要素となっています。
IoTとAIを活用した最新システムの導入により、生産性向上、品質改善、コスト削減などの効果が期待できます。
システム開発では、現場のニーズを重視した段階的なアプローチが重要です。高品質な開発を実現するために、豊富な実績と技術力を持つパートナーの選定が成功の鍵となります。
お客様の生産管理システム開発についてのご相談は、こちらの [ベトナムオフショア開発 Mattock] までお気軽にお問い合わせください。
関連記事リンク
- スマートファクトリーの最新動向と導入事例
- 製造業DX成功のための5つのポイント
- IoTセンサー選定ガイド2025
- AI活用による品質管理の革新事例
- 製造業向けクラウドシステム選定ガイド