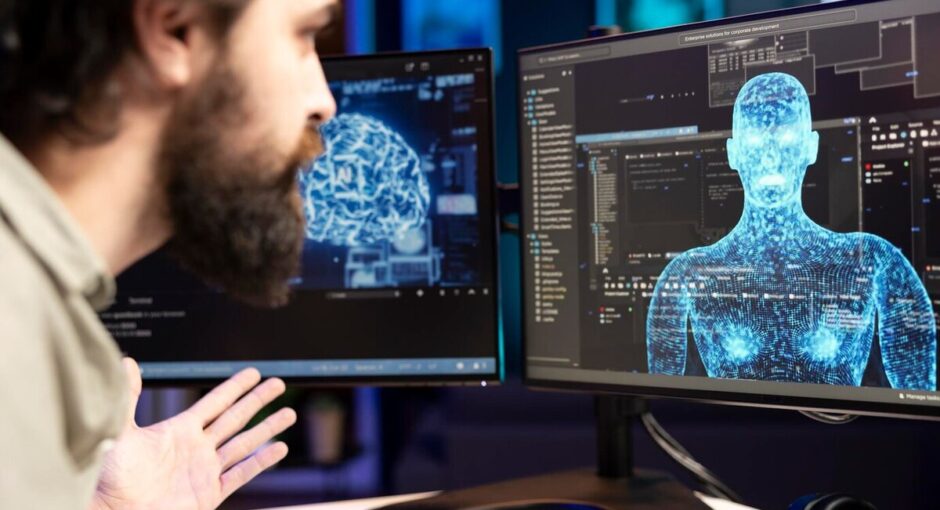
製造業におけるAI品質管理システムの開発と導入が加速する中、多くの企業が効率的な品質保証基盤の構築を目指しています。
本記事では、ディープラーニングを活用した品質管理システムの設計から運用まで、実践的な開発手法をご紹介します。
特に、画像検査による異常検知や予兆検知システムの実装に焦点を当て、具体的な導入手順とベストプラクティスを解説していきます。
この記事で分かること
- AI品質管理システムの設計・開発プロセスと具体的な実装方法
- 画像検査における異常検知モデルの実装手順と精度向上のための実践的なアプローチ
- 予兆検知システムの構築ノウハウと効果的な運用方法
- 実際の導入事例に基づく成功要因と注意点の詳細
- システム導入から運用までの包括的なロードマップと投資対効果の最大化手法
この記事を読んでほしい人
- 品質管理部門の責任者やマネージャーの方々
- 製造ラインの自動化を検討している技術者の皆様
- AI導入による品質改善を目指す経営層の方々
- 品質保証システムの刷新を計画している担当者の方々
- データサイエンティストやMLエンジニアの皆様
- 製造現場のDX推進担当者の方々
AI品質管理の現状と課題
製造業における品質管理は、従来の目視検査や統計的手法から、AIを活用したインテリジェントな品質管理へと大きく変革しています。
本セクションでは、現在の品質管理における課題と、AIによる解決アプローチについて詳しく解説します。
製造業が直面する品質管理の課題
製造現場では、製品の高度化や人手不足により、従来の品質管理手法では対応が困難になってきています。特に人的要因による検査のばらつきや、複雑化する製品への対応が大きな課題となっています。
検査工程の人的依存度
熟練検査員の高齢化や人材確保の困難さにより、安定した検査品質の維持が課題となっています。また、新人教育には多大な時間とコストが必要となり、早急な対応が求められています。
製品の高度化への対応
製品の微細化や複雑化により、人間の目による検査では限界が生じています。さらに、製品バリエーションの増加により、検査基準の統一化と維持が困難になってきています。
AI品質管理システムによる解決アプローチ
画像認識技術の活用
ディープラーニングを活用した画像認識技術により、人間の目では捉えきれない微細な異常や不良を検出することが可能となっています。
また、24時間365日安定した検査品質を維持できることから、製品品質の向上に大きく貢献しています。
データ駆動型の品質管理
センサーデータやプロセスデータを活用することで、製造プロセス全体を通じた品質管理が実現できます。リアルタイムでのモニタリングにより、異常の早期発見や予防保全が可能となっています。
導入における課題とその対策
AI品質管理システムの導入には、技術面から運用面まで様々な課題が存在します。これらの課題に対する適切な対策が、導入成功の鍵となります。
データ収集と整備の重要性
品質の高いAIモデルを構築するためには、十分な量の教師データが必要となります。製造現場での効率的なデータ収集体制の構築と、収集したデータの適切な整備が重要となります。
既存システムとの統合
多くの製造現場では、既存の品質管理システムが稼働しています。
新しいAIシステムを導入する際には、既存システムとの円滑な統合が課題となりますが、段階的な移行計画の策定により、この課題を解決することができます。
AI品質管理システムのメリット
AI品質管理システムの導入により、製造現場では多くの具体的なメリットが得られています。これらのメリットは、投資対効果の観点からも重要な指標となります。
検査精度の向上
従来の目視検査と比較して、検査精度が大幅に向上することが実証されています。特に、微細な傷や変形などの検出において、人間の目では見落としがちな不良を確実に検出することが可能となっています。
生産性の改善
検査工程の自動化により、作業効率が大幅に向上します。また、検査員の負担軽減や、夜間無人運転の実現など、働き方改革にも貢献しています。
コスト削減効果
不良品の流出防止や、検査工程の効率化により、品質管理に関わるコストを大幅に削減することができます。
さらに、予防保全による設備メンテナンスコストの最適化も実現できます。
今後の技術トレンド
AI品質管理システムは、技術の進歩とともに更なる進化を遂げています。最新のトレンドを把握することで、より効果的なシステム導入が可能となります。
エッジコンピューティングの活用
製造現場での即時的な判断が求められる場面では、エッジコンピューティングの活用が有効です。処理の低遅延化により、リアルタイムでの品質管理が実現できます。
説明可能なAIの実現
AI判断の根拠を可視化することで、品質管理の透明性が向上します。これにより、現場オペレーターの信頼性向上や、継続的な改善活動への活用が期待できます。
AI品質管理システムの基本設計
AI品質管理システムの構築には、適切なシステム設計が不可欠です。
本セクションでは、システムアーキテクチャの設計から、具体的なモデル選定まで、実装に必要な要素を詳しく解説します。
システムアーキテクチャの設計
効果的なAI品質管理システムを実現するためには、データの収集から分析、そして結果の出力までを一貫して処理できるアーキテクチャが必要となります。
データ収集基盤の構築
製造ラインから品質データを収集するためのセンサーやカメラシステムの配置が重要となります。
収集したデータは、リアルタイム処理と蓄積の両方に対応できる設計が求められます。
データ処理パイプライン
収集したデータを効率的に処理するためのパイプラインを構築します。
データの前処理、特徴抽出、モデルへの入力までを自動化することで、システムの安定性と効率性を確保します。
検査モデルの設計プロセス
品質管理における検査モデルの設計では、対象製品の特性や求められる精度に応じて、適切なアプローチを選択する必要があります。
データセットの準備
高精度なモデルを構築するためには、質の高い教師データの準備が不可欠です。
正常品と不良品のサンプルを十分に収集し、適切なラベリングを行います。
モデルアーキテクチャの選定
検査対象や要求精度に応じて、最適なモデルアーキテクチャを選定します。
画像検査では主にCNNベースのモデルが用いられ、異常検知ではオートエンコーダーなども活用されます。
データ前処理の重要性
AIモデルの性能を最大限に引き出すためには、適切なデータ前処理が重要となります。
画像データの標準化
製造ラインで撮影された画像データは、照明条件やカメラアングルによってばらつきが生じます。
これらを適切に補正し、一貫性のあるデータセットを作成します。
ノイズ処理とフィルタリング
製造現場特有のノイズや外乱を除去するための処理を実装します。
適切なフィルタリングにより、モデルの判定精度を向上させることができます。
モデル学習と評価
開発したモデルの性能を最大限に引き出すためには、適切な学習プロセスと評価方法の設計が重要となります。
学習プロセスの最適化
モデルの学習では、ハイパーパラメータの調整や学習率のスケジューリングなど、細かな最適化が必要となります。
交差検証を用いて、モデルの汎化性能を確保します。
評価指標の設定
検査システムの性能を適切に評価するために、複数の評価指標を設定します。
適合率や再現率、F値などの指標を組み合わせることで、総合的な性能評価を行います。
システム統合と展開
開発したAIモデルを実際の製造ラインに導入する際には、既存システムとの統合が重要となります。
既存システムとの連携
品質管理システムやMESなど、既存の製造システムとの円滑な連携を実現します。
データフォーマットの統一や通信プロトコルの設計により、シームレスな統合を目指します。
スケーラビリティの確保
将来的なシステム拡張や性能向上に対応できるよう、スケーラブルな設計を心がけます。
モジュール化された設計により、保守性と拡張性を確保します。
異常検知システムの実装
異常検知システムは、AI品質管理システムの中核を担う重要な要素となります。
本セクションでは、画像ベースの異常検知システムの実装から、リアルタイム処理の実現まで、具体的な実装手法について解説します。
画像検査システムの構築
製造ラインにおける画像検査システムは、製品の外観検査や寸法測定など、多岐にわたる検査項目に対応する必要があります。
カメラシステムの設計
検査対象の特性に応じて、適切なカメラの選定と配置を行います。照明条件の制御や、撮影タイミングの最適化により、安定した画像取得を実現します。
画像処理パイプラインの実装
取得した画像データに対して、ノイズ除去や特徴抽出などの前処理を行います。画像の正規化や増強処理により、検出精度の向上を図ります。
リアルタイム異常検知の実現
製造ラインでは、製品の品質を即時に判定する必要があります。そのため、高速かつ安定したリアルタイム処理の実装が求められます。
推論処理の最適化
モデルの軽量化や量子化により、推論処理の高速化を実現します。また、バッチ処理の最適化により、処理効率の向上を図ります。
並列処理システムの構築
複数のGPUを活用した並列処理システムにより、処理能力の向上を実現します。負荷分散の最適化により、安定した処理性能を確保します。
統計的プロセス管理との連携
AIによる異常検知と、従来の統計的プロセス管理(SPC)を組み合わせることで、より信頼性の高い品質管理を実現します。
SPCデータの活用
工程能力指数や管理図などのSPCデータを、AIモデルの入力として活用します。統計的な異常判定とAIによる判定を組み合わせることで、検出精度の向上を図ります。
ハイブリッド判定システム
AIと統計的手法それぞれの特長を活かした、ハイブリッドな判定システムを構築します。複数の判定基準を組み合わせることで、誤検知の低減を実現します。
精度向上のためのチューニング
異常検知システムの性能を最大限に引き出すためには、継続的なチューニングが必要となります。
モデルの最適化
検査対象や環境の変化に応じて、モデルのパラメータを適切に調整します。定期的な再学習により、検出精度の維持向上を図ります。
アンサンブル学習の活用
複数のモデルを組み合わせたアンサンブル学習により、検出精度の向上を実現します。異なる特徴を捉えたモデルを組み合わせることで、より堅牢な判定を実現します。
判定結果の可視化
異常検知システムの判定結果を、現場オペレーターが理解しやすい形で可視化することが重要となります。
リアルタイムモニタリング
検査結果をリアルタイムで表示するモニタリングシステムを実装します。異常箇所の強調表示や、判定根拠の提示により、判定結果の理解を促進します。
分析レポートの自動生成
検査データの傾向分析や、異常発生パターンの分析結果を、自動的にレポート化します。データの可視化により、品質改善活動への活用を促進します。
予兆検知機能の開発
予兆検知は製造プロセスにおける異常を未然に防ぐための重要な機能です。
本セクションでは、センサーデータの収集から予測モデルの構築まで、効果的な予兆検知システムの開発手法について解説します。
データ収集と統合
予兆検知の精度を高めるためには、多様なデータソースからの情報収集と適切な統合が不可欠となります。
センサーデータの収集
製造設備に設置された各種センサーからのデータを収集します。振動、温度、電流値など、設備の状態を示す様々なパラメータを継続的にモニタリングします。
プロセスデータの活用
製造プロセスの各工程で生成されるデータを収集します。加工条件や設備パラメータなど、製品品質に影響を与える要因を特定し、データとして蓄積します。
前処理とデータクレンジング
収集したデータの品質を確保するため、適切な前処理とクレンジングを実施します。
ノイズ除去と欠損値処理
センサーデータに含まれるノイズの除去や、欠損値の補完を行います。データの連続性と信頼性を確保することで、予測精度の向上を図ります。
特徴量エンジニアリング
収集したデータから、予兆検知に有効な特徴量を抽出します。時系列データの特性を考慮した特徴量設計により、異常の予兆を効果的に捉えます。
予測モデルの構築
収集したデータを基に、異常の予兆を検知するための予測モデルを構築します。
時系列分析手法の活用
RNNやLSTMなどの時系列分析に適したモデルを活用します。データの時間的な依存関係を考慮することで、より精度の高い予測を実現します。
マルチモーダル学習の実装
複数のデータソースを組み合わせたマルチモーダル学習により、予測精度の向上を図ります。異なる特性を持つデータを統合的に分析することで、より正確な予兆検知を実現します。
予測精度の評価と改善
開発した予測モデルの性能を適切に評価し、継続的な改善を行います。
評価指標の設定
予測の正確性や早期検知能力など、複数の観点から評価指標を設定します。実際の異常発生との関連性を分析し、モデルの有効性を検証します。
モデルの最適化
運用データを基にモデルのチューニングを行い、予測精度の向上を図ります。検知の早期化と誤検知の低減のバランスを考慮した最適化を実施します。
システム統合と実装
開発した予兆検知システムを、実際の製造ラインに統合します。
リアルタイム予測システム
収集したデータをリアルタイムで分析し、異常の予兆を検知するシステムを構築します。アラート機能の実装により、迅速な対応を可能にします。
可視化インターフェースの開発
予兆検知の結果を、直感的に理解できるインターフェースで表示します。時系列でのトレンド表示や、リスク度の可視化により、運用者の意思決定を支援します。
具体的な導入事例
AI品質管理システムの効果をより具体的に理解していただくため、実際の導入事例をご紹介します。
それぞれの事例から、導入時の課題とその解決方法、そして得られた成果について詳しく解説します。
食品工場での活用事例
大手食品メーカーA社における異物混入検査システムの導入事例について説明します。
導入背景と課題
従来の目視検査では見落としのリスクが高く、検査員の負担も大きい状況でした。特に微細な異物の検出において、より高精度な検査システムの導入が求められていました。
実装したソリューション
ディープラーニングを活用した画像検査システムを導入し、異物の自動検出を実現しました。独自の画像処理アルゴリズムにより、微細な異物でも高精度な検出が可能となっています。
自動車部品製造での実践例
自動車部品メーカーB社における品質管理システムの刷新事例を紹介します。
システム構築のアプローチ
製造ラインの各工程にセンサーを設置し、リアルタイムでのデータ収集を実現しました。収集したデータを基に、品質予測モデルを構築し、不良品の発生を未然に防ぐシステムを実装しています。
得られた効果と改善点
不良率の65%低減を達成し、年間のコスト削減効果は約2億円に達しています。また、予兆検知機能により、設備の予防保全も実現しています。
電子部品製造での導入例
精密機器メーカーC社における外観検査システムの導入事例について解説します。
要件定義と課題解決
製品の微細な傷や変形を検出する必要があり、高解像度カメラと専用の照明システムを組み合わせた検査システムを構築しました。
運用結果と効果測定
検査精度が従来比で30%向上し、人的コストを40%削減することに成功しています。また、検査データの蓄積により、製造プロセスの改善にも活用されています。
医療機器製造での実装例
医療機器メーカーD社における品質保証システムの導入事例を紹介します。
規制対応と品質保証
医療機器製造特有の厳格な品質基準に対応するため、トレーサビリティを重視したシステム設計を行いました。
システムの特徴と成果
全工程のデータを統合的に管理し、製品一つ一つの製造履歴を追跡可能なシステムを実現しています。品質管理の工数を50%削減しつつ、製品の信頼性を向上させることに成功しました。
半導体製造での活用事例
半導体メーカーE社におけるウェハー検査システムの導入例について説明します。
技術的な課題と解決策
ナノレベルの欠陥検出が求められる中、AIによる画像認識と従来の光学的検査を組み合わせたハイブリッドシステムを構築しました。
導入効果と今後の展開
検査精度が従来比で45%向上し、処理速度も2倍に向上しています。今後は予兆検知機能の強化により、さらなる品質向上を目指しています。
システム運用と保守管理
AI品質管理システムを効果的に機能させるためには、適切な運用体制の構築と継続的な保守管理が不可欠です。
本セクションでは、システムの安定運用を実現するための具体的な方法論と実践的なノウハウについて解説します。
運用体制の構築
効果的なシステム運用を実現するためには、現場のオペレーターからシステム管理者まで、各役割の責任範囲を明確にした体制づくりが重要となります。
運用チームの編成
システムの保守運用を担当する専門チームを編成します。
AIエンジニア、品質管理専門家、現場オペレーターなど、異なる専門性を持つメンバーで構成することで、多角的な視点での運用管理を実現します。
教育訓練プログラム
システムの適切な運用のため、定期的な教育訓練プログラムを実施します。
基本的な操作方法から、異常時の対応手順まで、体系的な教育を提供することで、運用品質の向上を図ります。
日常的な監視と保守
システムの安定稼働を維持するためには、日々の監視活動と適切な保守作業が重要です。
モニタリング体制
システムの稼働状況や性能指標を常時監視する体制を整備します。
リアルタイムでの異常検知と、迅速な対応を可能にする監視体制を構築することで、システムの安定性を確保します。
定期点検の実施
カメラやセンサー類の校正、システムログの確認など、定期的な点検作業を実施します。予防保全的なアプローチにより、システムの信頼性維持と長期的な安定運用を実現します。
トラブルシューティング
システム障害や異常が発生した際の、効果的な対応手順を確立します。
障害対応プロセス
システム異常の検知から原因究明、対策実施までの標準的な対応プロセスを策定します。エスカレーションルートを明確化し、迅速な問題解決を可能にします。
復旧手順の整備
様々な障害パターンに対する復旧手順を事前に整備します。システムのバックアップ体制や、代替運用手順の確立により、業務への影響を最小限に抑えます。
継続的な改善活動
システムの性能を維持向上させるため、継続的な改善活動を実施します。
パフォーマンス分析
システムの検査精度や処理速度など、主要な性能指標を定期的に分析します。データに基づく改善策の立案により、システム性能の最適化を図ります。
モデルの更新管理
検査対象の変更や新たな不良パターンの追加に応じて、AIモデルの更新を実施します。適切なバージョン管理と検証プロセスにより、安全なモデル更新を実現します。
コスト分析とROI
AI品質管理システムの導入を検討する際には、投資対効果(ROI)の適切な評価が重要となります。
本セクションでは、システム導入にかかる費用の内訳と、期待される投資回収効果について具体的に解説します。
初期投資の試算
システム導入時に必要となる初期投資について、主要な費用項目とその概算を説明します。
ハードウェア費用
カメラやセンサー類の機器費用、計算機システムの導入費用、ネットワーク機器の整備費用など、システムの基盤となるハードウェアへの投資が必要となります。
一般的な製造ラインの場合、2,000万円から5,000万円程度の投資が見込まれます。
ソフトウェア開発費用
AIモデルの開発費用、システムインテグレーション費用、カスタマイズ費用など、ソフトウェアの開発と導入にかかる費用を見積もります。
開発規模にもよりますが、3,000万円から1億円程度の費用が必要となります。
ランニングコストの分析
システム導入後の運用にかかる継続的なコストについて説明します。
保守運用費用
システムの日常的な保守管理、定期的なモデル更新、技術サポートなどにかかる費用を試算します。
年間で初期投資額の15%から20%程度を見込む必要があります。
教育訓練費用
運用担当者の教育訓練、技術力向上のための研修など、人材育成にかかる費用も重要な検討項目となります。
年間で500万円から1,000万円程度の投資が推奨されます。
投資対効果の算出
システム導入による具体的な効果を金額換算し、投資回収期間を試算します。
定量的効果の試算
不良品の削減効果、人件費の削減効果、生産性向上による増収効果など、具体的な数値に基づいて効果を算出します。
一般的には2年から3年程度での投資回収が見込まれます。
教えてシステム開発タロウくん!!
AI品質管理システムの導入や運用に関して、よくお寄せいただく質問について、システム開発のエキスパートであるタロウくんが分かりやすく解説します。
実務での疑問点や課題について、具体的な回答を提供します。
システム導入に関する質問
現場でよく聞かれる、システム導入時の実践的な疑問に答えます。
導入期間について
Q:AI品質管理システムの導入にはどのくらいの期間が必要ですか?
基本的な画像検査システムであれば3〜6ヶ月程度、予兆検知機能まで含めると6〜12ヶ月程度が標準的な期間となります。
ただし、製造ラインの複雑さや要求される精度によって変動する可能性があります。
既存システムとの統合
Q:既存の品質管理システムとの統合は可能ですか?
可能です。
APIやミドルウェアを活用することで、既存システムとの段階的な統合を実現できます。多くの場合、並行運用期間を設けることで、スムーズな移行が可能です。
運用に関する質問
システムの日常的な運用に関する実践的な質問にお答えします。
精度向上について
Q:導入後の検査精度はどの程度向上しますか?
一般的に、導入直後から30%程度の精度向上が見込まれ、運用データの蓄積と継続的な学習により、さらに15〜20%程度の改善が期待できます。
メンテナンス体制
Q:システムのメンテナンスにはどのような体制が必要ですか?
社内のAI担当者と品質管理担当者を中心としたチーム体制が推奨されます。また、システムベンダーによる定期的なサポートを併用することで、安定した運用が可能となります。
まとめ
AI品質管理システムは、製造業における品質保証の新たな基盤として、ますます重要性を増しています。
画像検査による異常検知から予兆検知まで、AIを活用した包括的な品質管理の実現により、製造現場の生産性と品質の大幅な向上が期待できます。
開発パートナーの重要性
AI品質管理システムの導入を成功に導くためには、豊富な開発実績と技術力を持つパートナーの選定が重要です。
Mattockは、ベトナムオフショア開発のリーディングカンパニーとして、AI品質管理システムの開発から運用まで、包括的なサポートを提供いたします。
カスタマイズされたAI品質管理システムの開発についてのご相談は、以下のお問い合わせフォームよりお気軽にご連絡ください。
AI品質管理システム開発の無料相談はこちら