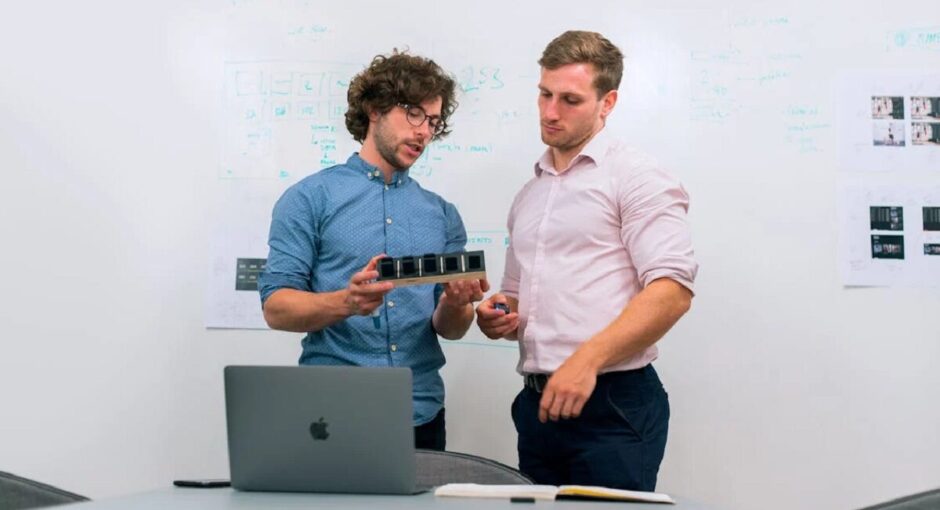
製造業界を取り巻く環境は、かつてないほどの速さで変化を続けています。特に中堅メーカーにとって、開発期間の短縮やコスト削減、品質管理の徹底は、生き残りをかけた重要な課題となっています。
このような状況下で注目を集めているのが、OEM開発という選択肢です。OEM開発は、自社の強みを活かしながら、開発期間の短縮やコスト削減を実現できる効果的な戦略として、多くの中堅メーカーに採用されています。特に近年は、AI/IoTなどの最新技術を活用したOEM開発により、さらなる可能性が広がっています。
この記事では、中堅メーカーがOEM開発を成功させるために必要な知識や戦略、具体的な事例を詳しく解説します。基礎的な概念から最新のトレンドまで、実践的な情報を網羅的に提供することで、読者の皆様の課題解決に貢献することを目指しています。
この記事を読んでほしい人
- 製品開発のスピードアップを目指す中堅メーカーの経営者
- 開発コストの削減を検討している製造業の担当者
- 品質管理体制の強化を考えている企業の責任者
- OEM開発による新規事業の立ち上げを検討している方
- グローバル展開を視野に入れている製造業の経営者
この記事で分かること
- OEM開発による開発期間短縮とコスト削減の具体的方法
- 信頼できるOEMパートナーの選定基準と評価方法
- 品質管理体制の構築と運用のベストプラクティス
- AI/IoTを活用した最新のOEM開発手法
- グローバル展開を見据えたOEM戦略の立て方
OEM開発の基礎知識
製品開発における重要な選択肢であるOEM開発について、その本質と特徴を理解することは、戦略立案の第一歩となります。
このセクションでは、OEM開発に関する基本的な知識から最新の市場動向まで、体系的に解説します。
OEM開発の定義と基本概念
OEM(Original Equipment Manufacturer)開発とは、他社のブランドで販売される製品の製造を請け負う事業形態を指します。
発注側は自社ブランドでの製品展開が可能となり、製造側は生産設備の有効活用が図れるという、双方にメリットのあるビジネスモデルです。近年では、製造だけでなく設計や開発の一部を委託するケースも増加しています。
OEMとODMの違いを理解する
製造委託の形態には、OEMの他にODM(Original Design Manufacturing)があります。
ODMは製品の設計から製造までを一貫して委託する形態で、より広範な業務委託が特徴です。OEM開発では製品仕様は発注側が決定するのに対し、ODMでは受託側が製品開発から担当することが一般的です。選択にあたっては、自社の強みや経営資源を考慮する必要があります。
OEM開発のメリットと課題
OEM開発の最大のメリットは、開発期間の短縮とコスト削減です。
専門メーカーの技術やノウハウを活用することで、高品質な製品を効率的に生産することが可能となります。一方で、品質管理や知的財産権の保護、コミュニケーションの円滑化など、適切に管理すべき課題も存在します。
グローバル市場におけるOEM開発の現状
グローバル化の進展に伴い、OEM開発の形態も多様化しています。
アジア地域を中心とした製造拠点の活用や、先進国企業との技術提携など、国際的な協力関係の構築が活発化しています。特に、電機・電子機器、自動車部品、アパレルなどの分野で、グローバルなOEM開発が拡大しています。
OEM開発を取り巻く最新トレンド
デジタル技術の進化により、OEM開発の在り方も変化しています。
クラウドを活用した設計データの共有や、AIによる品質管理の自動化など、新たな技術の導入が進んでいます。また、環境負荷の低減や持続可能性への配慮など、社会的要請に応えるOEM開発も増加しています。
業界別にみるOEM開発の特徴
業界によってOEM開発の形態や重要度は異なります。
家電業界では製品のライフサイクルの短縮化への対応として、自動車業界では技術の高度化への対応として、それぞれOEM開発が活用されています。業界特性を理解し、適切な戦略を立案することが重要です。
次のセクションでは、中堅メーカーが直面する具体的な課題と、OEM開発による解決方法について詳しく解説します。
中堅メーカーの抱える課題と解決策
中堅メーカーは、大手企業とは異なる独自の課題に直面しています。
このセクションでは、一般的な課題とその具体的な解決方法について、実践的な視点から詳しく解説します。
リソース不足の現状と対策
中堅メーカーにとって、人材・資金・時間といったリソースの不足は深刻な課題となっています。
特に研究開発部門では、専門性の高い人材の確保が困難であり、技術革新への対応が遅れがちです。このような状況に対して、OEM開発では専門メーカーの技術力を活用することで、自社リソースの最適化が可能となります。
人材不足への対応戦略
専門性の高い技術者の採用や育成には、多大な時間と費用が必要です。
OEM開発を活用することで、パートナー企業の専門家チームを即戦力として活用できます。これにより、最新技術への対応や品質管理の向上を、自社の人材育成を待たずに実現することが可能となります。
資金的制約の克服
研究開発施設や製造設備への投資は、中堅メーカーにとって大きな負担となります。OEM開発では、これらの初期投資を抑制しながら、高品質な製品開発を実現できます。また、生産量に応じた柔軟な製造体制の構築も可能となり、資金効率の向上にも貢献します。
開発期間短縮の必要性と実現方法
市場ニーズの急速な変化に対応するため、製品開発のスピードアップは不可欠です。従来の自社開発では、市場投入のタイミングを逃す可能性が高くなっています。
スピード重視の開発プロセス
OEM開発では、パートナー企業の既存技術や設備を活用することで、開発期間を大幅に短縮できます。特に、試作品の製作や品質テストなど、時間のかかるプロセスを効率化することが可能です。
市場投入時期の最適化
競合他社に先駆けて新製品を市場に投入することは、競争優位性の確保に重要です。OEM開発を活用することで、市場動向に応じた柔軟な製品開発と、タイムリーな市場投入を実現できます。
コスト削減の課題と効率化
原材料費の高騰や人件費の上昇により、製造コストの管理は一層重要性を増しています。OEM開発では、スケールメリットを活かした材料調達や、効率的な生産体制の構築が可能です。
製造コストの最適化
パートナー企業の生産設備と専門知識を活用することで、製造工程の効率化と品質の安定化を同時に実現できます。また、生産量に応じた柔軟な製造体制により、在庫管理コストの削減も可能となります。
開発コストの削減
自社での研究開発にかかる費用を抑制しながら、高品質な製品開発を実現できます。特に、専門性の高い技術領域では、パートナー企業のノウハウを活用することで、効率的な開発が可能となります。
品質管理の重要性と体制構築
製品の品質は、企業の評価に直結する重要な要素です。OEM開発では、パートナー企業の品質管理システムを活用することで、高い品質水準を維持することができます。
品質基準の確立
パートナー企業との緊密な連携により、明確な品質基準を設定し、その遵守を確保することが重要です。定期的な品質監査や改善活動を通じて、継続的な品質向上を図ることができます。
トレーサビリティの確保
製造工程の各段階における品質管理情報を適切に記録し、問題発生時の原因究明や改善対策に活用することが可能です。これにより、品質問題の早期発見と迅速な対応が実現できます。
OEM開発による具体的な解決方法
中堅メーカーの課題解決には、戦略的なOEM開発の活用が効果的です。
パートナー企業の選定から、開発プロセスの確立、品質管理体制の構築まで、総合的なアプローチが必要となります。
段階的な導入戦略
OEM開発の導入は、小規模なプロジェクトからスタートし、成功体験を積み重ねることが重要です。これにより、自社に適したOEM開発のモデルを確立することができます。
パートナーシップの構築
信頼関係に基づく長期的なパートナーシップの構築が、OEM開発成功の鍵となります。定期的なコミュニケーションと相互理解の促進により、より効果的な協力関係を築くことができます。
次のセクションでは、OEM開発を成功に導くための具体的な戦略について、詳しく解説します。
OEM開発成功のための戦略
OEM開発を成功に導くためには、綿密な計画と適切な実行が不可欠です。
このセクションでは、明確な目標設定から効果的なパートナーシップの構築まで、成功のための具体的な戦略を解説します。
明確な目標設定の方法
企業の成長戦略に基づいた明確な目標設定は、OEM開発の成否を左右する重要な要素です。市場分析や自社の強み弱みの評価を通じて、具体的な数値目標を設定することが重要となります。
戦略的目標の設定
中長期的な視点から、売上目標や市場シェア、製品ラインナップの拡充など、具体的な目標を設定します。これらの目標は、定期的に見直しと修正を行うことで、市場環境の変化に柔軟に対応することができます。
KPIの設定と管理
開発期間、製造コスト、品質基準など、具体的な指標を設定し、定期的なモニタリングを行います。数値化された指標を用いることで、プロジェクトの進捗状況を客観的に評価することが可能となります。
パートナー選定の基準と評価
最適なパートナー企業の選定は、OEM開発成功の重要な要素です。技術力、生産能力、品質管理体制など、多角的な視点からの評価が必要となります。
技術力の評価
パートナー企業の保有する技術やノウハウが、自社の製品開発ニーズに合致しているかを慎重に評価します。過去の開発実績や技術者の専門性なども、重要な評価基準となります。
生産能力の確認
安定的な製品供給を実現するため、パートナー企業の生産設備や生産管理体制を詳細に確認します。需要変動への対応力や、緊急時の供給体制なども考慮する必要があります。
効果的なコミュニケーション戦略
パートナー企業との円滑なコミュニケーションは、プロジェクトの成功に不可欠です。定期的な情報共有と問題解決の仕組みづくりが重要となります。
コミュニケーション体制の構築
プロジェクトマネージャーの選任や、定例会議の設定など、体系的なコミュニケーション体制を確立します。オンラインツールの活用により、リアルタイムでの情報共有も可能となります。
情報共有の仕組み作り
設計図面や品質データなど、重要な情報を安全かつ効率的に共有できる環境を整備します。クラウドシステムの活用により、グローバルな協業体制も構築可能です。
リスク管理と品質保証
OEM開発に伴うリスクを適切に管理し、製品品質を確保することは極めて重要です。予防的なリスク管理と、効果的な品質保証システムの構築が求められます。
リスクアセスメント
開発段階から想定されるリスクを洗い出し、対応策を準備します。技術的リスク、市場リスク、供給chain上のリスクなど、包括的な評価が必要です。
品質保証システム
製造工程における品質管理基準の設定や、定期的な品質監査の実施など、体系的な品質保証体制を構築します。トレーサビリティの確保も重要な要素となります。
契約における重要ポイント
適切な契約締結は、安定的なOEM開発の基盤となります。知的財産権の保護や責任範囲の明確化など、重要な事項を漏れなく契約に盛り込む必要があります。
権利義務の明確化
製造物責任や品質保証の範囲、知的財産権の帰属など、重要な事項を明確に規定します。将来的な紛争を予防するため、詳細な取り決めが必要です。
秘密保持の取り決め
製品設計情報や製造ノウハウなど、機密情報の保護に関する取り決めを行います。従業員教育や情報管理体制の整備も重要となります。
実行計画の策定と管理
具体的な実行計画の策定と、その適切な管理は、プロジェクトの成功に直結します。スケジュール管理や予算管理など、総合的なプロジェクト管理が求められます。
マイルストーンの設定
開発から量産開始までの工程を細分化し、具体的なマイルストーンを設定します。進捗状況を定期的に確認し、必要に応じて計画の修正を行います。
進捗管理の仕組み
ガントチャートやプロジェクト管理ツールを活用し、効率的な進捗管理を実現します。問題発生時の早期発見と迅速な対応が可能となります。
次のセクションでは、最新技術を活用したOEM開発の具体的な事例について解説します。
最新技術を活用したOEM開発
デジタル技術の進化は、OEM開発の在り方を大きく変えつつあります。
このセクションでは、AI/IoTをはじめとする最新技術の活用事例と、それらがもたらす新たな可能性について解説します。
AI/IoT技術の実践的活用
製造業におけるAI/IoT技術の活用は、生産性向上と品質管理の強化に大きく貢献しています。特にOEM開発では、これらの技術を効果的に活用することで、競争力の向上につながっています。
AI技術による品質管理の革新
画像認識AIを活用した製品検査システムにより、人的ミスを削減し、検査精度を向上させることが可能となっています。また、製造データの分析により、不良品発生の予兆を早期に発見し、予防的な品質管理を実現することができます。
IoTによる生産管理の効率化
製造設備にセンサーを設置し、稼働状況をリアルタイムでモニタリングすることで、生産効率の向上と設備保全の最適化が可能となります。収集したデータを分析することで、生産計画の精度向上にも活用できます。
デジタルトランスフォーメーションの影響
製造業のデジタルトランスフォーメーションは、OEM開発のプロセスそのものを変革しつつあります。従来の製造工程に留まらず、開発から販売までの全工程でデジタル化が進んでいます。
デジタル設計ツールの進化
3DCADやシミュレーションソフトウェアの発展により、試作品製作の効率化と開発期間の短縮が実現しています。クラウドベースの設計環境により、パートナー企業との共同開発もスムーズに行えるようになっています。
データ駆動型の意思決定
市場動向や顧客ニーズのデータ分析により、製品企画の精度向上が可能となっています。また、製造工程の各種データを活用することで、生産効率の最適化と品質向上を同時に実現できます。
サステナビリティへの対応
環境負荷の低減や持続可能な製造プロセスの確立は、現代のOEM開発における重要なテーマとなっています。最新技術の活用により、これらの課題に効果的に対応することが可能です。
環境配慮型製造プロセス
エネルギー消費の可視化と最適化により、製造工程における環境負荷を低減することができます。また、リサイクル材料の活用や廃棄物の削減など、環境に配慮した製造プロセスの確立も進んでいます。
サプライチェーンの最適化
IoT技術を活用した在庫管理と物流の効率化により、環境負荷の低減とコスト削減を同時に実現することが可能です。また、ブロックチェーン技術の活用により、サプライチェーンの透明性向上も図られています。
今後のトレンド予測
OEM開発における技術革新は、さらなる進化を続けています。将来的な展望を見据えた戦略立案が、競争力の維持向上には不可欠です。
次世代製造技術の展望
5Gの普及によるリアルタイム制御の高度化や、AIによる自律的な製造システムの実現など、製造技術の革新が進んでいます。これらの技術を効果的に活用することで、さらなる生産性向上が期待できます。
グローバル協業の進化
クラウド技術やコミュニケーションツールの発展により、地理的な制約を越えたグローバルな協業体制の構築が容易になっています。これにより、最適なパートナー選択の幅が大きく広がっています。
次のセクションでは、これらの最新技術を活用した具体的な成功事例について紹介します。
具体的な成功事例
OEM開発の成功事例を分析することで、実践的な知見を得ることができます。
このセクションでは、様々な業界における具体的な成功事例を紹介し、その成功要因について詳しく解説します。
家電メーカーの事例
中堅家電メーカーA社は、開発期間の短縮と品質向上を同時に実現し、市場シェアの拡大に成功しました。従来18ヶ月かかっていた製品開発期間を12ヶ月まで短縮し、競合他社に先駆けて新製品を市場投入することができました。
成功のポイント分析
A社は、AIを活用した品質管理システムを導入し、不良品率を従来比60%削減することに成功しました。また、パートナー企業との共同開発体制を構築し、技術ノウハウの相互活用により、製品の性能向上も実現しています。
課題解決のプロセス
開発初期段階から品質管理部門とパートナー企業が密接に連携し、潜在的な問題点の早期発見と解決を図りました。また、定期的なレビュー会議の実施により、開発の進捗管理と品質確保を徹底しています。
化粧品メーカーの事例
中堅化粧品メーカーB社は、OEM開発を活用して新規市場への参入を果たしました。特に、高機能性化粧品分野での商品開発において、パートナー企業の技術力を最大限に活用しています。
市場戦略と製品開発
B社は、パートナー企業の持つ独自技術を活用し、従来にない機能性を持つ製品の開発に成功しました。市場調査から製品開発、販売戦略まで、一貫した計画のもとでプロジェクトを推進しています。
ブランド価値の向上
品質の安定性と製品の独自性により、市場での評価を着実に高めています。売上は前年比150%を達成し、ブランド認知度も大幅に向上しました。
自動車部品メーカーの事例
自動車部品メーカーC社は、電動化対応部品の開発においてOEM開発を活用し、技術革新への対応を実現しました。グローバル市場での競争力強化に成功しています。
技術革新への対応
電気自動車向け部品の開発において、パートナー企業の先進技術を活用することで、開発リスクの軽減と開発期間の短縮を実現しました。特に、高電圧対応部品の安全性確保において、高い評価を得ています。
グローバル展開の実現
品質管理体制の国際標準化により、グローバル市場での信頼性を確立しています。現在では、年間売上の40%を海外市場が占めるまでに成長しています。
食品メーカーの事例
食品メーカーD社は、健康志向の高まりに対応した新製品開発において、OEM開発を効果的に活用しています。特に、機能性食品分野での商品展開が好評を博しています。
商品開発の革新
パートナー企業の持つ食品加工技術と、自社の市場ニーズ分析を組み合わせることで、独自性の高い商品開発を実現しました。特に、保存料不使用の長期保存可能商品の開発が市場で高い評価を得ています。
生産体制の最適化
季節変動の大きい需要に対して、柔軟な生産体制を構築することに成功しています。これにより、在庫管理コストの削減と供給安定性の確保を両立させています。
成功事例から学ぶ重要ポイント
これらの成功事例に共通する重要なポイントとして、以下の要素が挙げられます。
戦略的パートナーシップ
単なる製造委託ではなく、技術開発から市場展開まで、包括的な協力関係を構築することが重要です。相互の強みを活かした価値創造が、成功の鍵となっています。
品質管理の徹底
製品の品質は、企業の信頼性とブランド価値に直結します。先進的な品質管理システムの導入と、継続的な改善活動の推進が不可欠です。
次のセクションでは、OEM開発における注意点とリスク対策について解説します。
OEM開発における注意点とリスク対策
OEM開発を成功に導くためには、想定されるリスクを事前に把握し、適切な対策を講じることが不可欠です。このセクションでは、主要なリスク要因とその対策について、実践的な観点から解説します。
知的財産権の保護
企業の競争力の源泉となる知的財産権の保護は、OEM開発において最も重要な課題の一つです。技術情報や製品設計情報の適切な管理が必要となります。
契約による権利保護
知的財産権の帰属や使用範囲について、契約書で明確に規定することが重要です。特許権、意匠権、商標権などの取り扱いについて、詳細な取り決めを行う必要があります。
情報管理体制の構築
機密情報の漏洩を防止するため、適切な情報管理体制を構築することが必要です。アクセス権限の設定や、セキュリティ対策の実施など、具体的な防止策を講じることが重要です。
品質管理体制の構築
製品の品質は、企業の信頼性に直結する重要な要素です。パートナー企業との協力のもと、効果的な品質管理体制を構築する必要があります。
品質基準の明確化
製品の品質基準や検査方法について、パートナー企業と明確な合意を形成することが重要です。定期的な品質監査の実施や、改善活動の推進も必要となります。
トレーサビリティの確保
製品の製造履歴や品質データを適切に管理し、問題発生時の原因究明や対策立案に活用できる体制を整備することが重要です。
コスト管理の重要性
OEM開発におけるコスト管理は、プロジェクトの収益性を左右する重要な要素です。適切なコスト管理体制の構築が必要となります。
コスト構造の分析
製造原価の内訳を詳細に分析し、コスト削減の余地を特定することが重要です。材料費や加工費など、各要素について継続的な見直しを行う必要があります。
原価管理の徹底
目標原価の設定と実績管理を通じて、コストの適正化を図ることが重要です。パートナー企業との協力のもと、継続的な原価低減活動を推進する必要があります。
トラブル発生時の対応策
製品不具合や納期遅延など、様々なトラブルに対する適切な対応策を事前に準備することが重要です。
危機管理体制の整備
トラブル発生時の対応手順や責任体制について、あらかじめ明確化しておくことが必要です。パートナー企業との連携体制も含めて、具体的な対応策を準備しておく必要があります。
補償対応の取り決め
製品不具合による損害賠償など、トラブル発生時の補償について、契約書で明確に規定することが重要です。責任範囲と補償内容について、詳細な取り決めを行う必要があります。
次のセクションでは、パートナー企業との関係構築について解説します。
パートナー企業との関係構築
OEM開発の成功は、パートナー企業との良好な関係構築にかかっています。
このセクションでは、長期的な視点に立った関係構築の方法と、効果的なコミュニケーション戦略について解説します。
長期的な関係構築のポイント
単なる取引関係を超えた、戦略的パートナーシップの構築が重要です。相互の成長を目指した協力関係を築くことで、持続的な発展が可能となります。
また、定期的な経営層同士の対話や、中長期的な事業計画の共有により、相互理解を深めることが重要です。また、共同での技術開発や市場開拓など、価値創造に向けた取り組みを推進することで、信頼関係を強化することができます。
効果的なコミュニケーション方法
日常的なコミュニケーションの質を高めることは、プロジェクトの成功に直結します。適切なコミュニケーション体制の構築が必要となります。
また、定例会議の開催やプロジェクト管理ツールの活用により、円滑な情報共有を実現することが重要です。特に、開発進捗や品質情報など、重要な情報については、リアルタイムでの共有が求められます。
相互の成長戦略
パートナー企業との協力関係を通じて、両社の成長を実現することが重要です。技術力の向上や新規事業の開発など、様々な面での相乗効果が期待できます。
さらに、新技術の開発や新製品の企画など、共同での取り組みを通じて、両社の競争力を高めることができます。市場ニーズの変化や技術トレンドを見据えた、戦略的な協力関係の構築が求められます。
教えてシステム開発タロウくん!!
OEM開発のシステム戦略について、オフショア開発のエキスパート、タロウが実践的なアドバイスをお届けします!効率的な開発体制と品質管理のポイントを解説していきましょう。
Q: OEM開発のシステム化で、特に重要な領域は?
A: 「設計管理」と「品質管理」の統合がカギです!設計図面や部品表(BOM)の管理をクラウド化し、取引先との情報共有を効率化。ベトナムには製造業向けシステム開発の経験豊富なエンジニアが多いんです。例えば、CADデータと品質管理システムを連携させることで、設計変更の影響を即座に把握可能。また、部品の共通化率を分析することで、コスト削減のポイントも明確になります。特に重要なのは、バージョン管理と承認フローの仕組みですよ。
Q: 開発期間短縮のための、効果的なシステム構築は?
A: 「並行開発」と「自動化」が決め手です!プロジェクト管理ツールと設計システムを連携させて、タスクの進捗をリアルタイムに可視化。シミュレーションツールも活用して、試作前の問題点を早期に発見。例えば、デジタルツインを活用することで、設計段階での検証が可能に。これにより、試作回数を30%削減できた事例もあります。また、テスト工程の自動化で、品質確認のスピードアップも実現できますよ。
Q: 取引先とのコミュニケーション効率化のコツは?
A: 「情報共有プラットフォーム」の構築が重要です!仕様書や図面の管理、進捗報告、課題管理を一元化。例えば、クラウドベースのポータルサイトで、リアルタイムなコミュニケーションを実現。変更管理も履歴が追えるように。また、AI翻訳ツールを統合して、グローバルでの情報共有もスムーズに。セキュアな環境で、取引先ごとにアクセス権限を細かく設定できる仕組みも必須ですよ。
Q: コスト管理と原価低減を実現するシステム設計のポイントは?
A: 「データの見える化」と「予測分析」がベストです!部品コスト、製造コスト、物流コストなどを統合的に分析。AIを活用して、コスト削減のポテンシャルを発見します。例えば、類似部品の共通化提案や、最適な調達先の提案機能を実装。また、為替変動の影響シミュレーションも可能に。在庫最適化機能と連携させることで、トータルコストの削減が実現できますよ。
Q: 品質保証と技術ノウハウの管理で、注意すべき点は?
A: 「トレーサビリティ」と「ナレッジ管理」が重要です!製造工程の各データを紐づけて管理し、不具合発生時の原因究明を容易に。IoTセンサーからのデータも活用して、品質予兆管理を実現。また、過去の開発ノウハウをデータベース化し、新規開発時に活用できる仕組みを構築。図面だけでなく、設計意図や過去の課題解決方法なども含めて、ナレッジとして蓄積することが大切。特に、セキュリティ面では、機密情報の管理レベルを細かく設定できる仕組みが必要ですよ。
まとめ
OEM開発は、中堅メーカーが直面する様々な課題を解決し、持続的な成長を実現するための有効な戦略です。この記事では、OEM開発の基礎知識から具体的な実践方法まで、包括的に解説してきました。
OEM開発の成功には戦略的なパートナー選びと綿密な計画立案が不可欠です。特に品質管理とコスト管理の両立、そして知的財産権の保護は重要な要素となります。
デジタル技術の進化により、OEM開発の形態も大きく変化していくことが予想されます。AI/IoTの活用やデジタルトランスフォーメーションの推進により、さらなる効率化と価値創造が期待できます。
Mattockのご提案
Mattockは、20年以上にわたり中堅メーカーのOEM開発を支援してきた実績があります。高度な技術力と柔軟な対応力を活かし、お客様の課題解決に最適なソリューションをご提案いたします。まずはお気軽にご相談ください。
お問い合わせ
OEM開発に関するご相談は、下記のフォームよりお願いいたします。経験豊富な担当者が、貴社の課題やニーズに合わせた具体的なご提案をさせていただきます。