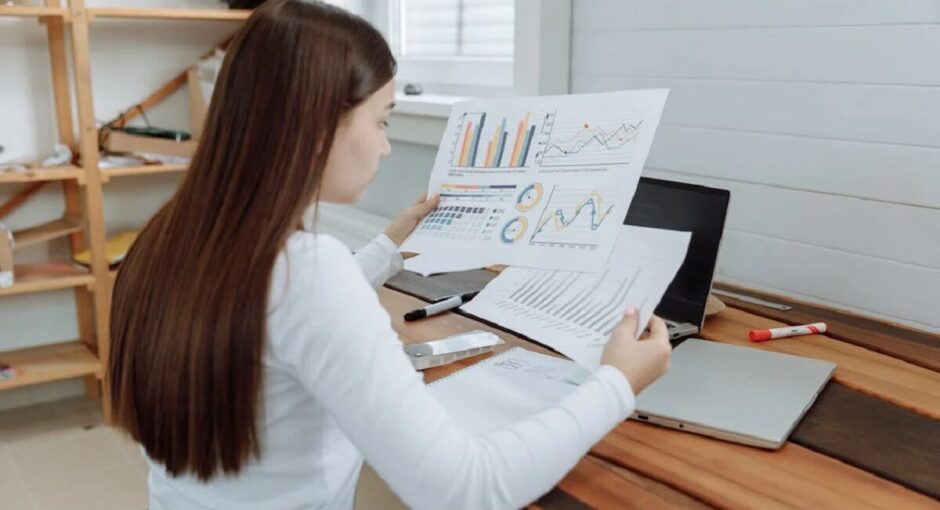
DX(デジタルトランスフォーメーション)が叫ばれる中、中堅製造業の皆様は、どのようにして自社の競争力を高め、未来への成長を実現できるか悩んでいらっしゃるのではないでしょうか。その答えの一つが、ERP(Enterprise Resource Planning)システムの導入・開発にあります。
本記事では、ERPがなぜDX成功の鍵となるのか、中堅製造業がERPを導入・開発する上でのメリット・デメリット、成功事例などを詳しく解説します。また、ERP選定のポイントや、開発の進め方についても具体的な事例を交えてご紹介します。
ERP導入を検討されている方はもちろん、DX推進の一環として新たなシステム導入を検討されている方も、ぜひ本記事を参考にして、自社の未来を描き、具体的なアクションにつなげてください。
この記事を読んでほしい人
- 中堅製造業の経営者・経営幹部の方々
- IT部門責任者・担当者の方々
- DX推進を検討している製造業の方々
- システム刷新を検討している企業の経営層
- ERP導入プロジェクトのマネージャー
- デジタル化による業務改革を目指す管理職の方々
この記事でわかること
- ERPシステムの本質的な価値と導入効果
- 製造業特有のERP導入における課題と解決策
- DX推進におけるERPの戦略的活用方法
- ERP開発・導入の具体的なステップと注意点
- 最新技術(AI/IoT)を活用したERP展開事例
- 投資対効果を最大化するためのプロジェクト管理手法
- グローバル展開を見据えたERP戦略
ERPがもたらす製造業のデジタル革新
製造業を取り巻く環境は、グローバル競争の激化、人手不足、サプライチェーンの複雑化など、年々厳しさを増しています。このような状況下で、ERPは単なる基幹システムではなく、企業の競争力を高めるためのデジタル革新の基盤として、その重要性が増しています。
本章では、ERPが製造業にもたらす本質的な価値と、DX推進における戦略的意義について詳しく解説します。
ERPの本質的価値を理解する
ERPは「Enterprise Resource Planning(企業資源計画)」の略称ですが、その本質は企業活動全体を一つの有機的なシステムとして統合し、経営効率を最大化することにあります。製造業における具体的な価値として、まず生産計画から在庫管理、原価管理、品質管理までの一連のプロセスを統合的に管理できることが挙げられます。
例えば、受注情報が入力されると、必要な部材の在庫確認、発注計画の立案、生産スケジュールの調整が自動的に行われ、さらに原価計算や納期回答までが一気通貫で処理されます。
これにより、従来は部門間の調整に費やされていた時間を大幅に削減し、より戦略的な業務に人材を振り向けることが可能になります。
製造業DXにおけるERPの役割
製造業のDXにおいて、ERPは重要な基盤システムとしての役割を担います。従来の紙ベースやエクセルベースの管理から脱却し、全社的なデータのデジタル化を実現することで、AIやIoTなど先進技術の活用への道を開きます。
例えば、生産現場のIoTデータをERPに集約することで、リアルタイムの進捗管理や予知保全が可能になります。さらに、蓄積されたデータをAIで分析することで、需要予測の精度向上や最適な生産計画の立案が実現できます。
これらは、単なる業務効率化を超えて、新たなビジネスモデルの創出にもつながる可能性を秘めています。
グローバル競争力強化のためのERP活用
製造業のグローバル展開において、ERPは重要な競争力の源泉となります。海外拠点との情報連携、多通貨対応、各国の法規制対応など、グローバルビジネスに必要な機能を統合的に提供することで、シームレスな事業運営を可能にします。
特に中堅製造業にとって、限られたリソースでグローバル展開を進める上で、ERPの活用は必須といえます。例えば、ある自動車部品メーカーでは、ERPの導入により海外拠点との在庫情報の共有がリアルタイム化され、適正在庫の維持と物流コストの30%削減を実現しました。
また、品質情報の一元管理により、品質問題の早期発見と対策が可能となり、顧客満足度の向上にもつながっています。
ERP開発・導入プロジェクトの進め方
ERP開発・導入プロジェクトは、企業の将来を左右する重要な取り組みです。
本章では、プロジェクトを成功に導くための具体的なステップと、各フェーズで押さえるべきポイントについて解説します。
準備フェーズ:プロジェクトの成功基盤を築く
プロジェクト開始前の準備段階で、以下の点を十分に検討することが重要です。まず、現状の業務プロセスを可視化し、課題を明確にします。その上で、ERPによって実現したい目標を具体的に設定します。
この際、単なるシステム更新ではなく、業務改革の機会としてとらえることが重要です。
例えば、ある精密機器メーカーでは、ERP導入に先立ち、全部門の業務フローを可視化し、約200の業務改善ポイントを特定しました。その結果、ERP導入後の業務効率化目標を明確に設定することができ、プロジェクト完了時には当初の目標を上回る40%の工数削減を達成しています。
要件定義フェーズ:成功の鍵を握る重要プロセス
要件定義は、ERPプロジェクトの成否を決める最も重要なフェーズです。現場の要望を丁寧にヒアリングしながら、業界のベストプラクティスを取り入れ、最適な要件を定義していきます。
この際、重要なのは「あるべき姿」を描きつつ、現実的な実装範囲を見極めることです。ある工作機械メーカーでは、要件定義に3か月を費やし、現場の意見を丁寧に集約した上で、3段階に分けた段階的な導入計画を策定しました。
その結果、初期導入から6か月で投資回収を実現し、その後の展開もスムーズに進めることができました。
開発・構築フェーズ:確実な実装を目指して
開発・構築フェーズでは、要件定義に基づいて実際のシステム構築を進めます。このフェーズでは、進捗管理と品質管理が特に重要になります。定期的なマイルストーンレビューを設定し、要件との整合性を確認しながら進めていく必要があります。
特に注意すべきは、開発中に発生する要件変更への対応です。安易な変更要望を受け入れると、スケジュールの遅延やコストの増大を招く恐れがあります。
ある電子部品メーカーでは、変更管理委員会を設置し、影響度評価に基づく厳格な変更管理を実施することで、当初の予算とスケジュールを維持したまま、高品質なシステムを構築することに成功しています。
テストフェーズ:品質を確保する重要なステップ
テストフェーズは、システムの品質を確保する最後の砦です。単体テスト、結合テスト、システムテスト、そしてユーザー受入テストと、段階的にテストを実施していきます。特に製造業のERPでは、生産管理や在庫管理など、ミスが許されない重要な業務プロセスが多いため、より慎重なテストが求められます。
ある自動車部品メーカーでは、テストケースの作成に現場担当者を積極的に巻き込み、実際の業務シナリオに基づいた約1万件のテストケースを作成しました。その結果、本番稼働後のトラブルを最小限に抑え、スムーズな移行を実現することができました。
本番稼働フェーズ:慎重な移行計画が成功を左右する
本番稼働は、プロジェクトの山場となります。特に製造業では、生産活動を止めることなく新システムへの移行を実現する必要があります。そのため、綿密な移行計画の策定と、全社を挙げての準備が不可欠です。
ある電機メーカーでは、まず営業所システムから段階的に移行を開始し、その後工場システム、本社システムの順で移行を進めました。各フェーズで得られた知見を次のフェーズに活かすことで、リスクを最小限に抑えながら、確実な移行を実現しています。
最新技術を活用したERP進化の方向性
ERPは、AI、IoT、クラウドなどの最新技術との融合により、さらなる進化を遂げています。本章では、これらの技術がERPにもたらす新たな可能性について解説します。
AIによる高度な分析と予測
AIをERPに組み込むことで、データ分析の精度と速度が飛躍的に向上します。例えば、需要予測においては、過去の販売データだけでなく、気象データやSNSデータなども含めた多角的な分析が可能になり、予測精度が大幅に向上します。
ある食品メーカーでは、AI搭載のERPを導入することで、需要予測の精度が従来比で30%向上し、在庫回転率の改善と欠品率の低下を同時に実現しました。さらに、原材料の発注タイミングも最適化され、調達コストの削減にもつながっています。
IoTとの連携による製造現場の可視化
IoTセンサーとERPを連携させることで、製造現場のリアルタイムな状況把握が可能になります。設備の稼働状況、生産進捗、品質データなどを自動的に収集・分析することで、より効率的な生産管理を実現できます。
ある機械メーカーでは、主要設備にIoTセンサーを設置し、ERPと連携させることで、設備の稼働率が15%向上し、予防保全による計画外停止時間の80%削減を達成しました。また、品質データのリアルタイム分析により、不良率も半減しています。
ERPシステムの選定基準と比較のポイント
ERPシステムの選定は、プロジェクト成功の重要な要素です。本章では、システム選定時の具体的な評価基準と、製造業特有の考慮点について詳しく解説します。
パッケージ型とクラウド型の比較
システム選定において、まず検討すべきはパッケージ型とクラウド型の選択です。それぞれの特徴を詳しく見ていきましょう。
パッケージ型ERPは、カスタマイズの自由度が高く、自社の業務プロセスに合わせた細かい調整が可能です。ある精密機器メーカーでは、独自の品質管理プロセスをシステムに組み込むため、パッケージ型を選択し、約20%のカスタマイズを加えることで、理想的な業務フローを実現しました。
一方、クラウド型ERPは、初期投資を抑えられ、導入期間も短縮できるメリットがあります。ある金属加工メーカーでは、クラウド型ERPを採用することで、導入期間を従来の半分以下に短縮し、3ヶ月での本番稼働を実現しています。
業界特有の機能要件
製造業向けERPには、以下のような業界特有の機能が必要とされます。選定時には、これらの機能の実装レベルを詳細に評価することが重要です。
生産管理機能については、MRPやスケジューリング、工程管理など、製造業の根幹となる機能の充実度を確認します。特に、変種変量生産への対応や、生産計画の柔軟な変更機能は重要な評価ポイントとなります。
品質管理機能では、トレーサビリティや検査データの管理、不適合管理など、製品品質に直結する機能の実装状況を確認します。ある自動車部品メーカーでは、完全なトレーサビリティ機能を持つERPを選択することで、品質問題の原因究明時間を80%削減することに成功しています。
ERPを活用した製造業の未来戦略
ERPは、単なる業務効率化のツールではなく、製造業の未来を切り開くための戦略的プラットフォームとなります。本章では、ERPを活用した長期的な成長戦略について解説します。
デジタルツインへの展開
ERPに蓄積されたデータを活用し、製造現場のデジタルツイン化を推進する企業が増えています。ある工作機械メーカーでは、ERPと連携したデジタルツインにより、生産ラインの最適化シミュレーションを実現し、生産効率を25%向上させることに成功しました。
サービタイゼーションへの対応
製造業のサービス化(サービタイゼーション)において、ERPは重要な基盤となります。製品の稼働データをERPに集約し、予防保全サービスや性能保証サービスなど、新たな付加価値サービスの創出を可能にします。
ある産業機械メーカーでは、ERPを基盤としたサービタイゼーション戦略により、従来のスポット保守から予防保全サービスへの転換を実現し、サービス収益を前年比200%に拡大しています。
グローバル展開を見据えたERP戦略
中堅製造業のグローバル展開において、ERPは重要な役割を果たします。本章では、グローバル展開時の具体的な戦略と注意点について解説します。
マルチサイト運用の実践
複数拠点でのERP運用には、特有の課題が存在します。ある電子部品メーカーでは、日本、中国、タイの3拠点でERPを展開する際、以下のような対策を講じることで、スムーズな統合運用を実現しました。
まず、基幹データの一元管理を実現するため、マスターデータ管理(MDM)の仕組みを構築しました。品目コードや取引先コードなどの基幹データを統一的に管理することで、拠点間の情報連携がスムーズになり、グローバルでの在庫最適化が可能になりました。
また、各拠点の多言語対応として、画面表示や帳票を現地語に対応させながらも、データベース上では統一コードを使用する方式を採用しました。これにより、拠点間のデータ連携を維持しながら、現地スタッフの使いやすさを確保しています。
サプライチェーンの最適化
グローバルサプライチェーンの可視化と最適化は、ERPの重要な役割の一つです。ある自動車部品メーカーでは、ERPを活用したサプライチェーン改革により、以下のような成果を上げています。
調達面では、グローバルでの発注を一元管理することで、購買力を強化し、原材料コストの15%削減を実現しました。また、サプライヤーの評価情報をグローバルで共有することで、品質管理の強化にもつながっています。
物流面では、拠点間の在庫移動を最適化し、輸送コストを20%削減することに成功しています。特に、AIを活用した需要予測により、各拠点の適正在庫レベルを維持しながら、物流の効率化を実現した点が注目されます。
次世代製造業に向けたERP活用戦略
製造業を取り巻く環境は、急速に変化しています。本章では、次世代の製造業において求められるERP活用の方向性について解説します。
スマートファクトリーへの進化
ERPは、スマートファクトリー実現の中核を担います。ある精密機器メーカーでは、ERPを基盤としたスマートファクトリー化により、以下のような革新を実現しています。
まず、製造設備のIoTデータをERPにリアルタイムで集約し、AI分析による予知保全を実現しました。これにより、設備の計画外停止を90%削減し、生産性を大幅に向上させています。
また、作業者の動線分析や工程の自動最適化により、生産効率を30%向上させることに成功しています。ERPに蓄積されたデータを基に、AIが最適な作業順序や人員配置を提案する仕組みを構築しました。
カーボンニュートラルへの対応
環境負荷低減は、製造業における重要な課題です。ERPを活用したカーボンニュートラルへの取り組みも始まっています。ある化学メーカーでは、ERPに環境負荷管理機能を追加し、以下のような取り組みを実現しています。
製造工程ごとのCO2排出量を可視化し、リアルタイムでモニタリングすることで、環境負荷の少ない生産計画の立案が可能になりました。その結果、CO2排出量を前年比15%削減することに成功しています。
ERPシステムの将来展望と投資対効果の最大化
ERPシステムは、技術革新とビジネス環境の変化に応じて進化を続けています。本章では、今後のERP展開における重要なトレンドと、投資効果を最大化するためのアプローチについて解説します。
次世代ERPの特徴と可能性
従来のERPは、業務の効率化と統合管理が主な目的でしたが、次世代のERPはより戦略的な役割を担うようになっています。ある産業機械メーカーでは、次世代ERPの特徴を活かし、以下のような革新を実現しています。
リアルタイムアナリティクスにより、経営判断のスピードが大幅に向上しました。従来は月次での分析が中心でしたが、現在では日次、さらには時間単位での経営指標の把握が可能となり、市場変化への対応力が強化されています。
また、機械学習による異常検知システムを導入し、品質管理や設備保全の高度化を実現しました。不良品の発生を事前に予測し、予防的な対策を講じることで、品質コストを40%削減することに成功しています。
投資対効果を最大化するアプローチ
ERP投資の効果を最大限に引き出すためには、システムの導入だけでなく、組織全体の変革が必要です。ある電機メーカーでは、以下のような取り組みにより、ERPの投資対効果を大きく向上させています。
まず、部門横断的な改善推進チームを設置し、ERPの活用度を定期的に評価・改善する仕組みを構築しました。その結果、システムの利用率が向上し、導入効果を最大限に引き出すことに成功しています。
また、データ活用人材の育成にも注力し、社内でのデータ分析スキルの向上を図っています。これにより、ERPから得られるデータを活用した業務改善が活発化し、継続的な改善サイクルが確立されています。
リスク管理と危機対応
ERPは企業の基幹システムであるため、万全のリスク管理体制が求められます。本章では、具体的なリスク対策と危機管理のアプローチについて解説します。
システムダウン対策の実践
システムダウンは、製造業において深刻な影響をもたらす可能性があります。ある自動車部品メーカーでは、以下のような多層的な対策を実施しています。
まず、システムの二重化により、主系システムに障害が発生した場合でも、即座に副系システムに切り替えることが可能な体制を構築しました。また、定期的な災害復旧訓練を実施し、実際の緊急時にも冷静に対応できる体制を整えています。
これらの対策により、システム稼働率99.99%を達成し、安定した事業運営を実現しています。
サイバーセキュリティ対策の強化
製造業のデジタル化が進む中、サイバーセキュリティの重要性も増しています。ある精密機器メーカーでは、ERPのセキュリティ対策として、以下のような施策を実施しています。
アクセス権限の厳格な管理や、暗号化技術の導入はもちろん、AIを活用した異常検知システムにより、不正アクセスの早期発見と対応を可能にしています。また、定期的なセキュリティ監査と、従業員への教育プログラムを実施することで、人的要因によるリスクも最小限に抑えています。
運用最適化と人材育成の戦略
ERPの真価を発揮するためには、システムの導入後の運用体制と人材育成が重要です。本章では、持続可能な運用体制の構築と、それを支える人材育成について解説します。
持続可能な運用体制の確立
ERPの運用は、単なるシステム保守ではなく、継続的な業務改善の機会として捉える必要があります。ある工作機械メーカーでは、以下のような運用体制を構築し、大きな成果を上げています。
運用体制の中核として、業務改革推進室を設置しました。この組織は、システム部門と現場部門のハブとして機能し、ERPの活用度向上と業務改善を推進しています。定期的な業務診断を実施し、システムの使用状況や効果を測定することで、継続的な改善サイクルを確立しています。
また、ヘルプデスク機能を社内に設置し、ユーザーからの問い合わせに迅速に対応できる体制を整えました。これにより、システムの利用率が向上し、導入効果を最大限に引き出すことに成功しています。
戦略的な人材育成プログラム
ERPを効果的に活用するためには、システムを使いこなす人材の育成が不可欠です。ある電子部品メーカーでは、以下のような体系的な人材育成プログラムを実施しています。
まず、役割別の教育プログラムを整備しました。一般ユーザー向けの基本操作研修から、キーユーザー向けの高度な活用研修、さらには管理者向けのシステム運用研修まで、段階的な教育体系を確立しています。
特に注力しているのが、データアナリスト人材の育成です。ERPから得られるデータを分析し、業務改善や意思決定に活用できる人材を計画的に育成しています。その結果、データに基づく改善提案が活発化し、業務効率が年々向上しています。
成功事例から学ぶベストプラクティス
これまでの導入事例から得られた知見を体系化し、成功のための重要なポイントをまとめます。
成功企業に共通する特徴
ERPの導入に成功している企業には、いくつかの共通点が見られます。ある機械メーカーの事例では、以下のような取り組みが成功の鍵となりました。
まず、トップマネジメントの強力なコミットメントです。経営層自らがプロジェクトの進捗を定期的にレビューし、必要な意思決定を迅速に行うことで、プロジェクトの推進力を維持しました。
また、現場の声を活かしながらも、全体最適の視点を失わない柔軟なアプローチを採用しています。過度なカスタマイズを避け、業務プロセスの標準化を進めることで、システムの保守性と拡張性を確保しています。
失敗を防ぐための重要ポイント
一方で、失敗を避けるために注意すべきポイントもあります。ある自動車部品メーカーでは、過去の失敗経験から以下のような教訓を得ています。
要件定義の段階で、現場の業務プロセスを十分に把握せず、理想的なプロセスを押し付けようとしたことで、システム導入後に混乱が生じました。この経験から、現状業務の可視化と段階的な改善の重要性を学びました。
また、データ移行の重要性を軽視したことで、本番稼働後に多くの問題が発生しました。この教訓を活かし、現在では徹底的なデータクレンジングとテストを実施しています。
ERPによるDX推進の成功事例
製造業におけるERP導入は、単なるシステム刷新ではなく、企業全体のDXを推進する重要な機会となります。ここでは、実際の成功事例を通じて、ERPがもたらす具体的な効果を見ていきましょう。
中堅機械メーカーのDX成功事例
従業員500名規模の機械メーカーA社では、ERPの導入を契機に全社的なDXを推進し、大きな成果を上げています。特筆すべきは、段階的なアプローチにより、確実に成果を積み上げていった点です。
第一段階では、生産管理と在庫管理の効率化に焦点を当て、リアルタイムな在庫把握と生産計画の最適化を実現しました。その結果、在庫回転率が40%向上し、生産リードタイムが30%短縮されています。
第二段階では、AIによる需要予測機能を追加し、さらなる効率化を達成しました。予測精度が向上したことで、適正在庫の維持が可能となり、機会損失と過剰在庫の同時削減に成功しています。
システム開発タロウ君のQ&A
Q1:「ERPの導入範囲はどのように決めればよいでしょうか?」
タロウ君:ERPの導入範囲は、段階的なアプローチをお勧めします。まず、最も効果が見込める基幹業務(例:生産管理や在庫管理)から始め、成果を確認しながら順次拡大していくのが賢明です。実際、ある金属加工メーカーでは、生産管理からスタートして2年かけて全社展開を完了し、投資効果を最大化することができました。
ポイントは、「パーフェクトを目指さない」ことです。初期段階では80%の完成度を目標とし、運用しながら徐々に改善していく方法が、現実的かつ効果的です。
Q2:「ERPの導入コストを抑えるコツはありますか?」
タロウ君:コスト削減のための重要なポイントは、パッケージの標準機能をできるだけ活用することです。カスタマイズは必要最小限に抑え、むしろ業務プロセスをパッケージに合わせる方向で検討することをお勧めします。
また、クラウド型ERPの活用も効果的です。初期投資を抑えられるだけでなく、バージョンアップやメンテナンスのコストも削減できます。ただし、選定の際は将来的なランニングコストまで含めて総合的に判断することが重要です。
Q3:「現場からの反発にはどう対処すべきでしょうか?」
タロウ君:現場の反発は、どのプロジェクトでも必ず直面する課題です。解決のカギは、「早期からの巻き込み」と「メリットの見える化」です。要件定義の段階から現場のキーマンを参画させ、彼らの意見を積極的に取り入れることで、プロジェクトへの当事者意識を高めることができます。
また、新システム導入後の具体的なメリット(例:残業時間の削減、ペーパーレス化による作業効率向上など)を数値で示すことも効果的です。一方で、すべての要望を受け入れるのではなく、全体最適の視点から適切な判断を下すことも重要です。
Q4:「データ移行でよく失敗するポイントは?」
タロウ君:データ移行の失敗は、本番稼働後の混乱に直結する重要な問題です。最も注意すべきは、「データの精度」と「マスターデータの整備」です。既存システムのデータをそのまま移行するのではなく、この機会に徹底的なクレンジングを行うことをお勧めします。
例えば、ある機械部品メーカーでは、データ移行の3ヶ月前から専任チームを設置し、品目マスターの棚卸しと整理を実施しました。その結果、約2万点あった品目を1.5万点まで整理し、新システムでのデータ管理の効率化に成功しています。
Q5:「グローバル展開する際の注意点は?」
タロウ君:グローバル展開で最も重要なのは、「標準化」と「ローカライズ」のバランスです。基幹業務プロセスは極力標準化し、国ごとの法制度対応や商習慣への対応のみをローカライズすることをお勧めします。
また、多言語・多通貨対応はもちろんのこと、時差を考慮したシステム運用体制の構築も重要です。さらに、海外拠点のネットワーク環境やユーザーのITリテラシーレベルも事前に確認し、必要な対策を講じることが成功のポイントとなります。
Q6:「保守・運用体制はどのように構築すべきですか?」
タロウ君:保守・運用体制は、「内製化」と「外部委託」のバランスが重要です。基幹業務に関わる重要な判断や改善提案は内製化し、定型的な保守作業は外部委託するというのが一般的なアプローチです。
特に重要なのは、社内にERPに精通した人材を育成することです。ある精密機器メーカーでは、若手社員を計画的に育成し、2年後には保守運用の70%を内製化することに成功しました。これにより、運用コストの削減だけでなく、システムの改善スピードも向上しています。
Mattockが提供するERP開発ソリューション
Mattockは、中堅製造業のERPプロジェクトを、構想段階から開発、運用まで一貫してサポートします。特に、以下の三つの強みを活かし、確実なプロジェクトの成功を支援します。
製造業に特化した知見とノウハウ
製造業における豊富な導入実績を基に、業界特有の課題やニーズに最適なソリューションを提供します。標準的なERPパッケージをベースに、製造業向けの機能を効率的に実装することで、コストパフォーマンスの高いシステム構築を実現します。
最新技術の効果的な活用
AI、IoT、クラウドなどの最新技術を、実務に即した形で導入します。ただし、技術ありきではなく、その技術が本当に業務改善に寄与するかを十分に検討した上で、最適な提案を行います。
確実な導入を実現するプロジェクト管理
豊富な経験を持つプロジェクトマネージャーが、計画から導入まで一貫して支援します。特に、要件定義フェーズでは、現場の声を丁寧に拾い上げながら、実現可能な要件をまとめ上げていきます。
まとめ:ERP開発成功のために
ERPの導入は、製造業のDX推進における重要な一歩です。しかし、その成功のためには、綿密な計画と確実な実行が不可欠です。特に重要なのは、以下の三点です。
まず、明確な目標設定です。「なぜERPを導入するのか」という根本的な目的を、経営層から現場まで共有することが重要です。次に、段階的なアプローチです。
すべてを一度に実現しようとせず、確実に成果を積み上げていく姿勢が必要です。そして最後に、人材育成です。システムの導入だけでなく、それを使いこなす人材の育成も同時に進めることが、真の意味でのDX実現につながります。
Mattockは、これらの要素を総合的に支援し、お客様のERP開発プロジェクトを成功に導きます。まずは気軽にご相談ください。
経験豊富なコンサルタントが、貴社の課題とニーズに最適なソリューションをご提案いたします。
ERPによるDX推進は、製造業の未来を切り開く重要な鍵となります。この記事が、皆様のプロジェクト成功への一助となれば幸いです。